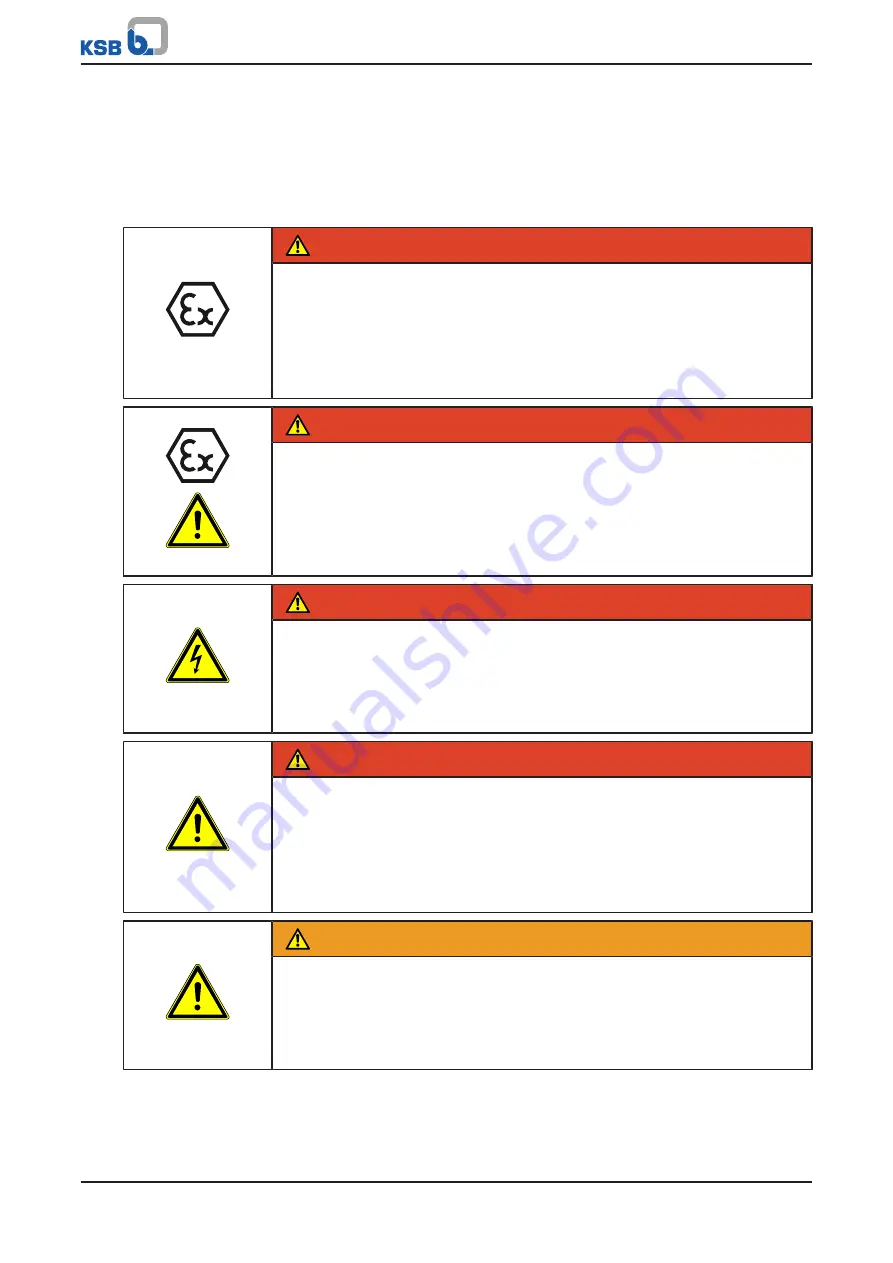
7 Servicing/Maintenance
42 of 84
Amarex N
2563.84/08-EN
7 Servicing/Maintenance
7.1 Safety regulations
The operator ensures that maintenance, inspection and installation are performed by
authorised, qualified specialist personnel who are thoroughly familiar with the
manual.
DANGER
Sparks produced during servicing work
Explosion hazard!
▷
Observe the safety regulations in force at the place of installation!
▷
Never open an energised pump set.
▷
Always perform maintenance work on explosion-proof pump sets outside
potentially explosive atmospheres only.
DANGER
Improperly serviced pump set
Explosion hazard!
Damage to the pump set!
▷
Service the pump set regularly.
▷
Prepare a maintenance schedule with special emphasis on lubricants, power
cable, bearing assembly and shaft seal.
DANGER
Electrical connection work by unqualified personnel
Danger of death from electric shock!
▷
Always have any work on the connection to the power supply performed by a
trained electrician.
▷
Observe regulation EN 60079.
DANGER
Risk of falling when working at a great height
Danger to life by falling from a great height!
▷
Do not step onto the pump (set) during installation work or dismantling work.
▷
Pay attention to safety equipment, such as railings, covers, barriers, etc.
▷
Observe the applicable local health and occupational safety regulations and
accident prevention regulations.
WARNING
Unintentional starting of the pump set
Risk of injury by moving components and shock currents!
▷
Ensure that the pump set cannot be started unintentionally.
▷
Always make sure the electrical connections are disconnected before carrying
out work on the pump set.
Содержание Amarex N series
Страница 80: ...Index 80 of 84 Amarex N 2563 84 08 EN W Warnings 7 Warranty claims 6...
Страница 81: ......
Страница 82: ......
Страница 83: ......