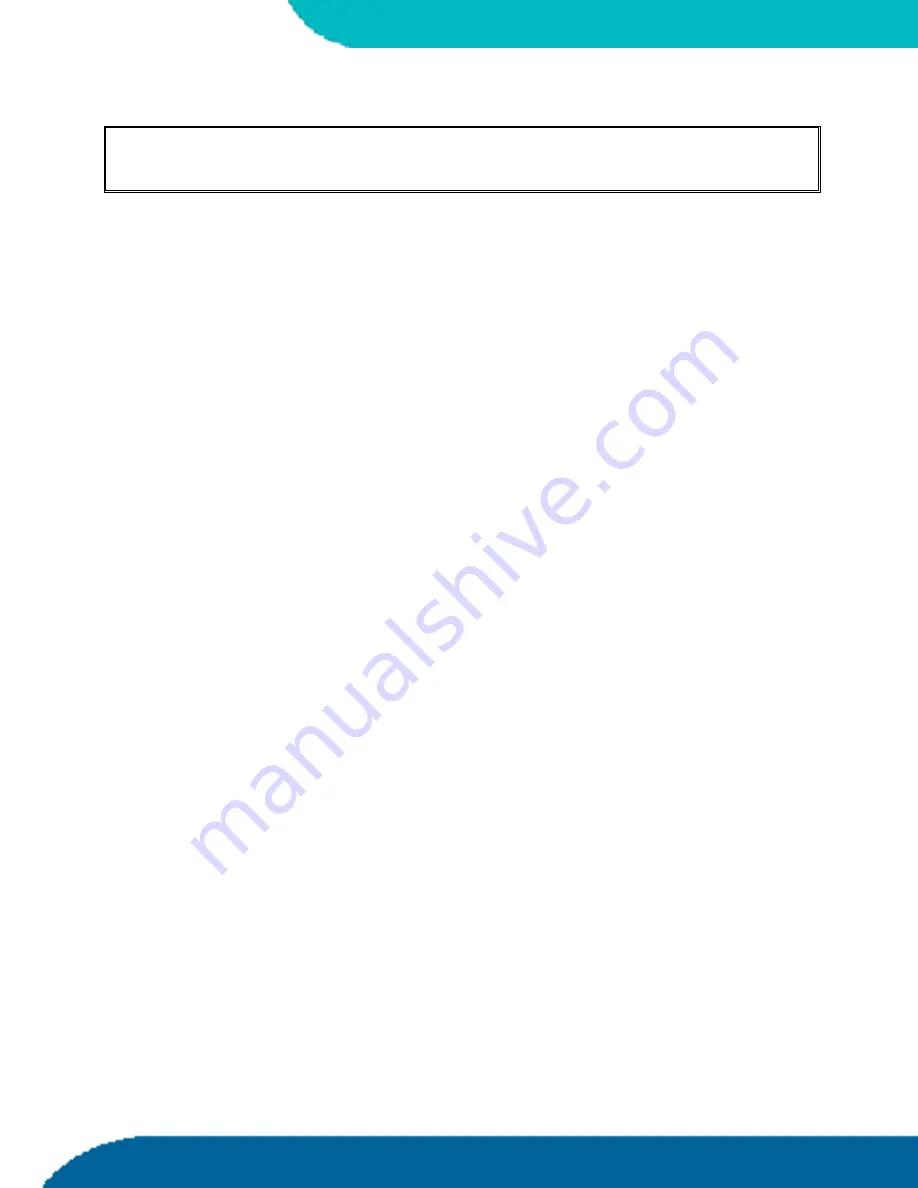
Kontron
ETX-P3/C3 User’s Guide
23
Design Considerations
11.
DESIGN CONSIDERATIONS
11.1
Thermal Management
A heat-spreader assembly is available from Kontron Embedded Modules for the
ETX-P3/C3
.
The heat-spreader plate on top of this assembly is NOT a heat sink. It is intended as an ETX-
standard thermal interface to be used with a heat sink or other cooling device.
External cooling must be provided to maintain the heat spreader plate at proper operating
temperatures. Under worst-case conditions, the cooling mechanism must maintain an
ambient air and heat-spreader plate temperature of 60
°
C or less.
The aluminum slugs and thermal pads on the underside of the heat-spreader assembly
implement thermal interfaces between the heat spreader plate and the major heat-
generating components on the
ETX-P3/C3
. About 80% of the power dissipated within the
module is conducted to the heat spreader plate and can be removed from it by the cooling
solution.
For the 400 and 500MHz modules, the heat dissipated into the spreader plate is in the 10 to
12 watt range. It is recommended that the cooling solution be designed for a heat spreader
plate heat load of 20 watts to accommodate future
ETX-P3/C3
modules with faster
processors.
For 700MHz modules, the heat dissipated into the plate ranges from 16 to 18 watts. Design
a cooling solution to dissipate the heat load on a heat-spreader plate at a minimum of 20
watts to accommodate all
ETX-P3/C3
modules.
Many thermal-management solutions can be used with the heat-spreader plate, including
active and passive approaches. The optimum cooling solution varies depending on the ETX
application and environmental conditions. Please see the
ETX Design Guide
for further
thermal-management information.