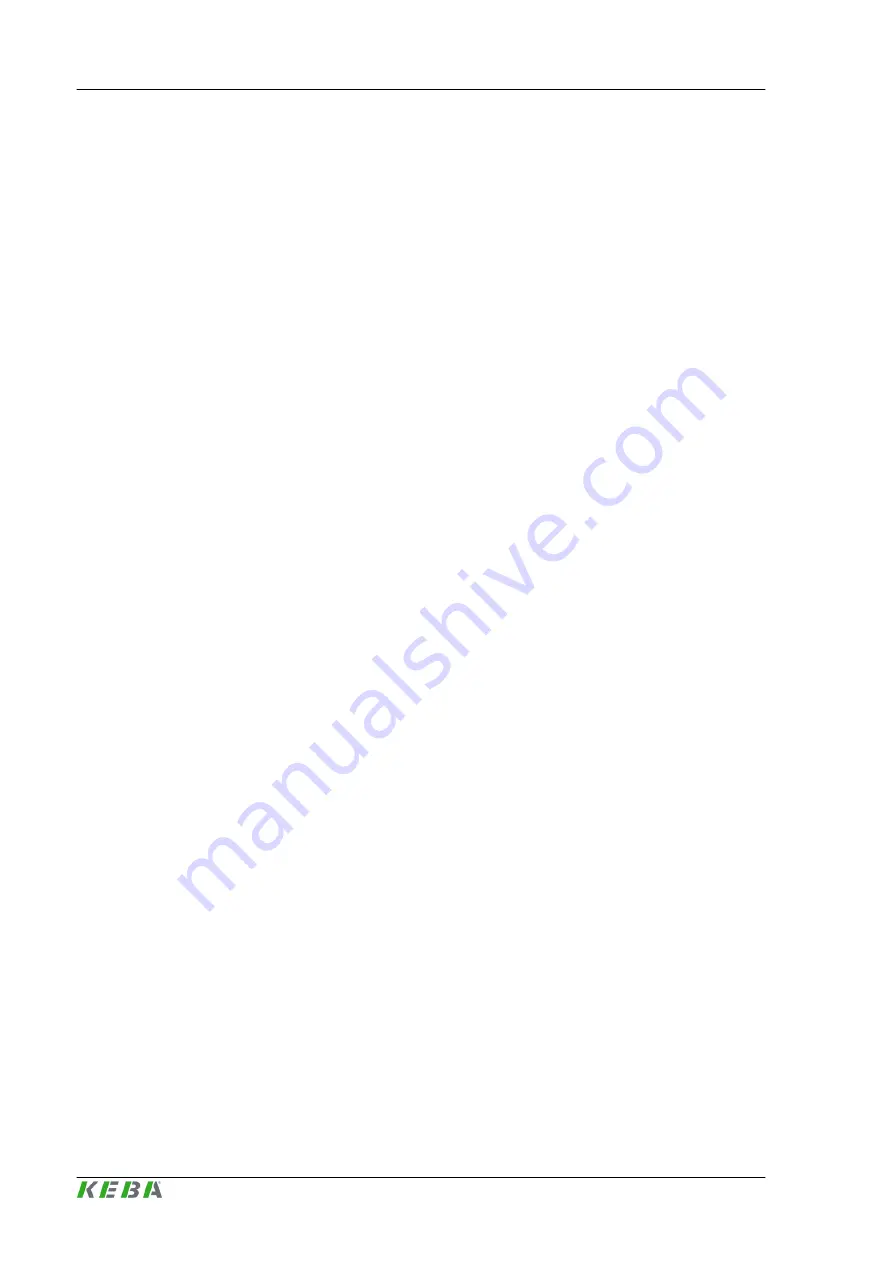
The display is quite reduced in function: It only allows the selection of prede-
fined icons representing mode and state information. There are several icon
sets available which are stored in the KeTop T10 itself.
The KeTop T10 has an Ethernet interface which allows exchanging information
with the control. The following information is exchanged between controller and
the device:
●
state of keyboard and joystick
●
current orientation of the device
●
current selected icons for display
As a communication protocol KVC (KEBA Virtual Channel) based on UDP/IP
designed by KEBA is used. The protocol also implements a transfer of param-
eters. Parts of the data exchange are handled cyclically like a live check to
detect connection errors between KeTop T10 is active.
The communication protocol is integrated into the firmware of the KeTop
T10. The firmware also contains all (inertial) sensor evaluation to derive the
orientation of the device.. Furthermore a small web server on the device allows
basic diagnosis and network settings.
Inertial sensor processing
The KeTop T10 contains a 6D IMU (inertial measurement unit), consisting of
3 accelerometers and 3 gyroscopes, which measure the motion of the device
in space. The sensor software contains all necessary sensor processing and
state control to provide the robot control with the current orientation of the de-
vice and filter undesired vibrations like e.g. from tremor of the hand of the
operator.
To get reliable orientation results from the sensors, the sensors have to be
calibrated at the beginning of operation. This is done automatically after power-
up as soon as the device is in rest position. Due to the inertial sensors the
KeTop T10 only can calculate the orientation relative to the starting orientation.
Therefore before operation the KeTop T10 has to be put in a defined orientation
relative to the robot. The automatically calculated orientation is stored as ref-
erence direction via the reference button.
Sensor errors lead to a growing deviation of the orientation in horizontal direc-
tion. To keep the quality of the orientation at a high level the KeTop T10 has
to be referenced about every 10 minutes. The user can check the accuracy of
the current orientation at any time by activating device's own orientation button.
The used gyro sensors (measuring angular speed), have a measurement
range of 2000°/s. If this range is exceeded it is necessary to restore the original
orientation by re-referencing.
3.2
Integration of the KeTop T10 into robot control
The KeTop T10 is equipped with an Ethernet interface for exchanging I/O data
between device and control. The hardware interface is compatible with the
System overview
KeTop T10
© KEBA 2014
Project engineering manual V1.02
18
Содержание Kemro KeTop T10
Страница 1: ...Kemro KeTop T10 Project engineering manual V1 02 Translation of the original manual ...
Страница 4: ......
Страница 8: ......