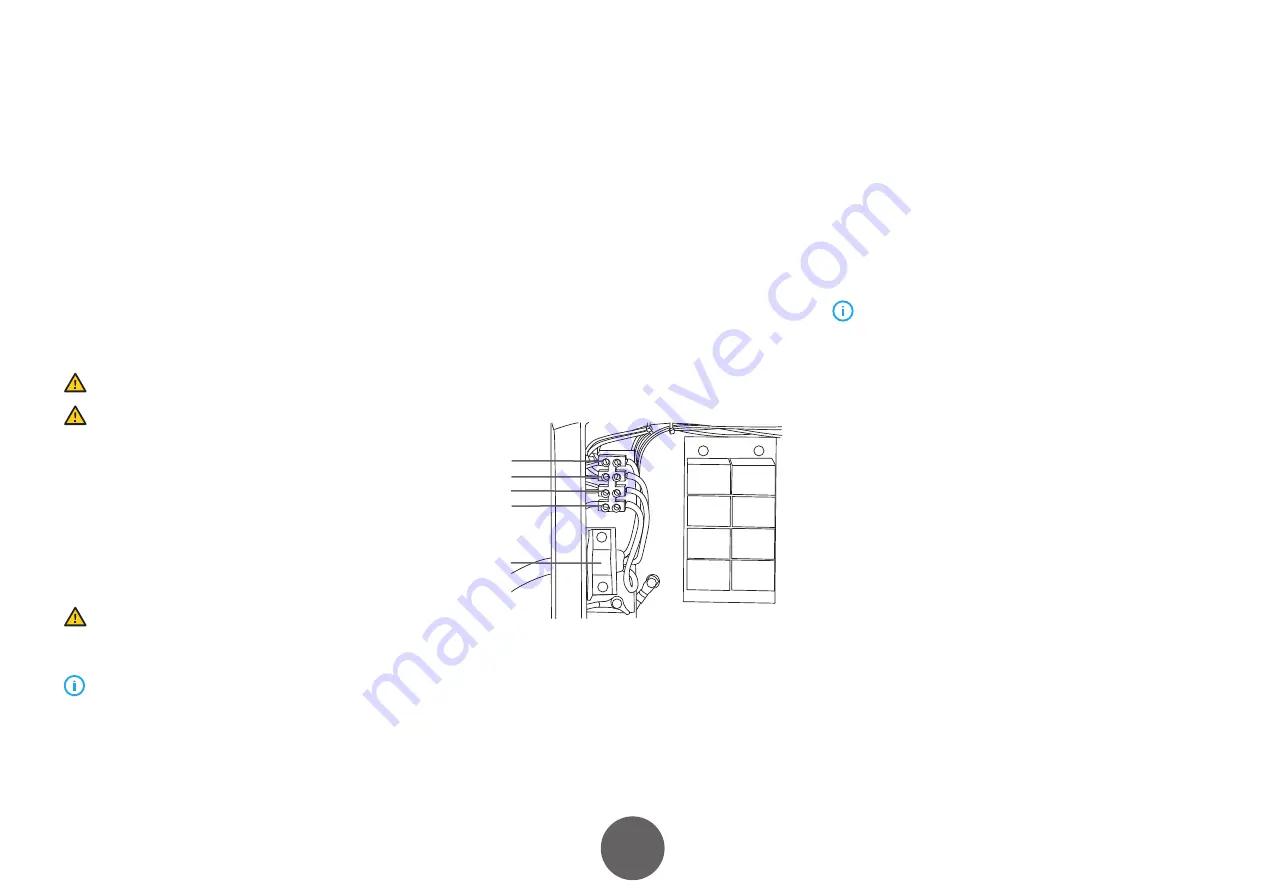
7
A7 MIG Welder
© Kemppi Oy 2020
2002
INTEGRA
TION GUIDE
3.3 Power source
Place the machine on a sturdy, level surface that is dry
and will not allow dust or other impurities to enter the
machine’s cooling air flow. Preferably, situate the machine
in a suitable carriage unit so that it is above floor level.
• The surface inclination may not exceed 15
degrees.
• Ensure the free circulation of cooling air. There
must be at least 20 cm of free space in front
of and behind the machine for cooling-air
circulation.
• Protect the machine against heavy rain and direct
sunshine.
Do not operate the machine in the rain.
Never aim the spray of sparks from a grinding machine
toward the equipment.
The power plug
The power source comes without a plug for connection
to the electrical grid. Attach a plug suitable for your
power-supply standard to the power cable. Check the
connections, attach the plug to a socket, and switch the
electrical power on from the welding power source to
verify that the machine works properly.
Switch the machine off, and unplug it from the power
socket before continuing to further steps in the hardware
installation.
If local or national regulations specify that an
alternative power cable is required, the cable must be
replaced in conformity with the regulations. Connection
and installation of the power cable and plug should be
carried out only by a suitably qualified person.
Remove the machine’s left-hand cover plate to enable
attachment of an electrical cable. The power source unit
can be connected to a 400 V, 3~ power supply.
If changing the power cable, take the following facts
into consideration:
• The cable enters the machine through the inlet
ring on the rear panel and is fastened in place
with a cable clamp (05).
• The phase conductors of the cable are coupled to
connectors L1, L2, and L3.
• The protective ground line, colored green and
yellow, is coupled to the marked connector.
• If you are using five-lead cable, do not connect
the neutral conductor.
05
*
L3
L2
L1
*
In S-type cables there is a protective grounding conductor,
green-and-yellow striped.
3.4 Cooling unit
If you use a water-cooled welding torch, you need a
cooling unit installed as part of the welder system. Attach
the cooling unit to the power source. See the detailed
installation instructions in the operating manual delivered
with the cooling unit package.
The cooling hose connections are described in
Subsection
3.8.5, “Cooling hoses.”
The wire feeder has no connectors for cooling hoses.
Use a special adapter to connect the cooling hoses to the
welding torch cooling connectors.
3.5 Wire feeder
Use a two-part mounting bracket to mount the wire
feeder securely on the robot arm. Fasten the upper part of
the bracket to the bottom of the wire feeder and the lower
part to the robot arm. Finish the installation by putting the
bracket parts together and fixing them in place with bolts.
See the illustrated instructions included in the product
delivery package.
Mounting brackets are available for the most commonly
used welding robots. See the complete list at
www.kemppi.com
.
The wire feeder connections are described in
Section 3.8,
“Interconnection cable set.”
Содержание A7 350
Страница 1: ...350 450 1920310 2002 A7 MIG Welder A7 MIG Welder EN INTEGRATION GUIDE...
Страница 60: ...And you know...