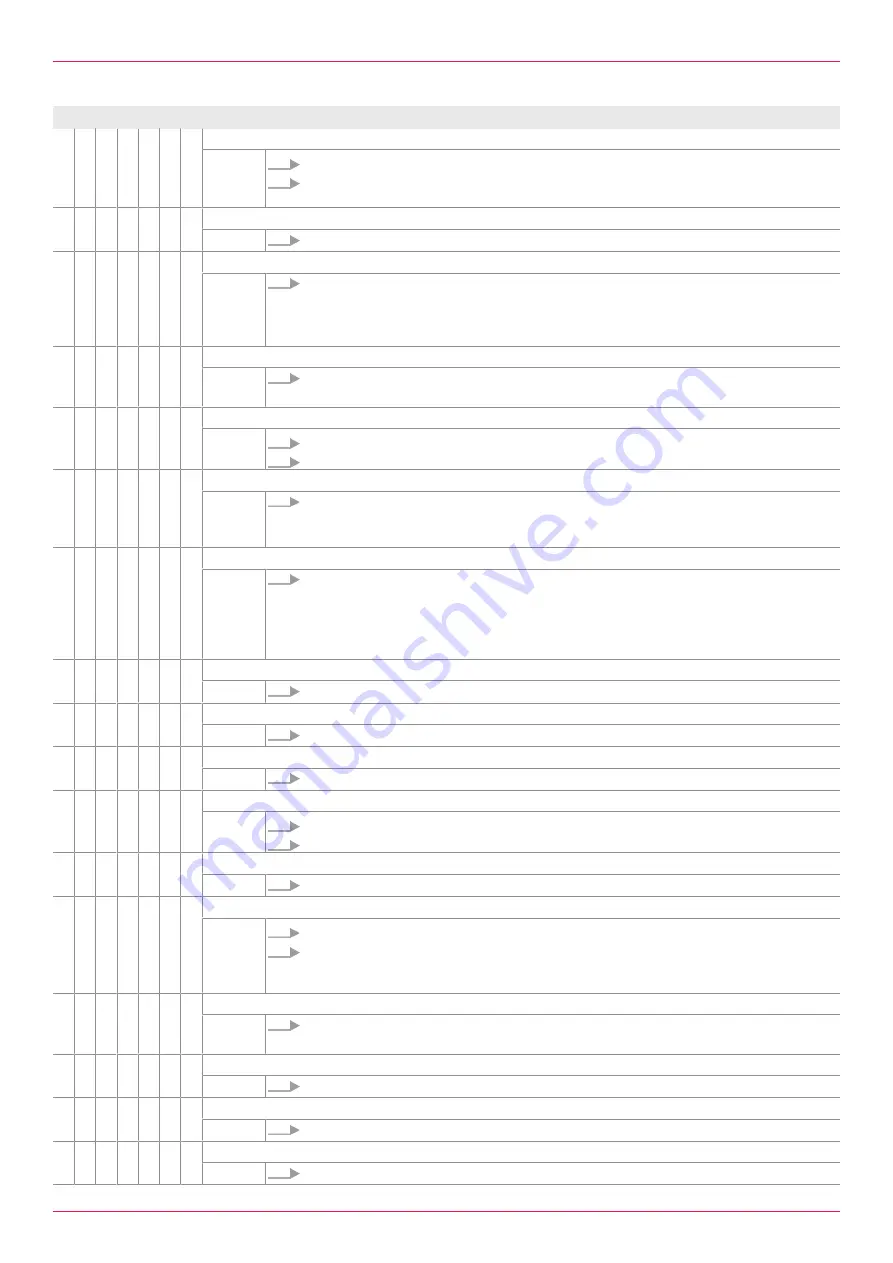
14 Troubleshooting
14.2 Troubleshooting
Fault identification
Cause
Remedy
–
2
–
4
–
–
–
Speed/frequency/voltage of the motor false
1.
Ensure that the motor frequency and voltage match the operating voltage.
2.
Ensure that the speed of the motor matches the rating plate of the pump. If necessary ad-
just the speed.
–
2
–
–
–
–
–
Advanced wear of the housing/screw set
Contact the manufacturer.
–
–
–
–
–
–
7
Advanced wear of sealing surfaces
Replace the seal and check the pumped liquid for abrasive substances. If required, re-
place the filter/strainer.
-or-
Contact the manufacturer.
–
–
3
–
–
–
–
Coupling aligned incorrectly
Assemble the coupling and motor correctly, see the associated operating instructions of
the pumps.
–
–
3
–
–
–
–
Pump subject to mechanical stress
1.
Support the weight of the pipe system.
2.
Connect the pump station correctly to the pipe system
Ä
–
–
3
–
–
–
–
Vibrations/pulsations in the system
Bear the pump station elastically.
-or-
Make the connections with hoses.
–
–
3
–
–
–
–
Flow speed in the pressure line or suction line too high
Set the flow speed in the pressure line so that it does not exceed 3 m/s.
-or-
Set the flow speed in the suction line so that it does not exceed 1 m/s.
-or-
Contact the manufacturer.
–
–
3
4
–
–
7
Ball bearing damaged
Replace the ball bearing, see corresponding operating instructions of the pump.
–
2
3
4
–
–
7
Superficial damage to pump parts coming into contact with the liquid
Contact the manufacturer.
–
–
–
–
–
–
7
Shaft seal damaged through dry running
Replace the shaft seal, see corresponding operating instructions of the pump.
–
–
–
–
–
–
7
Inlet pressure too high
1.
Reduce the inlet pressure at the system side.
2.
Replace the shaft seal, see corresponding operating instructions of the pump.
–
–
–
–
–
–
7
Inlet pressure too low
Install a non-return valve at the pressure side.
–
–
–
–
–
–
7
Shaft seal is overloaded through thermal/chemical influences
1.
Check the maximum operating temperature.
2.
Check the suitability and resistance of the elastomers with regard to the pumped liquid.
-or-
Contact the manufacturer.
–
–
–
–
–
–
7
Overload of the shaft seal by pressure build-up during the heating process
Open the pressure-side/suction-side shut-off device in order to avoid a pressure build-up
through heat expansion of the pumped liquid.
1
2
3
4
5
–
–
Cold start when delivering high-viscosity liquids
Install the heating system.
–
–
–
–
–
–
7
Differential pressure is too high and has overloaded the idle screws
Contact the manufacturer.
–
–
–
–
–
–
7
Viscosity is too low and has overloaded the idle screws
Contact the manufacturer.
46
OID 02en-GB Edition 2019-11
Operating instructions