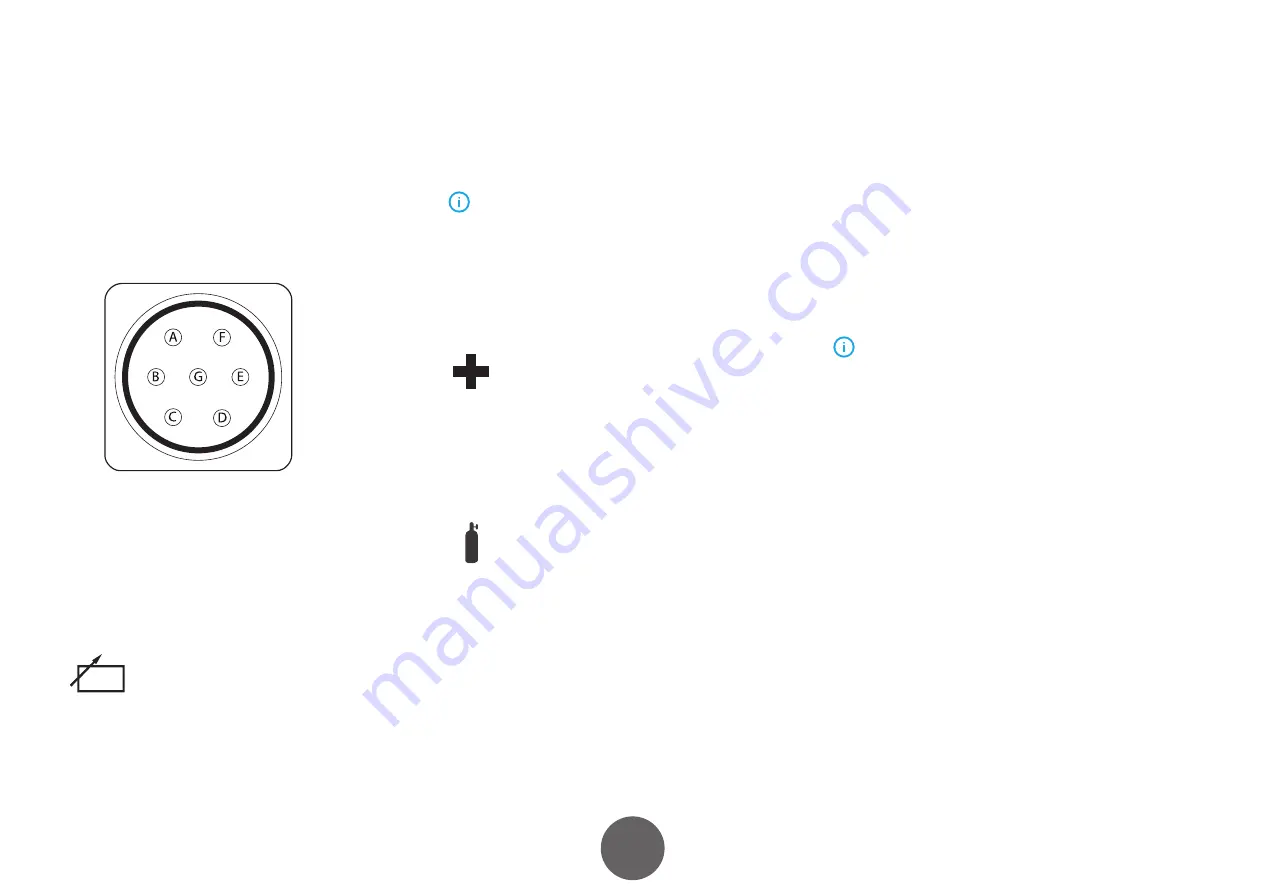
12
A7 MIG Welder
© Kemppi Oy 2020
2002
INTEGRA
TION GUIDE
3.8.2 Wire feeder control cable
The wire feeder control cable provides power to the wire
feeder and transmits the control data between the wire
feeder and the robot interface unit. It also contains the
touch sensor voltage line from the robot interface unit to
the wire feeder.
Figure 3.12: Wire feeder control cable connector pinout
A. Power supply GND
B. Data in/out
C. Power 50 V
D. (not connected)
E. Touch sensor voltage (+50…+200 V)
F. (not connected)
G. (not connected)
At the wire feeder, make the connection to the
control cable connector.
At the power source, connect the cable to the
control cable connector at the rear of the robot
interface unit.
At the power source, the connector must be connected
to the back of the robot interface unit. Do not use any other
control cable connectors.
3.8.3 Welding cable
The welding cable delivers welding power from the power
source to the welding head.
At the wire feeder, connect the cable to the screw
terminal on the front of the unit.
At the power source, connect the cable to the (+)
connector on the back of the power source unit.
3.8.4 Shielding gas hose
The shielding gas hose delivers the shielding gas to the
welding torch.
At the wire feeder, connect the hose to the shielding
gas snap connector.
Connect the other end of the hose to the shielding
gas supply.
3.8.5 Cooling hoses
Cooling hoses deliver the cooling liquid from the cooling
unit to the welding head.
• At the wire feeder, connect the cooling hoses
directly to the hoses coming from the welding
torch.
• At the power source, connect the cooling hoses
to the cooling unit located under the power
source.
The wire feeder does not have connectors for cooling
hoses. Use special adapters if required.
Содержание A7 350
Страница 1: ...350 450 1920310 2002 A7 MIG Welder A7 MIG Welder EN INTEGRATION GUIDE...
Страница 60: ...And you know...