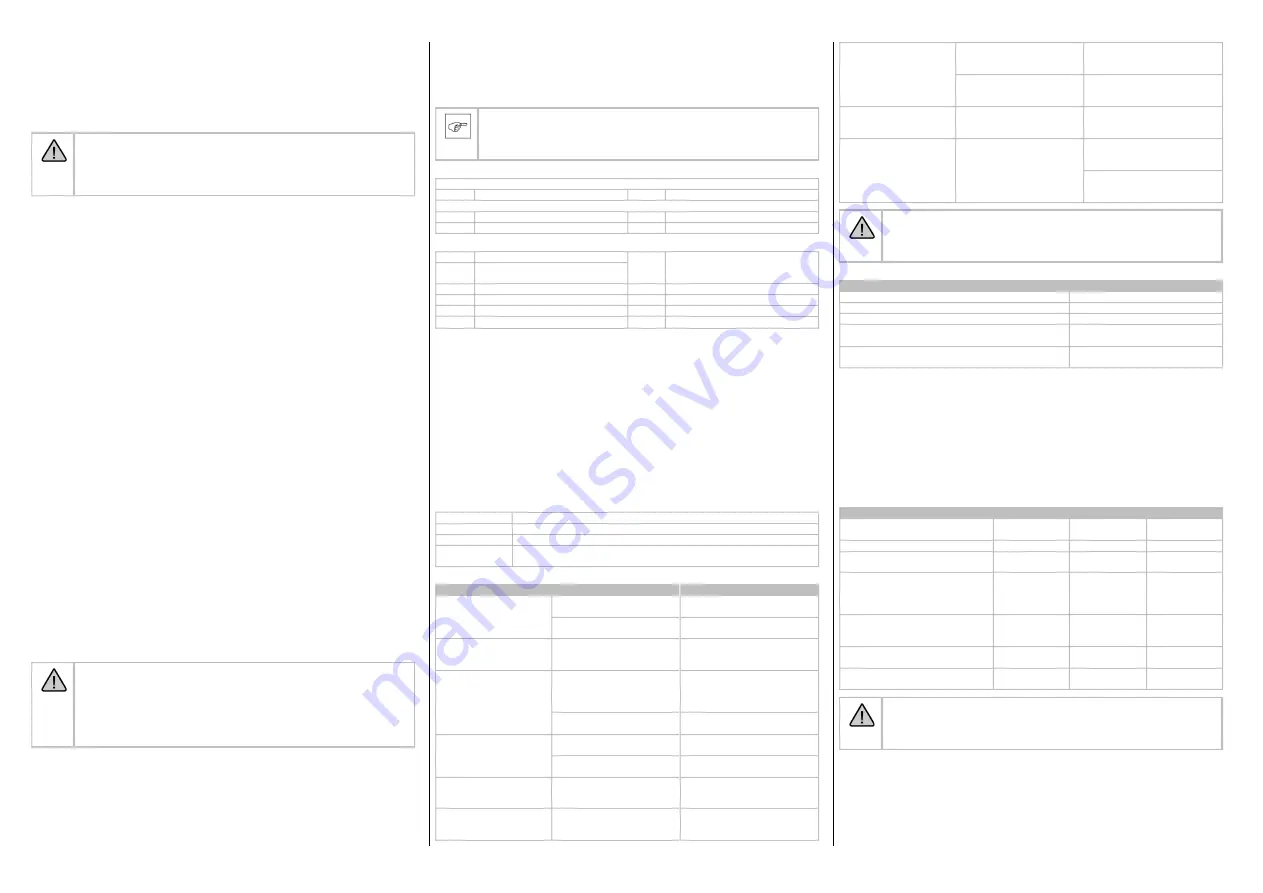
13
22.05.2018
71. If the height monitor (64) is retracted (min.
①
), the container can be collected and set
down.
The fixed hooks (67) can be opened and closed.
72. If the height monitor is extended (max.
②
), the container can be emptied and the
container floor can be opened and closed.
The mobile hooks (68) can be moved upwards and downwards.
73.
Coloured markings
show that the height monitor (64) is extended.
74. WARNING
The
pressure switch
function on the crane is an important safety device in
addition to the height monitor (64). It prevents the container falling down, even if
there is an operating error.
Ensure it is installed correctly.
Pressure switch installation:
The valve block (H9) delivered with the discharge unit must be installed in the hydraulic circuit
of the function “open/close” (open/close container floor = extend/retract cylinder). A 24 V
electrical connection is required to activate the solenoid coil. Ensure that the “I
N” connection (P)
in the “open“ line and the “OUT” connection (T) in the “close” line are each installed with a T
connection.
Pressure switch operation:
The system works with 2 pressure levels. In normal mode, (pressure switch (74) is not
activated), the pressure relief valve (H9.1) prevents the working pressure of 70 bar from being
exceeded. The fixed hook cannot open. When the container is hanging freely, the container
floor can only be opened with the “open” function. The pressure limit is only stopped when the
pressure button (74) is activated, and the full crane pressure (min. 200 bar) is available. If a
container is set down and the height monitor is retracted, the fixed hooks (67) now open with
the “open” function to detach the container. The pressure button (74) is mounted on the
hydraulic lever or the remote control if not already present.
75.
Safety sticker: Do not shore up the container while open.
When emptying, do not allow
the container or container floor to rest on anything
①
, as this may cause the height
monitor to retract
②
.
If the height monitor retracts, the fixed hook will open and the load will
fall down
③
.
76. Operation
77. Also see the Quick Guide delivered with the unit.
78. Before beginning operation: Check whether fixed and mobile hooks are fully opened.
If the hooks are not open:
•
Place the unit on a solid surface.
•
Lower the crane boom until the height monitor (64) is fully retracted.
•
Use the "open grab" function and press the pressure switch (74) push-button. Fixed and
mobile hooks will be opened.
•
Check: The lock indicator (67) must be retracted and not visible; then the mobile hook
(66) is open.
79. Latch onto the container
•
Position the unit vertically over the fixed (80) and mobile disks (81) and lower it
until the
height monitor is fully retracted
.
•
Close the fixed hooks (66):
Actuate the
"close grab"
function until the closing
movement stops automatically.
Visual inspection:
The
lock indicator (67) must be
visible
.
•
Close the container floor:
Use the crane to
lift
the unit until the
height monitor is fully
extended
. The yellow marking (73) on the height monitor (64) must be visible. Actuate
the
"close grab" function:
The mobile hooks close and the mobile disk (80) is raised.
The closing movement stops automatically. The container is raised slightly.
WARNING
Do not lift the container:
•
If the container is only hooked onto the mobile disk (80) and the fixed disk
(81) is visible.
•
If the fixed hook is jammed and not hooked onto the fixed disk (81) correctly.
•
If the lock indicator (67) is not visible.
"Open hook": see 78.
82. Empty the container
•
Position the container above the larger container into which it is to be discharged.
•
Use the "open grab" function to lower the mobile disk (80), which opens the container
floor and discharges the container.
•
Use the "close grab" function to close the container floor.
83. Release container
•
Set the container on the ground so that the height monitor (64) stays extended.
•
"Open grab" function: The mobile disk (80) is lowered. The opening movement stops
automatically.
•
Then lower the crane boom until the height monitor is fully retracted.
•
Use the "open grab" function and press the pressure switch (74) push-button. Fixed and
mobile hooks will be opened. The lock indicator (67) retracts.
•
Lift the unit.
84. Technical data
85. Requirements of the carrier machine
NOTICE
Operating pressure dependent on litre performance
max. 20 MPa (200 bar) at max. 75 l/min
20 - 37 MPa (200 - 370 bar) at max. 40 l/min
86. Greasing points
Grease fitting – grease gun
A
Rotator
B
Cylinder bearing
Grease spray:
C
Plain bearing
E
Mobile hooks
D
Fixed hooks
F
Locking indicator
87. KM920-12 hydraulic diagram
H1
Lower
H7
Pressure relief valve
50 bar: Standard
0 bar: Special
H2
Lift
H3
Ball valve for limit of lift
H8
Pressure relief valve 130 bar
H4
Pressure relief valve 200 bar
H9
Valve block
H5
Ball valve for height monitor
H9.1
Pressure relief valve 70 bar
H6
Non
-return valve
Adjust pressure relief valve H7
If the fixed hooks close autonomously as a result of increased back pressure, the set pressure
for the pressure relief valve can be increased in stages until the hooks no longer close
autonomously.
Adjusting the pressure relief valve:
•
Set down container discharge unit.
•
Open the fixed hooks (extend the cylinder).
•
Move the open/close function to the neutral position.
Observe the fixed hooks: If the fixed hooks remain open, the pressure relief valve is set
correctly. If the fixed hooks close automatically, continue with this procedure.
•
Loosen the counter nut with a spanner (size 15).
•
To increase the pressure setting, unscrew the Allen screw (IS, size 4) by a quarter turn
(clockwise).
•
Tighten the Allen screw and counter nut securely.
•
Close the fixed hooks (retract the cylinder).
Repeat procedure until the fixed hooks remain open.
G
Pressure relief valve
GS
Size 15 open-ended spanner for hexagon castle nut
IS
Size 4 Allen screw
Measure L
For 50 bar = 8 mm
For 0 bar = unscrewed as far as the limit stop
88. KM920-12 troubleshooting
Functional fault
Cause
Remedial measures
Lifting hooks (65) and
fixed hooks (66) do not
close
Height monitor (64) not
retracted
Retract height monitor, see 70.,
76.
Ball valve for height monitor
(H5) defective
Replace valve
Mobile hooks (65) do not
close or do not close
completely
Leg spring broken
Replace the leg spring
Mobile hook unit does not
move upwards
Ball valve to lift limiter (H3)
defective or locked, e.g. by
jammed nose rod or defective
lever (both in the switch rod)
Clean or replace the valve,
make the switch rod mobile,
replace defective parts.
Pressure relief valve (H7)
defective or blocked
Clean or replace pressure relief
valve.
Hydraulic cylinder (2)
piston rod does not extend
Non return valve (H6)
defective
Replace non return valve
Mechanism for bottle bank
floor jammed
Rectify blockage of bottle bank
floor mechanism.
Bottle-bank releases
during the emptying
process
Container supported, height
monitor retracted, see 75.
The container must hang freely
(height monitor must be
extended)
Hooks do not open when
the bottle-bank is to be set
down
Height monitor (64) not
retracted
Retract height monitor
The unit does not switch
off or switches off too late
when the container floor is
closing
The nose rod (in the switch
rod) is worn out
Use the threaded rod to re-
adjust the switching point or
replace the nose rod.
The ball valve to the lift limiter
(H3) or part of the switch
linkage is defective
Replace defective part
Fixed hooks close
autonomously
Crane leak oil pressure (back
pressure)
Adjust the pressure relief valve
(adjusting the H7 pressure relief
valve)
Container goods do not
drop out of the container
Container goods have
become jammed
Close the container floor, loosen
the contents by shaking, try the
emptying procedure once again.
If this is unsuccessful, set the
container down and call in
specialist personnel to open it.
WARNING
No
-one may stand under the raised container or remain in the danger zone under
any circumstances. If the belt jams, do not attempt to release it by hand through
the container floor.
89. Positions for the KM920-12 safety stickers
Safety sticker
Order number
69: Mushroom system on the container (dimensions)
189058125
70: Function switch
189077101
75: Do not shore up the container while open
189078043
90.
Safety inspection / next inspection:
189012362
91.
Safety stickers in general
189012347
92. KM920-5, KM920-11, KM920-12 transport
Secure the attachment while it is being transported on the HGV, for example using a fixing
device as illustrated.
KM920-5, KM920-11 and KM920-12 maintenance
A service manual or a spare parts catalogue can be requested to carry out repairs or servicing
tasks.
Pay attention to cleanliness when carrying out maintenance work.
Clean hydraulic connections and their surroundings before opening to ensure that no dirt gets
into the hydraulic system.
If used under intensified working conditions, e.g. if operated on a construction site where there
are extreme levels of dirt, in multi-shift operation, if there are strong external influences or if
used frequently underwater, halve the maintenance intervals or carry out daily.
Maintenance intervals
Daily
weekly
Annually
Check hydraulic connections for
leaks and tighten if necessary
X
Grease at grease fittings
X
Check screw connections and
tighten if necessary
X
Check hydraulic hoses; if damaged,
replace.
Replace hydraulic hoses every 6
years at the latest.
X
Check pinned joints and safety
parts, tighten or replace if
necessary
X
Check for external cracks, wear,
corrosion and functional safety
X
Inspection according to regional
safety and health regulations
X
WARNING
If damage occurs, the attachment must not continue to be used.
Only carry
out welding work only after consulting the manufacturer and complying with the
welding instructions and specifications for the filler material.
Содержание KM920-11
Страница 64: ......