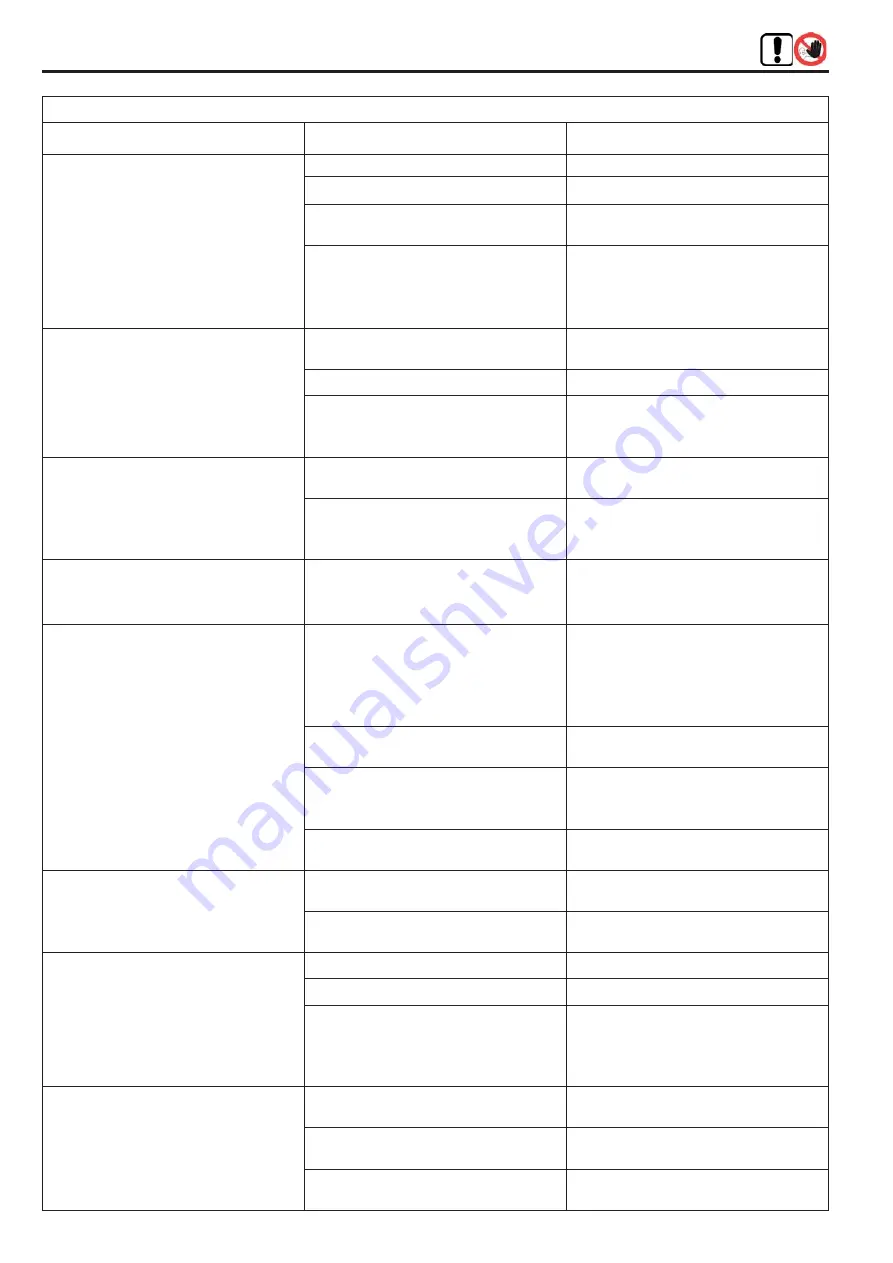
Trobleshooting guide
Failure
Possible reason
What to do
1) Airflow rate is lower than duty one.
Air filter(s) dirty.
Clean or replace air filter(s).
Plant air resistance higher than expected.
Check air plant project.
Adjusting dampers closed.
Open the dampers and
balance the plant.
Fans speed setpoint too low.
Increase fan speed by AHU Kit control panel.
Increase fan speed set point of VSD option, if pre-
sent.
2) Airflow rate is higher than duty one.
Internal component missing (filter ?).
Install the missing component (while unit is off)
Access panels open.
Close the access panels.
Plant air resistance lower than expected.
Balance the air plant by dampers.
Check plant project.
Reduce fan speed setpoint.
3) Heating/cooling capacity is lower than expected
Not enough air flow rate.
(See failure 1).
Valve control is not right.
Check connection between actuator and controller/
change temperature setpoint by remote control
panel.
4) Water condensate not discharged.
Syphon wrong or missing.
Install well-sized syphon.
5) The fans do not work.
The power supply is not inserted.
Check the power supply electric unit and the elec-
tric line upstream of the plant itself (by the User).
Check and if necessary restore the electrical con-
nections by qualified personnel.
The thermostat switches are not in the exact fun-
ctioning position.
Reposition the switches correctly and check their
status.
There are foreign bodies
that block the rotors.
Remove the foreign bodies from the impellers, and
keep them clean, check that there are no impedi-
ments, check their integrity.
Loosened electric connections.
Check presence of 0-10 V control signal (EC
motor).
6) Motor out of absorption.
Static pressure at that requested and therefore ex-
cessive flow rate.
It is possible to intervene by increasing the load
using dampers and adjusters.
Rotation speed too fast.
Check plant project.
Reduce fan speed setpoint.
7) Noise.
Excessive flow rate.
(See failure 2).
Wear or cracks in the bearings.
Contact the technical assistance service.
Presence of foreign material in the auger.
Remove the foreign bodies from the impellers, and
keep them clean, check that there are no impedi-
ments, check their integrity. Contact the technical
assistance service.
8) Strong vibrations.
Rotor unbalanced due to wear or deposits of dust.
Contact the technical assistance service.
The rotor rubs against the auger due to deforma-
tions.
Contact the technical assistance service.
Obstructions in the ducts.
Open the unit, check and clean the ducts, check
their tightness.
11 - IDENTIFYING BREAKDOWNS
pag.
41
Содержание KRE-1500DX1
Страница 1: ...KRE 1500DX1 KRE 2300DX1 KRE 3100DX1 INSTALLATION USER MAINTENANCE MANUAL Cross flow heat recovery ...
Страница 43: ... 13 SPARE PARTS pag 43 ...
Страница 45: ...NOTES ...
Страница 46: ...NOTES ...
Страница 47: ......
Страница 48: ......