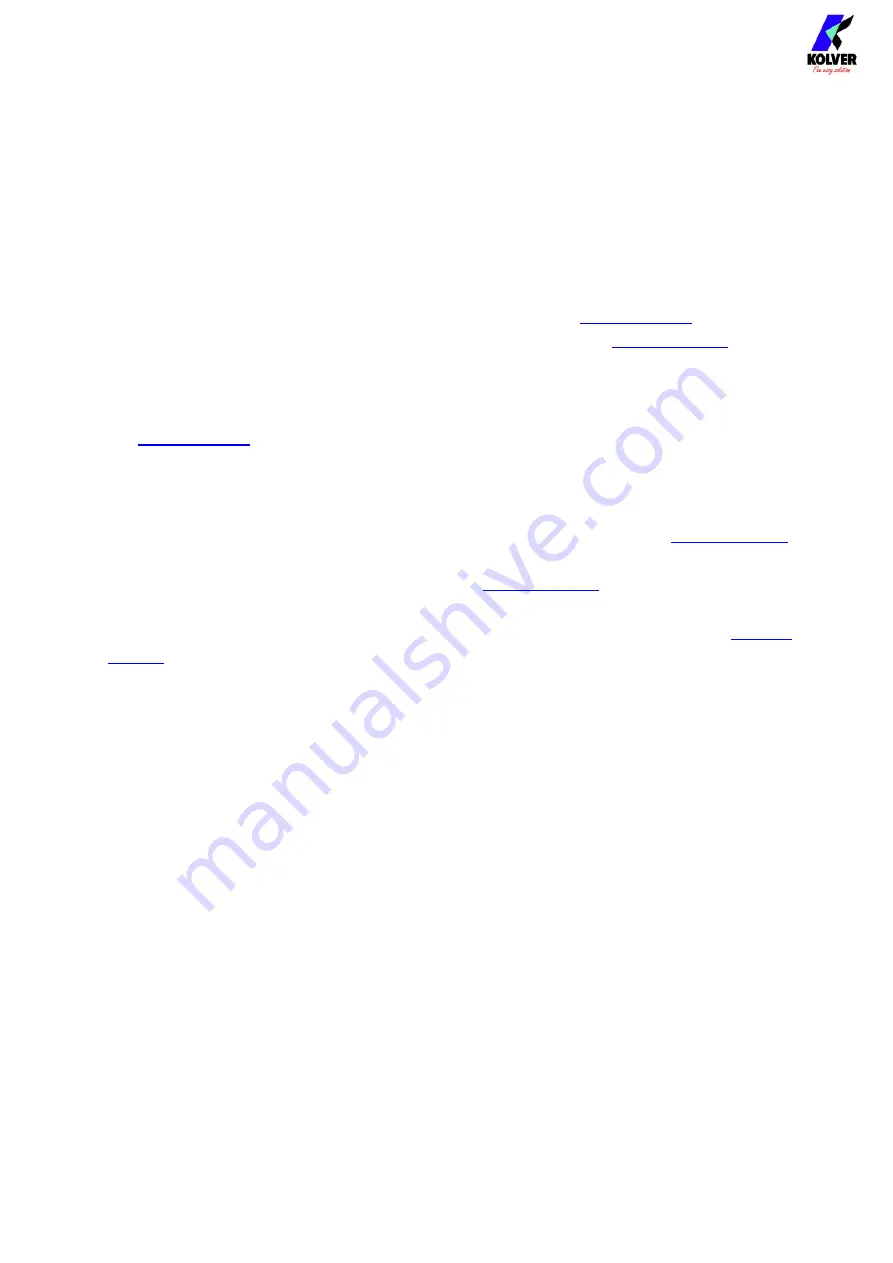
Vers. 062721
36
WARNING:
carefully choosing the right combination of speed and downshift settings
for the application will maximize the precision and lifetime of the tool while minimizing
your assembly cycle time.
While the appropriate settings can be highly specific to each application, there exist a
few rules of thumb:
A high approach speed minimizes motor strain and assembly cycle time, but can
mechanically stress and even break the part or the tool if the joint is hard.
Hard/inelastic joints are best finished at low speed, to improve precision and avoid a
high velocity impact at the end of the rundown. Utilize the
very low torque AT threshold (<20% of target torque) and slow
, to ensure
that the last revolutions are executed slowly and in control.
Soft/elastic joints, especially those requiring high target torques relative to the range
of the tool, are best executed at high speed, to avoid excess strain on the motor. Utilize
the
setting with a high torque AT threshold (>80% of target torque), to
ensure most of the torque is applied at higher speed.
(7)
DOWNSHIFT
The DOWNSHIFT function lets you execute the rundown in two phases: a high speed
approach (enter the speed in the “RPM” field), followed by a lower (6)
after a certain torque threshold is reached.
If OFF (red), the screwdriver will run at the (6)
If ON (green), the screwdriver will run at the entered “RPM” speed until a certain
torque is reached (AT torque value), at which point it will downshift to the (6)
for the remainder of the rundown.
Note: most applications will benefit from using the DOWNSHIFT setting, as it allows to
minimize production cycle times (running the screwdriver fast) without compromising
on final torque precision (finishing the rundown at a slow, controlled speed).
(8)
ANGLE CONTROL / TORQUE MONITORING flag
Tap to select Angle Control and Torque Monitoring mode.
In this mode, the screw is tightened down to the target angle (number of revolutions of
the screw, in degrees), while the torque is measured.
(9)
TARGET Angle
Tap to set the target angle. Only available in Angle Control/Torque Monitoring mode.
(10)
MIN Angle
If the angle measured at the end of the rundown is below the MIN Angle value, the
rundown will be considered unsuccessful (NOK) and a corresponding error will be
raised. Applicable to Torque Control as well as Angle Control modes.
(11)
MAX Angle
If the angle measured at the end of the rundown exceeds the MAX Angle value, the
rundown will be considered unsuccessful (NOK) and a corresponding error will be
raised. Applicable to Torque Control as well as Angle Control modes.
(12)
STARTING AT
Tap to select the starting point for the angle measurement. Three modes are available:
-
Torque threshold: the angle measurement starts after the torque reaches this value
Содержание K-DUCER
Страница 1: ...KDU1 KDU1A Torque range 0 1 70 Nm OPERATOR MANUAL...
Страница 22: ...Vers 062721 22 Main Screen Program Mode navigation tree...
Страница 25: ...Vers 062721 25 Main Screen Sequence Mode navigation tree...
Страница 32: ...Vers 062721 32 PROGRAMS menu tree...
Страница 33: ...Vers 062721 33...
Страница 34: ...Vers 062721 34...
Страница 44: ...Vers 062721 44 SEQUENCE SETTINGS menu tree...
Страница 53: ...Vers 062721 53 USB menu tree...
Страница 59: ...Vers 062721 59...