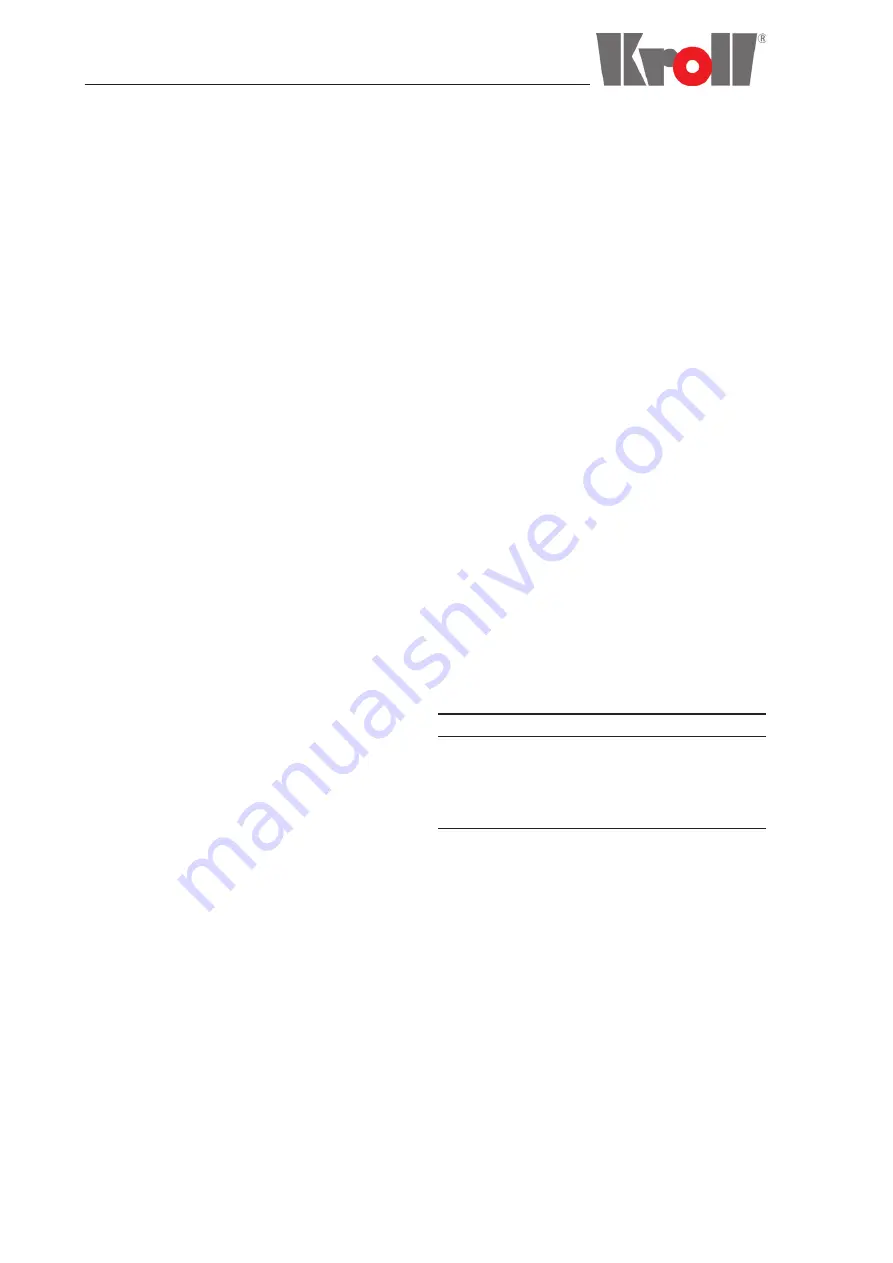
9
Installation and commissioning
•
Take off the intake hose from the burner
connection and put it into the foreseen con-
nection at the lower side of the burner hood.
•
Turn the switch at the control panel to "Pre-
heat" and activate the main switch.
•
Mount all side panels of the BKM120.
The 3 kW electric heater now heats the complete
fresh air intake pipe and the heat exchanger,
the burner and the burner motor and the interior
room with the boiler control.
After about 30 – 45 min (depending on the out-
door temperature), continue as follows:
•
Take off the intake hose from the burner
hood and put it onto the burner connection.
•
Promptly, adjust the switch to "Boiler".
Then activate the boiler main switch. The switch
will glow green. Depending on the operation
mode, do the necessary adjustments as shown
in the chapter "Control settings".
4.3.3 Secondary side
Until the operation temperature is reached, the
boiler circulates the liquid internally. Only after
that, the primary circuit is supplied and the
energy can be taken off by the secondary circuit
at the plate heat exchanger. The highest possible
temperature raise depends from the flow rate.
The following table indicates the calculated tem-
perature rise at different flow rates at the maxi
-
mum power of 120 kW. It only depends slightly
from the entering temperature.
Flow rate [l/min]
Temperature rise [K]
50
35
100
17
150
12
200
8,6
At low entering temperatures (return temperatu-
res) of about <20 °C, the flow rate must not be
higher than 75 l/min (4,5 m³/h, calculated flow
rate). In addition to that, the boiler temperature
must be set to 85 °C (see "Control settings").
Otherwise, undesired operation faults of the con-
trol may occur (pulsing control, long controlling
time).
• the secondary circuit is filled and deaerated.
•
the cap valve B5 at the expansion vessel is
opened.
•
the condensate pipe and the neutralisation
box are filled with water and free of ice.
•
the valves B1, B2 and B3 are opened.
•
all connections and screwings are sealed.
•
the inlet air hose is put onto the burner.
At temperatures near or below the freezing point,
you have to check if the siphon of the conden-
sate pipe and the neutralization box are ice-free.
If they are not, you have to thaw the ice before
commissioning using the heating band. Switch it
on using the switch "Heat Neutrabox" at the con-
trol panel. When all the ice has melted, you can
continue the commissioning work.
4.3.1 Commissioning at outdoor tempe-
ratures >5 °C
At outdoor temperatures over 5 °C, pre-heating
the burner and the inlet air components is not
necessary. The changeover switch at the control
panel must be adjusted do "Boiler". Then acti-
vate the boiler main switch. The switch will glow
green. Depending on the operation mode, do the
necessary adjustments as shown in the chapter
"Control settings".
4.3.2 Commissioning at outdoor tempe-
ratures <5 °C
In case of too low outdoor temperatures, the fol-
lowing problems may occur:
1. Condensate leftovers from last operation
can be frozen and thus hinder the newly
created condensate to flow away.
2. If a not suitable fuel is used or if a not sui-
table fuel is still inside the oil pipe, paraffin
may have been created blocking now the oil
pipe.
3. If the intake air is too cold, it may happen
that there is no flame at the burner.
4. The bearing grease inside the burner motor
can be too viscous so that the motor does
not start.
For point 1, set the switch „Heat Neutrabox“ to
„1“. For point 2 observe the table on chapter
"Mounting and connecting". For points 3 and
4, you have to do the pre-heating programme
before the actual commissioning. This is how to
do it:
Содержание BKM120
Страница 1: ...Operation Manual BKM120 Mobile hot water unit 053373 00c July 2014 0085 ...
Страница 2: ......
Страница 7: ...5 General 1 5 Circuit diagram ...
Страница 17: ...15 Notes 9 Notes Notes and particularities ...
Страница 18: ...BKM120 16 Notes Notes and particularities ...
Страница 19: ...17 Notes Notes and particularities ...