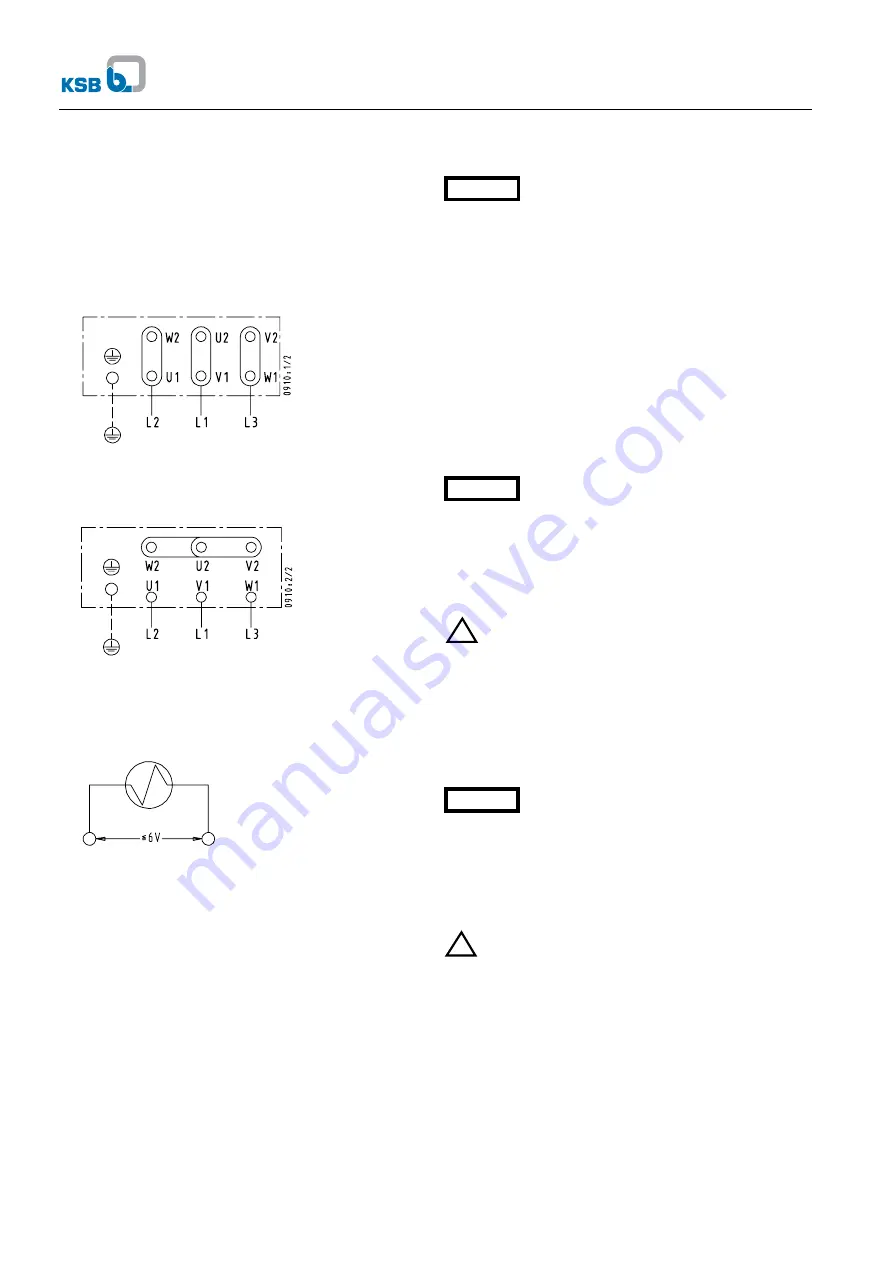
5.7.1 Motor connection
In compliance with DIN VDE 0530 – Part 8, the three-phase
motors are always wired for clockwise rotation (looking at the
motor shaft stub).
The pump’s direction of rotation is anti-clockwise (looking at
the suction flange).
For the motor’s direction of rotation to match the pump’s direc-
tion of rotation, the motor must be connected as shown in fig.
5.7-1 or 5.7-2, as applicable.
n configuration (low voltage)
Fig. 5.7-1 Connection diagram for three-phase motors,
n configuration
Y configuration (high voltage)
Fig. 5.7-2 Connection diagram for three-phase motors,
Y configuration
If required, connect the PTC resistors as per DIN
44081/44082 with the tripping unit in accordance with fig. 5.7-
3.
Fig. 5.7-3 Connection diagram for PTC resistors
5.7.2 Setting the time relay
Make sure that in the case of three-phase motors with star-
delta starting method switching over from star to delta will be
effected at very short intervals. Prolonged switch-over inter-
vals will result in pump damage.
Time relay setting for star-delta starting: <3 s.
5.7.3 Checking the direction of rotation
The motor’s direction of rotation must correspond to the direc-
tion indicated by the arrow on the pump’s volute casing (clock-
wise seen from the motor end). Verify by switching the motor
on and then off again immediately.
If the pump runs in the wrong direction of rotation, interchange
any two phases L1, L2 or L3 of the power cable in the motor
terminal box.
6 Commissioning, start-up / shutdown
6.1 Commissioning
Before starting up the pump make sure that
- the pump unit has been properly connected to the electric
power supply and is equipped with all protection devices;
- the pump has been primed with the liquid to be pumped;
- the direction of rotation has been checked;
- all auxiliary connections have been properly connected.
6.1.1 Shaft seal
Shaft seal (see sections 7.4.4 and 7.5.2)
6.1.2 Priming the pump and checks to be carried out
Before start-up, the pump and the suction line must be vented
and primed with the liquid to be pumped.
The shut-off valve in the suction line must be fully open.
Open the shut-off valve in the vacuum balance line (if any),
and close the vacuum-tight shut-off valve E (fig. 5.5-2).
Dry-running will result in increased wear and
must be avoided.
6.1.3 Final check
It must be easy to rotate the shaft by hand.
Check the integrity and proper functioning of all connections.
6.1.4 Contact guard
In compliance with the accident prevention regulations
the pump must not be operated without a contact guard.
6.1.5 Start-up
Always make sure that the shut-off valve in the discharge line
is closed before the pump is started up! Only after the pump
has reached full rotational speed shall the shut-off valve in the
discharge line be opened slowly and adjusted to comply with
the duty point.
After the operating temperature has been reached and/or in
the event of leakage, switch off the unit and re-
tighten hex. nuts 920.2 or .3 or .4.
6.1.6 Shutdown
Close the shut-off valve in the discharge line.
If the discharge line is equipped with a non-return or check
valve, the shut-off element may remain open if there is back
pressure.
The shut-off valve in the suction line must not be closed
when switching off the pump.
Switch off the motor, making sure that the unit runs down
smoothly to a standstill.
Depending on the type of installation, the pump should have a
sufficient after-run time – with the heat source shut off – until
the medium handled has cooled down sufficiently to avoid a
heat build-up in the pump.
For prolonged shutdown, close the shut-off valve in the suc-
tion line. Close the auxiliary connections.
In the event of frost and/or prolonged shutdowns, the pump
must be drained or otherwise protected against freezing.
0910:
3/
2
pp g
g
!
!
Etabloc
Caution
Caution
Caution
8
Содержание Etabloc
Страница 1: ...Operating Instructions Close coupled Pumps Etabloc...
Страница 2: ......
Страница 19: ......
Страница 20: ...Etabloc Gartone Press Tel 011 440 6126 29 6 2004 Subject to technical modification without prior notice...