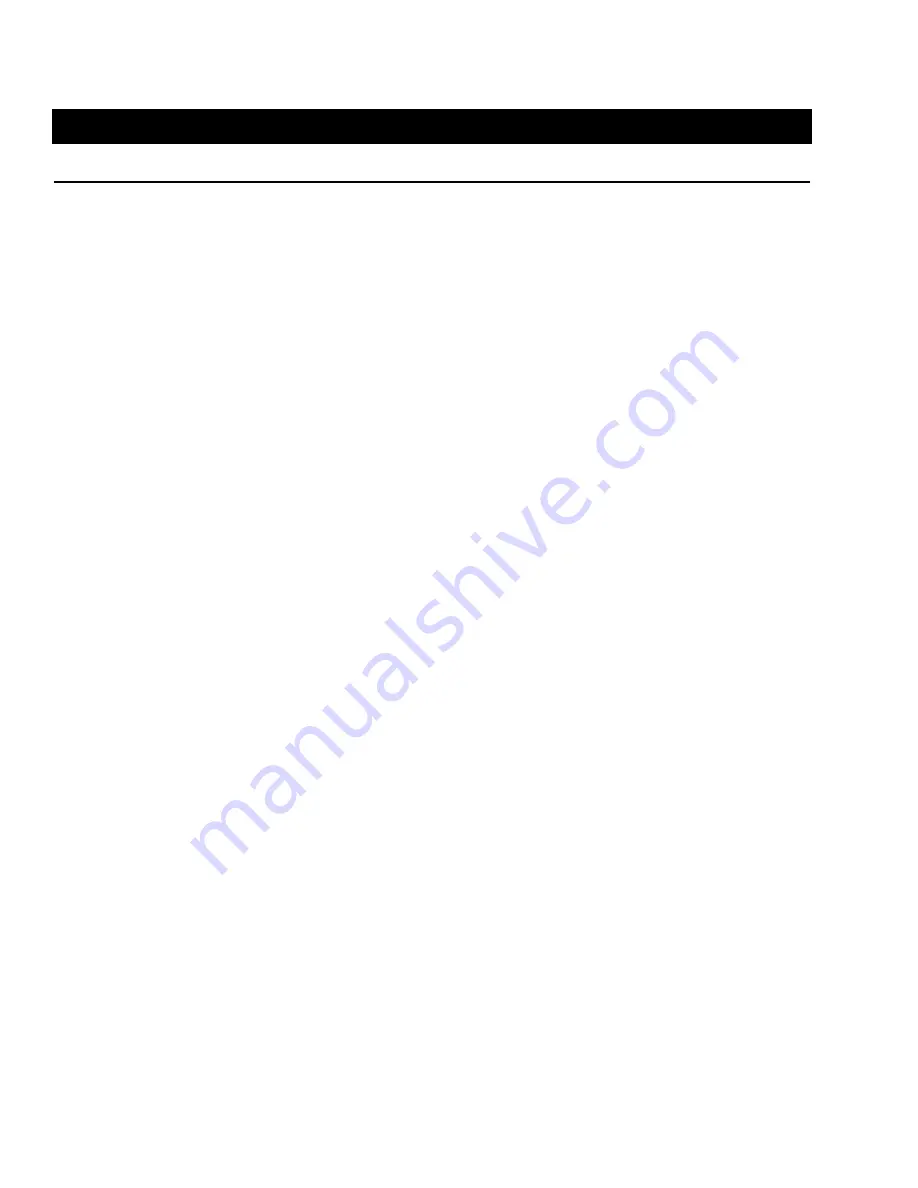
2
Table of Contents
Section
Page Number
1.0
Important Information and Warnings…………………………………………….……………………. 4
1.1
Terms and Summary
1.2
Warning Tags and Labels
2.0
Technical Information …………………………….…………………………………………………… 10
2.1
Specifications
2.2
Dimensions
2.3
Part Names
3.0
Pre-operational Procedures……………………………………………………………………….….. 16
3.1
General Information
3.2
Handling
3.3
Mounting Location
3.4
Assembly, Adjustments and Mounting
3.5
Block Operated Limit Switch (BLS) Adjustment
3.6
Electrical Connections
3.7
Pendant Installation
3.8
Hoist Variable Frequency Drive (VFD) Setup
3.9
Light-Load High Speed Function
3.10
Hoist Load Limiter (LL) Adjustment
3.11
Trolley Variable Frequency Drive (VFD) Setup
3.12
Hoist Upper and Lower Limit Switch (ULLS) Setup
3.13
Pre-operational Checks and Trial Operation
4.0
Operation……………………………………………………………………………………………….. 44
4.1
Introduction
4.2
Shall’s and Shall Not’s for Operation
4.3
Hoist and Trolley Controls
Содержание Harrington RY Series
Страница 15: ...15 2 3 Part Names Figure 2 1 RY Part Names...
Страница 42: ...42 Figure 3 20 Hoist Upper and Lower Limit Switch ULLS...
Страница 57: ...57 Table 5 8 Various shapes that require the wire rope to be replaced...
Страница 67: ...67 Table 6 9 Motor Brake Gap Capacity Code Brake Gap G inch mm RY030 RY050 0 032 0 8...
Страница 104: ...104 9 3 Trolley Frame Parts Figure 9 3 Trolley Frame Parts...
Страница 112: ...112 9 10 Hoist Motor Parts Figure 9 10 Hoist Motor Parts...
Страница 114: ...114 9 11 Trolley Motor Parts Figure 9 11 Trolley Motor Parts...
Страница 116: ...116 9 12 Control Panel Box Parts Figure 9 12 Control Panel Box Parts...
Страница 119: ...119 This Page Intentionally Left Blank...