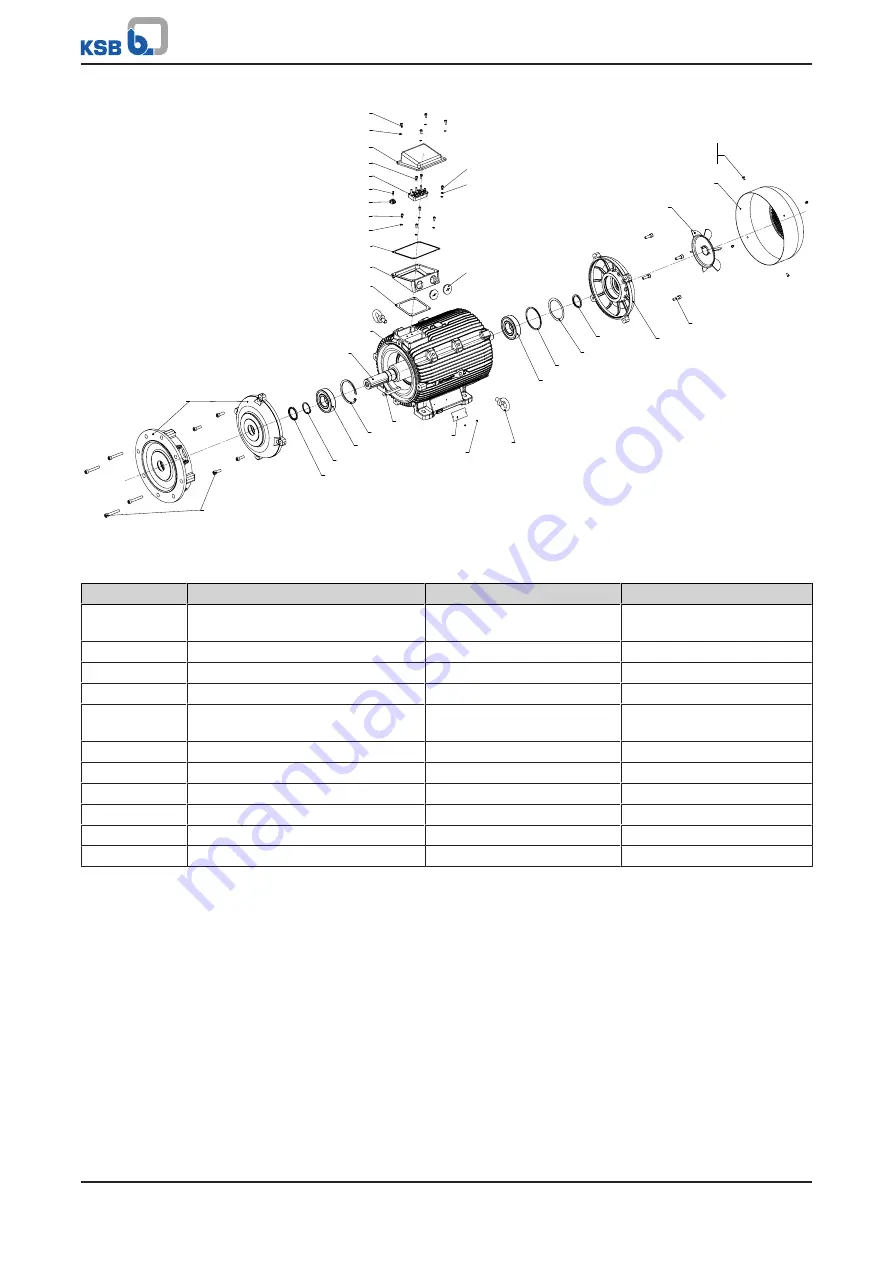
9 Related Documents
43 of 52
KSB SuPremE
914.19
900
900.04
914.14
914.07
930.07
421.01
950
903
81-36
914.01
99-9.02
831
914.52
930.52
832
UG1492278
360.02
914.02
970.02
932.01
321.02
421.02
932.02
835
81-22
914.06
930.06
80-1
930.18
914.18
360.01
550
836
99-9.01
818
321.01
940
Fig. 8:
Variant made of grey cast iron
Table 28:
List of components
Part No.
Description
Part No.
Description
80-1
Motor unit (motor housing with
stator)
835
Terminal board
81-22
Terminal box cover
836
Terminal strip
81-36
Terminal box base
900.04
Bolt/screw
99-9.01/.02
Set of sealing elements
903
Screw plug
321.01/.02
Radial ball bearing
914.01/.02/.06/.07/.14/.18/.19/.
52
Hexagon socket head cap
screw
360.01/.02
Bearing cover
930.06/.07/.18/.52
Safety device
421.01/.02
Lip seal
932.01/.02
Circlip
550
Disc
940
Key
818
Rotor
950
Spring
831
Fan impeller
970.02
Name plate
832
Fan hood
Содержание SuPreme Series
Страница 1: ...Synchronous Reluctance Motor KSB SuPremE Installation Operating Manual ...
Страница 49: ......
Страница 50: ......
Страница 51: ......