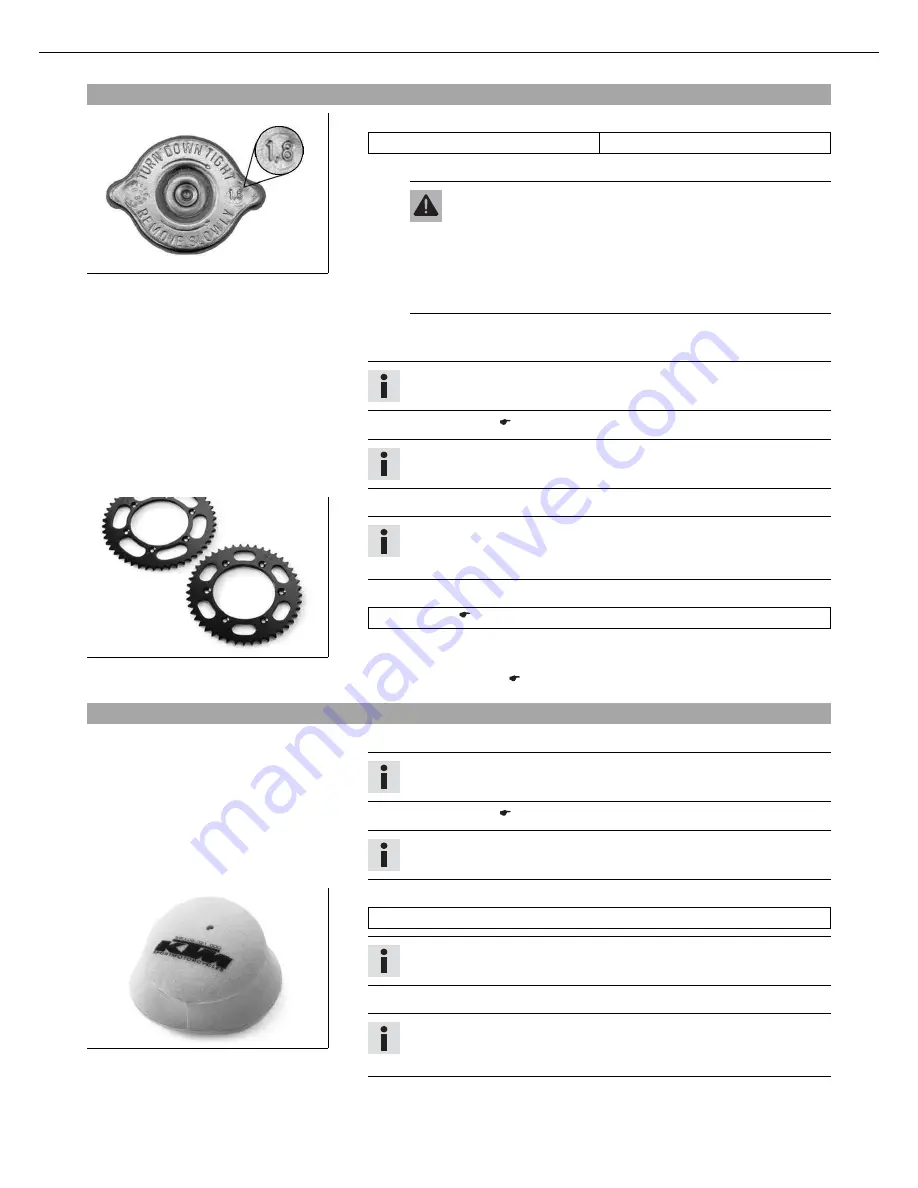
GENERAL TIPS AND HINTS ON PUTTING INTO OPERATION
18
6.7
Preparations for riding at high temperatures and riding slowly
600872-10
–
Check the radiator cap.
Value on radiator cap
1.8 bar (26 psi)
» If the value displayed does not meet specifications:
Warning
Danger of scalding
During motorcycle operation, the coolant gets
very hot and is under pressure.
–
Do not remove the radiator cap, radiator hoses or other cooling
system components when the engine is hot. Allow the engine
and cooling system to cool down. In case of scalding, rinse
immediately with lukewarm water.
–
Change the radiator cap.
–
Seal the air filter box.
x
Tip
Seal the air filter box at the edges to prevent dirt from entering.
–
Clean the air filter.
x
(
p. 63)
Info
Check the air filter approx. every 30 minutes.
600868-01
–
Adjust the secondary ratio to the nature of the terrain.
Info
The engine oil heats up quickly if the clutch needs to be activated
frequently because the secondary ratio is too long.
–
Clean the chain.
Chain cleaner (
p. 96)
–
Clean the radiator fins.
–
Carefully align bent radiator fins.
–
Check the coolant level. (
p. 59)
6.8
Preparations for riding at low temperatures and in snow
–
Seal the air filter box.
x
Tip
Seal the air filter box at the edges to prevent dirt from entering.
–
Clean the air filter.
x
(
p. 63)
Info
Check the air filter approx. every 30 minutes.
600870-01
–
Mount the rain cover for the air filter.
Rain cover for air filter (59006021000)
Info
Follow the
KTM PowerParts
mounting instructions.
–
Adjust the carburetor jetting and setting.
Info
The recommended carburetor tuning is available from your authorized KTM
workshop.
Содержание 125 SX 2010
Страница 2: ...OWNERSMANUAL2010 250 SX 250 300 XC XC W EXC EXC SixDays ...
Страница 3: ...OWNER S MANUAL 2010 125 SX 150 SX 250 SX Art no 3211480en ...
Страница 91: ...TECHNICAL DATA SHOCK ABSORBER 89 Shock absorber oil p 95 SAE 2 5 ...
Страница 93: ...91 ...
Страница 103: ...INDEX 101 U Use definition 5 V View of vehicle right rear 8 W Warranty 5 Wiring diagram 92 93 Work rules 5 ...
Страница 222: ...119 ...
Страница 223: ...WIRING DIAGRAM 120 ...
Страница 226: ...WIRING DIAGRAM 123 ...
Страница 304: ...1 2 3 4 7 12 Art No 3 206 088 E Repair manual KTM 250 300 ...
Страница 306: ...bl bk 6 7 8 9 7 14 Art No 3 206 088 E Repair manual KTM 250 300 ...
Страница 308: ...1 2 3 4 5 7 16 Art No 3 206 088 E Repair manual KTM 250 300 ...
Страница 323: ...9 1 Art No 3 206 088 E Repair manual KTM 250 300 TROUBLE SHOOTING TROUBLE SHOOTING 250 300 9 2 INDEX 9 ...
Страница 393: ...11 15 PERIODIC MAINTENANCE SCHEDULE 2010 250 SX ...
Страница 394: ...11 16 Repair manual KTM 250 300 Art No 3 206 088 E ...
Страница 395: ...11 17 PERIODIC MAINTENANCE SCHEDULE 2010 250 300 XC XC W EXC EXC SIX DAYS 250 300 EXC E EXC E SIX DAYS ...
Страница 396: ...11 18 Repair manual KTM 250 300 Art No 3 206 088 E ...
Страница 397: ...11 19 ...
Страница 408: ...EXC 250 300 2005 EXC SIX DAYS 250 300 05 06 12 10 Art No 3 206 088 E Repair manual KTM 250 300 ...
Страница 409: ...EXC 250 300 2005 EXC SIX DAYS 250 300 05 06 12 11 ...
Страница 410: ...e EXC 250 300 2005 EXC SIX DAYS 250 300 05 06 12 12 Art No 3 206 088 E Repair manual KTM 250 300 ...
Страница 411: ...right front flasher right rear flasher left rear flasher EXC 250 300 2005 EXC SIX DAYS 250 300 05 06 12 13 ...
Страница 412: ...EXC 250 300 2005 EXC SIX DAYS 250 300 05 06 12 14 Art No 3 206 088 E Repair manual KTM 250 300 ...
Страница 413: ...EXC 250 300 2005 EXC SIX DAYS 250 300 05 06 12 15 ...
Страница 414: ...EXC USA 250 2005 12 16 Art No 3 206 088 E Repair manual KTM 250 300 ...
Страница 416: ...12 18 Repair manual KTM 250 300 Art No 3 206 088 E ...
Страница 430: ...Repair manual KTM 250 300 Art No 3 206 088 E 12 32 250 EXC EXC Six Days EU AUS 2008 2009 ...
Страница 431: ...12 33 250 300 XC USA 2008 250 CX W ZA 2008 2009 ...
Страница 432: ...Repair manual KTM 250 300 Art No 3 206 088 E 12 34 250 XC W USA 2008 09 300 XC W USA ZA 2008 09 ...
Страница 433: ...12 35 300 EXC E EXC E SixDays EU AUS 2008 2009 ...
Страница 435: ...12 37 CABLE COLOURS bl black ye yellow bu blue gn green re red wh white br brown or orange pi pink gr grey pu purple ...
Страница 437: ...12 39 250 SX 2010 ...
Страница 438: ...12 40 Repair manual KTM 250 300 Art No 3 206 088 E ...
Страница 439: ...12 41 250 EXC EU 2010 ...
Страница 440: ...12 42 Repair manual KTM 250 300 Art No 3 206 088 E ...
Страница 441: ...12 43 250 300 EXC 2010 ...
Страница 442: ...12 44 Repair manual KTM 250 300 Art No 3 206 088 E ...
Страница 443: ...12 45 250 300 XC XC W 2010 ...
Страница 444: ...12 46 Repair manual KTM 250 300 Art No 3 206 088 E ...
Страница 445: ...REPAIRMANUAL2004 2010 2004 2005 DCC ...
Страница 553: ...1 7 T 14031 Dismounting mounting tool ...
Страница 559: ...2 6 Exploded view PDS 5018 SXS SMR 2005 2006 ...
Страница 561: ...2 8 Exploded view PDS 5018 SXS 2007 ...
Страница 664: ...REPAIRMANUAL2004 2010 WP 4860 MXMA Closed Cartridge WP 4860 MXMA PA Preload Adjuster WP 4357 4860 MXMA ...
Страница 682: ...Workshop manual Product Exploded View Disassembly assembling 3 4860 MXMA Frontfork 4860 MXMA 2003 05 2002 Exploded view ...
Страница 739: ...1 7 T 14 030 Adaptor T 14 033 Assembling tool ...
Страница 741: ...2 2 Repair manual WP Fork Closed Cartridge Art No 3 211 199 E Exploded view SXS 2005 ...
Страница 746: ...2 7 Exploded view SXS 2006 ...
Страница 751: ...2 12 Repair manual WP Fork Closed Cartridge Art No 3 211 199 E Exploded view SX 2007 ...
Страница 756: ...2 17 Exploded view Fork SXS 2007 ...
Страница 820: ... Assemble the O ring 1 Apply the O ring with T158 Apply the inside O ring 2 with T158 Membrane holder complete 4 55 1 2 ...