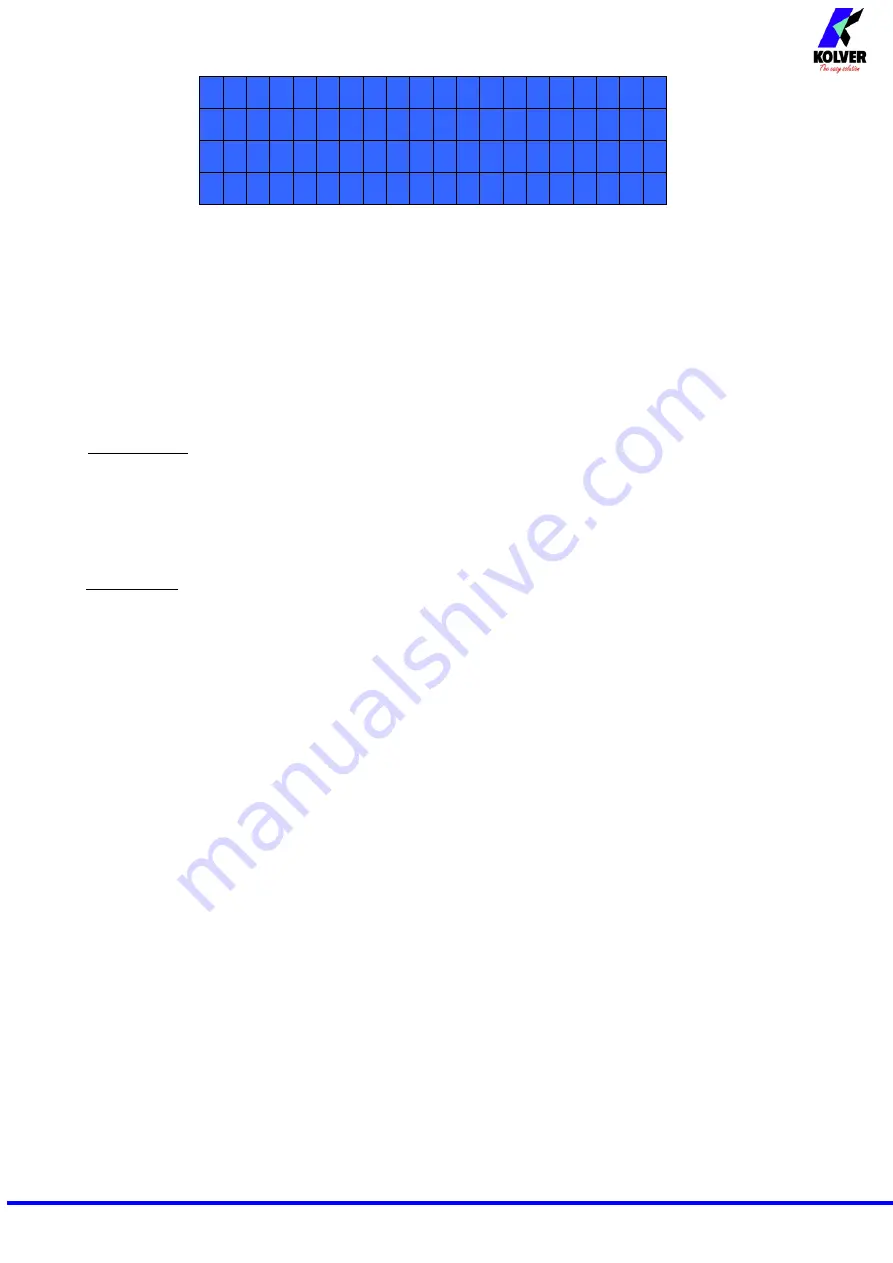
Vers. 100822 Page 5
- - - - - M E N U - - P R : 1 - - - - -
3 ) M o d e l : P L U T O 1 0
4 ) R a m p : 0 . 3 s
5 ) T o r q u e : 1 0 % 1
3) Model:
you can select the screwdriver to be used. Your choice will automatically change the default
settings.
It’s important to select the correct model you’re going to use since most parameters regarding the
motor software are specific to every single model.
In the # mode, the models that can be selected are: MITO 15, PLUTO3, PLUTO6, PLUTO10, PLUTO15,
PLUTO20, PLUTO35, PLUTO50, PLUTO 3ANG, PLUTO 6ANG and PLUTO 8ANG. In this mode, once
chosen a screwdriver model, a speed and tightening torque will be automatically set in an intermediate value
between those available. While in reverse, torque and speed values will be set at maximum.
Also in the # mode, if the
Model Detect
is set on auto and no screwdriver is connected, it won’t be possible
to set any torque value or speed.
IMPORTANT: To work with CA drivers, switch box, socket tray and remote it is mandatory to select
ON on Ext. Box in Sequence Menu.
4) Ramp
:
You can select the slow start time (acceleration) from 0.2 to 3.0 sec. This option is only available
for the screwing phase, while during the unscrewing phase the ramp time is always 0.2 sec. We suggest using
this option with self-tapping screws.
ATTENTION: Reaching the torque while the ramp is still on could give as result a different torque level from
the one that results when the ramp is over. This is due to the motor acceleration.
Reaching the torque while the ramp is still on will activate the “screw OK” signal anyway (this option is useful
if you need to tighten screws that are already tightened, the so called “double hit” ).
On the other hand, if you wish to see an error signal during the preset torque in the ramp phase, you can
change the minimum time by setting value which is equal or superior to the ramp value (see point 7).
5) Torque:
you can select the desired torque as a percentage of the torque range of the selected screwdriver.
For example, for a Pluto10, a 50% setting will result in a torque in the area of 4 -5 Nm. The torque range is
always referred to the MAX speed. In case you’re not working at maximum speed, the torque range will
progressively lower in order to avoid motor stalling. If the torque level is reached correctly, it will be displayed
and you will hear a beep sound, too.
Such torque level is indicated as “T: ..% ” on the main screen.
In
#
mode, the desired torque value is set automatically. This value depends on some tables which show a
range of selectable torque values for each speed (see page 18). Therefore, for each speed it is possible to set a
torque value between the minimum and maximum indicated. The torque range available will be displayed
also on the main screen. If you want to set a torque value outside the range of that speed, you will have to
increase or decrease the speed value in order to get a range of values the desired one is contained in.
6) Compens – Compensation:
This function allows an increase or decrease of the displayed torque value
after a calibration. The available range is from 0 to ±55 Nm. For example: after calibration (see Torque
calibration) you make a screwing on your assembly and compare the displayed value to the value you see on
a torque tester (for example a mini-K or a K model). Let's say you notice that the torque displayed in the unit
EDU 2AE/TOP is +0.2 Nm higher than the value indicated on the tester (which is the right one). In this case
you can modify this value by setting -0.2 Nm so that the value on the display will be the same as the value on
the tester. If it’s lower than 0.3 Nm, you need to set +0.3 Nm and so on.
In # mode, this function is used to increase the torque accuracy in tightening. If a tightening value is checked
through a torque meter (for example a K or miniK model) and you notice a deviation between this and the
target value or the one on the unit display, you can intervene by adding an offset (positive or negative) through
compensation.