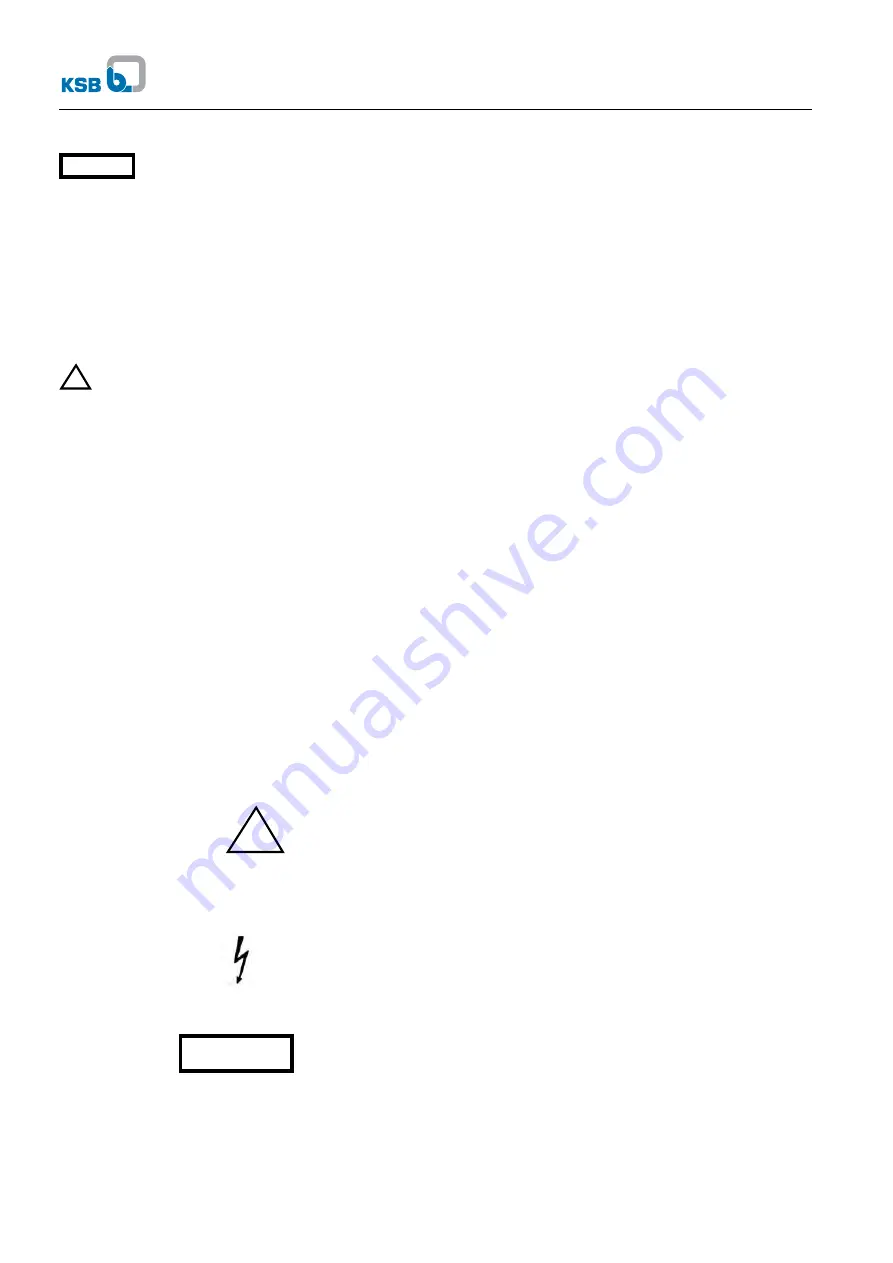
Etabloc
1 General
This KSB product has been developed in accor-
dance with state-of-the-art technology; it is man-
ufactured with utmost care and subject to continuous quality
control.
These operating instructions are intended to facilitate familiar-
ization with the unit and its designated use. The manual con-
tains important information for reliable, proper and efficient
operation. Compliance with the operating instructions is of
vital importance to ensure reliability and a long service life of
the unit and to avoid any risks.
These operating instructions do not take into account local
regulations; the operator must ensure that such regulations
are strictly observed by all, including the personnel called in
for installation.
This pump / unit must not be operated beyond the limit
values for the medium handled, capacity, speed, densi-
ty,
pressure, temperature and motor rating specified in the tech-
nical documentation. Make sure that operation is in accor-
dance with the instructions laid down in this manual or in the
contract documentation. Contact the manufacturer, if required.
The name plate indicates the type series / size, main operat-
ing data and identification number; please quote this informa-
tion in all queries, repeat orders and particularly when order-
ing spare parts.If you need any additional information or
instructions exceeding the scope of this manual or in case of
damage please contact KSB’s nearest customer service cen-
tre. Noise characteristics see section 4.5.
2 Safety
These operating instructions contain fundamental information
which must be complied with during installation, operation and
maintenance. Therefore this operating manual must be read
and understood both by the installing personnel and the
responsible trained personnel / operators prior to installation
and commissioning, and it must always be kept close to the
location of operation of the machine / unit for easy access. Not
only must the general safety instructions laid down in this
chapter on ”Safety” be complied with, but also the safety
instructions outlined under specific headings.
2.1 Marking of instructions in the manual
The safety instructions contained in this manual whose
non-observance might cause hazards to persons are special-
ly marked with the symbol
general hazard sign to ISO 7000-0434
The electrical danger warning sign is
safety sign to IEC 417 - 5036,
The word
is used to introduce safety instructions whose non-obser-
vance may lead to damage to the machine and its functions.
Instructions attached directly to the machine, e.g.
- arrow indicating the direction of rotation
- markings for fluid connections
must always be complied with and be kept in a perfectly legi-
ble condition at all times.
2.2 Personnel qualification and training
All personnel involved in the operation, maintenance, inspec-
tion and installation of the unit must be fully qualified to carry
out the work involved.
Personnel responsibilities, competence and supervision must
be clearly defined by the operator. If the personnel in question
is not already in possession of the requisite know-how, appro-
priate training and instruction must be provided. If required,
the operator may commission the manufacturer / supplier to
take care of such training. In addition, the operator is respon-
sible for ensuring that the contents of the operating instruc-
tions are fully understood by the responsible personnel.
2.3 Non-compliance with safety instructions
Non-compliance with safety instructions can jeopardize the
safety of personnel, the environment and the machine / unit
itself. Non-compliance with these safety instructions will also
lead to forfeiture of any and all rights to claims for damages.
In particular, non-compliance can, for example, result in:
- failure of important unit/system functions,
- failure of prescribed maintenance and servicing practices,
- hazard to persons by electrical, mechanical and chemical
effects,
- hazard to the environment due to leakage of hazardous
substances.
2.4 Safety awareness
It is imperative to comply with the safety instructions contained
in this manual, the relevant national health and safety regula-
tions and the operator’s own internal work, operation and
safety regulations.
2.5 Safety instructions for the operator / user
- Any hot or cold components that could pose a hazard
must be equipped with a guard by the operator.
- Guards which are fitted to prevent accidental contact with
moving parts (e.g. coupling)must not be removed whilst
the unit is operating.
- Leakages (e.g. at the shaft seal) of hazardous media han-
dled (e.g. explosive, toxic, hot)must be contained so as to
avoid any danger to persons or the environment. All rele-
vant laws must be heeded.
- Electrical hazards must be eliminated. (In this respect
refer to the relevant safety regulations applicable to differ-
ent countries and/or the local energy supply companies.)
2.6 Safety instructions for maintenance, inspection and
installation work
The operator is responsible for ensuring that all maintenance,
inspection and installation work be performed by authorized,
qualified specialist personnel who are thoroughly familiar with
the manual.
The pump must have cooled down to ambient temperature,
pump pressure must have been released and the pump must
have been drained.
Work on the machine / unit must be carried out only during
standstill. The shutdown procedure described in the manual
for
taking the unit out of service must be adhered to without fail.
Pumps or pump units handling media injurious to health must
be decontaminated.
Caution
!
!
Caution
4
Содержание Etabloc
Страница 1: ...Operating Instructions Close coupled Pumps Etabloc...
Страница 2: ......
Страница 19: ......
Страница 20: ...Etabloc Gartone Press Tel 011 440 6126 29 6 2004 Subject to technical modification without prior notice...