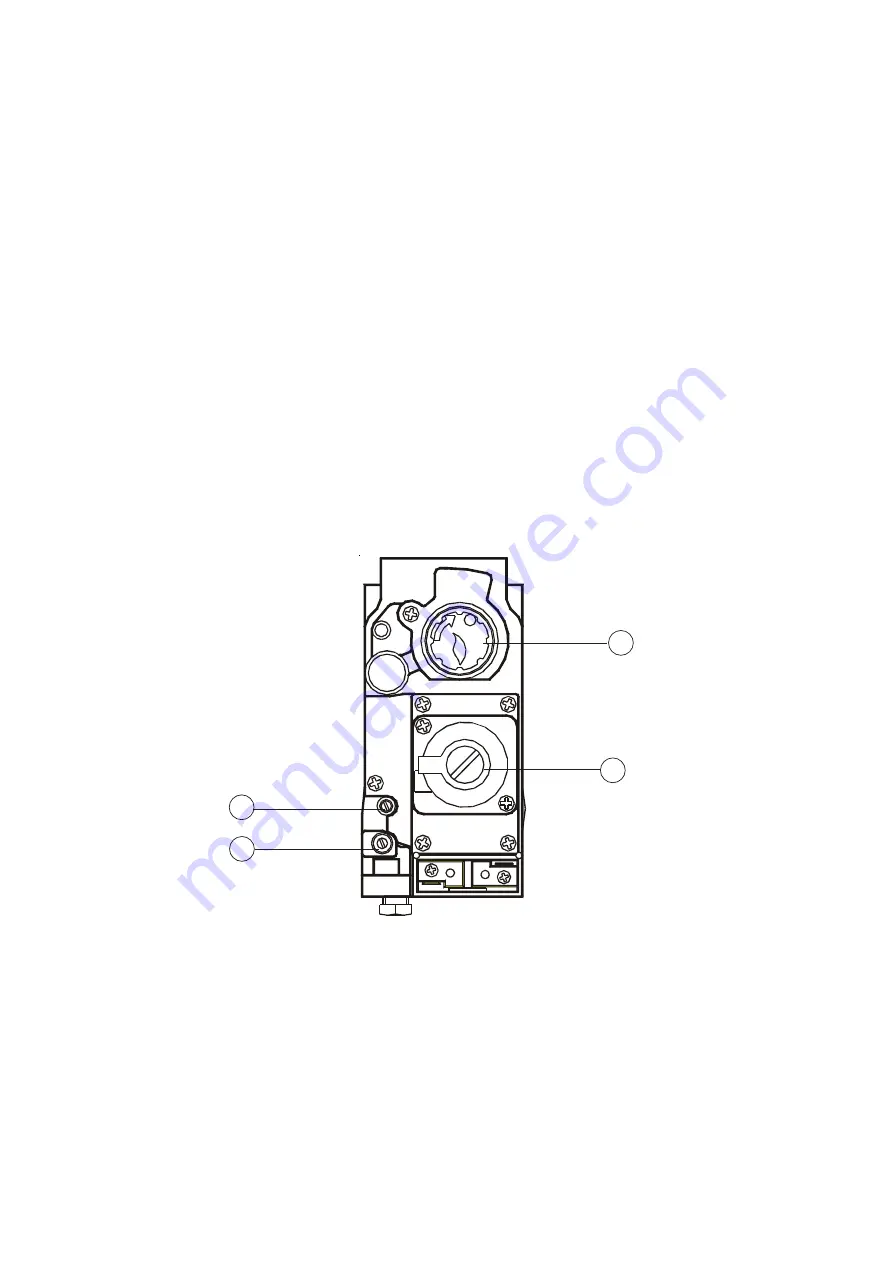
11
Sales/Spares & Replacement Help Line 01604 762881
Fig. 3
PILOT BURNER ASSEMBLY
6.4
MAIN BURNER PRESSURE TEST:
NOTE: AIR HEATER BURNERS ARE FACTORY SET TO PROVIDE A NOMINAL HIGH RATE OUTPUT AS
DETAILED IN SUB PARA 1.2
6.4.1
Referring to Table 4 and Fig. 4 below, ensure that the pressure test gauge indicates the correct burner pressure,
resetting if required as follows:
a.
At the Multifunctional Control:
i.
Remove the Burner Pressure Adjuster cover.
ii.
Set the Burner Pressure Adjuster to provide a pressure test gauge indication for the correct burner
pressure as detailed in Table 4
iii.
Refit the Burner Pressure Adjuster cover.
6.4.2 Apply the pressure set arrow to indicate the appropriate burner pressure on the data badge.
6.5
EXTINGUISHING OF BURNERS AND TEMPERATURE RISE TEST:
6.5.1
On the Multifunctional Control, rotate the OPERATING CONTROL clockwise to the ‘
l
’ position and ensure that
the OPERATING CONTROL fully resets, and both Pilot and Main Burners are extinguished.
6.5.2
On the Multifunctional Control, remove the pressure test gauge and refit the Outlet Pressure test point cover.
6.6
TEMPERATURE RISE CHECK:
6.6.1
Ignite the Pilot and Main Burners and allow 15 minutes for stability before continuing.
6.6.2
With the Main Burner operating continuously, check that the temperature rise across heater is between 45
o
C -
55
o
C, setting the fan speed accordingly, (decrease fan speed to increase temperature rise). For MODAIRFLOW
heaters, adjusting the balancing screw sets the fan speed; whilst for non-MODAIRFLOW heaters, the fan speed is
adjusted by selecting the fan speed at control panel (decrease voltage selection to decrease fan speed).
Note: Tapping 1 = 170V, Tapping 2 = 180V, Tapping 3 = 195V, Tapping 4 = 210V, Tapping 5 = 230V.
8
21
Thermocouple
Electrode
Pilot Burner
6.3.6
Ensure that the pilot flame envelops the thermocouple tip, adjusting the Multifunctional Control Pilot Adjuster as
required (refer Fig. 3).
6.3.7
Set the air heater Electricity supply
ON.
6.3.8
Set the Time Control to the required Heating On periods.
6.3.9
Set the Selector switch to ‘TIMED’.
6.3.10 Set the Thermista-stat or room thermostat to MAXIMUM.
6.3.11 Ensure that the main burner has now ignited.
6.3.12 Test for gas leakage at the supply, Multifunctional control, Pilot and Main burners using proprietary detection
fluid, sealing any leaks found.
6.3.13 Allow the heater to operate for a minimum of 15 minutes to ensure stability.
Fig. 5a, MODAIRFLOW CIRCUIT DIAGRAM
Fig. 3
PILOT BURNER ASSEMBLY
6.4
MAIN BURNER PRESSURE TEST:
NOTE: AIR HEATER BURNERS ARE FACTORY SET TO PROVIDE A NOMINAL HIGH RATE OUTPUT AS
DETAILED IN SUB PARA 1.2
6.4.1
Referring to Table 4 and Fig. 4 below, ensure that the pressure test gauge indicates the correct burner pressure,
resetting if required as follows:
a.
At the Multifunctional Control:
i.
Remove the Burner Pressure Adjuster cover.
ii.
Set the Burner Pressure Adjuster to provide a pressure test gauge indication for the correct burner
pressure as detailed in Table 4
iii.
Refit the Burner Pressure Adjuster cover.
6.4.2 Apply the pressure set arrow to indicate the appropriate burner pressure on the data badge.
6.5
EXTINGUISHING OF BURNERS AND TEMPERATURE RISE TEST:
6.5.1
On the Multifunctional Control, rotate the OPERATING CONTROL clockwise to the ‘
l
’ position and ensure that
the OPERATING CONTROL fully resets, and both Pilot and Main Burners are extinguished.
6.5.2
On the Multifunctional Control, remove the pressure test gauge and refit the Outlet Pressure test point cover.
6.6
TEMPERATURE RISE CHECK:
6.6.1
Ignite the Pilot and Main Burners and allow 15 minutes for stability before continuing.
6.6.2
With the Main Burner operating continuously, check that the temperature rise across heater is between 45
o
C -
55
o
C, setting the fan speed accordingly, (decrease fan speed to increase temperature rise). For MODAIRFLOW
heaters, adjusting the balancing screw sets the fan speed; whilst for non-MODAIRFLOW heaters, the fan speed is
adjusted by selecting the fan speed at control panel (decrease voltage selection to decrease fan speed).
Note: Tapping 1 = 170V, Tapping 2 = 180V, Tapping 3 = 195V, Tapping 4 = 210V, Tapping 5 = 230V.
8
21
Thermocouple
Electrode
Pilot Burner
6.3.6
Ensure that the pilot flame envelops the thermocouple tip, adjusting the Multifunctional Control Pilot Adjuster as
required (refer Fig. 3).
6.3.7
Set the air heater Electricity supply
ON.
6.3.8
Set the Time Control to the required Heating On periods.
6.3.9
Set the Selector switch to ‘TIMED’.
6.3.10 Set the Thermista-stat or room thermostat to MAXIMUM.
6.3.11 Ensure that the main burner has now ignited.
6.3.12 Test for gas leakage at the supply, Multifunctional control, Pilot and Main burners using proprietary detection
fluid, sealing any leaks found.
6.3.13 Allow the heater to operate for a minimum of 15 minutes to ensure stability.
Fig. 5a, MODAIRFLOW CIRCUIT DIAGRAM
9
1. Operating control
2. Burner Pressure Adjuster
3. Outlet Pressure test point
4. Pilot Adjuster
Fig. 4
MULTIFUNCTIONAL CONTROL
6.7
AUTOMATIC CONTROLS CHECK
6.7.1
Set the TIME CONTROL to
‘ON’.
6.7.2
Turn the Thermista-stat or room thermostat slowly clockwise until the Main Burner ignites.
6.7.3
Ensure that the fan starts to operate after a short period (approx. 1-2 minutes).
MODAIRFLOW models
:
6.7.4
Ensure that the fan speed increases to full speed.
6.7.5
When the temperature reaches the control setting, check that the Main Burner cycles ON and OFF, at approximately
75 to 120 seconds.
Non-MODAIRFLOW models
:
6.7.6
When the temperature reaches the control setting, ensure that the Main Burner extinguishes followed by the fan
switching off after a short period.
6.7.7 When the temperature falls below the control setting, ensure that the Main Burner re-ignites followed by fan
operation.
6.8
SAFETY CHECKS
:
6.8.1 Check for gas soundness within the appliance.
6.8.2
Spillage test:
Carry out a full spillage test as follows, and ensure that the flue operates effectively with all doors
closed and any extractor fans in operation.
NOTE:
If an extractor fan is situated in an adjoining or adjacent room, carry out the spillage test with the interconnecting
doors open.
If the draught diverter is accessible:
a.
Introduce smoke into the draught diverter adjacent to an exit from the heat exchanger, by means a smoke
match or puffer.
b.
Ensure that there is no spillage present (indicated by displacement of smoke downwards and out of the
draught diverter.
If the Draught Diverter is not accessible:
a.
Introduce smoke, by means of
part
of a smoke pellet on a non-combustible support, into the heat
exchanger.
b.
Extinguish the Main and Pilot burners.
c.
Ensure that there is no spillage evident by visually observing the draught diverter location on the air
heater.
d.
If spillage is evident, further investigation and rectification is required before re-testing the appliance.
e.
Repeat spillage tests but with the fan running, or Summer Airflow switch set to ON.
WARNING: The appliance shall not be left connected to the gas supply unless it has successfully passed
the above spillage test.
20
1
2
3
4
FAN CONTINUES TO RUN AFTER HEATING IS TURNED OFF
CHECK FAN SELECTOR
SWITCH SETTING
SET FAN SELECTOR
SWITCH TO
AUTO
N
Y
IS
SWITCH SET
TO AUTO ?
CHECK SUMMER AIR
CIRCULATION
SWITCH
IS
SWITCH SET
TO OFF ?
DOES
FAN STILL
RUN ?
DOES
FAN STILL
RUN ?
SET FAN SUMMER
AIR CIRCULATION
SWITCH TO OFF
N
Y
Y
Y
DOES
FAN STILL
RUN ?
DISCONNECT AIRFLOW
SENSOR
Y
DOES
FAN STILL
RUN ?
REPLACE
ELECTRONICS
MODULE
Y
IS
PILOT FLAME
TOO
BIG?
N
Y
ADJUST PILOT
FLAME TO CORRECT
SETTING
REPLACE
AIRFLOW SENSOR
N
Содержание 42-451-14
Страница 24: ...www johnsonandstarley co uk 24 11 WIRING DIAGRAMS Fig 5a MODAIRFLOW CIRCUIT DIAGRAM...
Страница 25: ...25 Sales Spares Replacement Help Line 01604 762881 Fig 5b Non MODAIRFLOW CIRCUIT DIAGRAM...
Страница 26: ...www johnsonandstarley co uk 26 12 FUNCTIONAL DIAGRAMS Fig 6a Non MODAIRFLOW FUNCTIONAL DIAGRAM...
Страница 27: ...27 Sales Spares Replacement Help Line 01604 762881 Fig 6b MODAIRFLOW FUNCTIONAL DIAGRAM...
Страница 28: ...www johnsonandstarley co uk 28 13 DIMENSIONS Fig 7 HI SPEC J65 DIMENSIONS...
Страница 29: ...29 Sales Spares Replacement Help Line 01604 762881 14 NOTES...
Страница 31: ...31 Sales Spares Replacement Help Line 01604 762881 16 EXPLODED DIAGRAM Fig 8 HI SPEC J65 EXPLODED DIAGRAM...