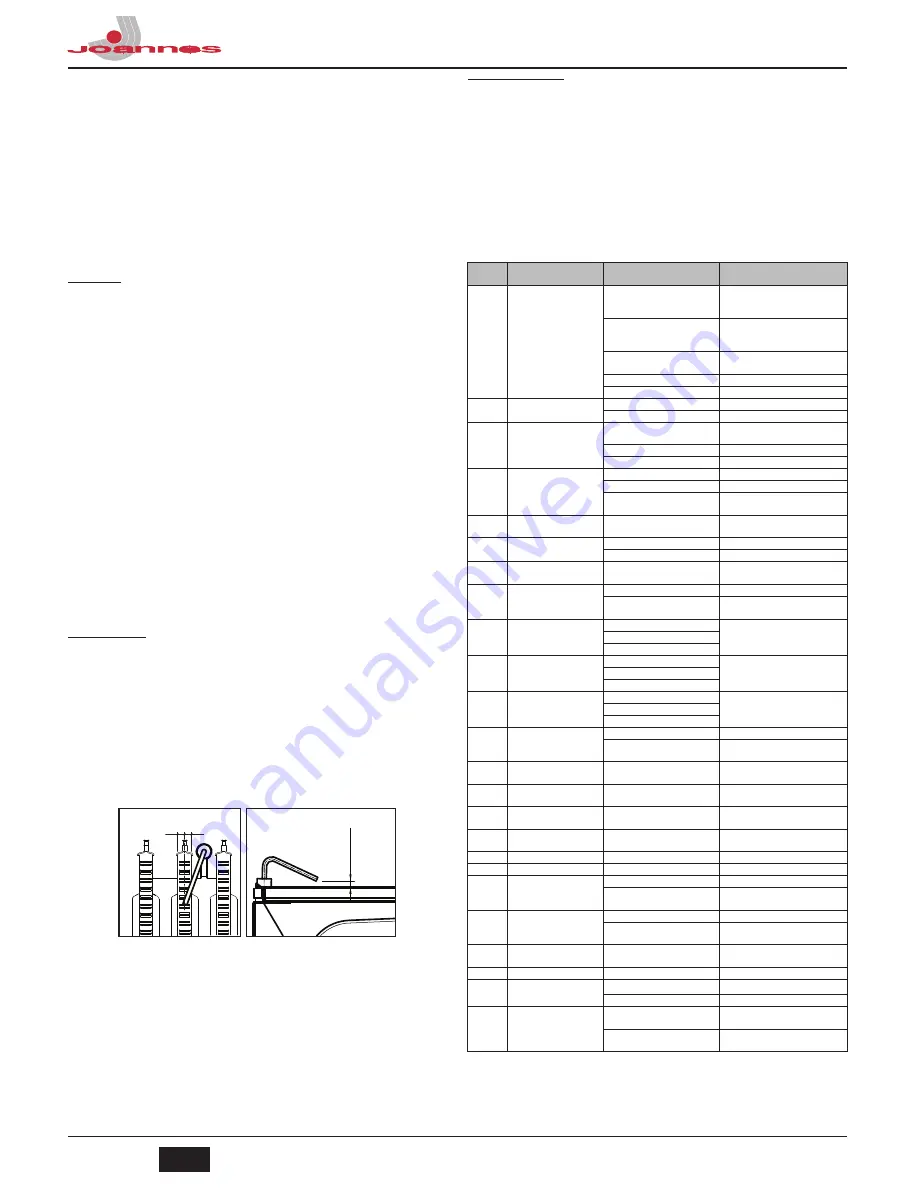
CLIZIA D LOW NOX 24 A
16
EN
cod. 3541D140 - Rev. 00 - 10/2012
"Hi" - History Menu
The card can store the last 11 faults: the History datum item H1: represents the most re-
cent fault that occurred; the History datum item H10: represents the least recent fault that
occurred.
The codes of the faults saved are also displayed in the corresponding menu of the Re-
mote Timer Control.
Press the Heating buttons to scroll the list of faults in increasing or decreasing order.
Press the DHW buttons to display the value.
Press the Reset button to return to the Service Menu. Press the Reset button for 20 sec-
onds to exit the card Service Menu, or exiting occurs automatically after 15 minutes.
"rE" - History Reset
Press the Eco/Comfort button for 3 seconds to delete all the faults stored in the History
Menu: the card will automatically exit the Service Menu, in order to confirm the operation.
Press the Reset button for 20 seconds to exit the card Service Menu, or exiting occurs
automatically after 15 minutes.
4.2 Startup
Before lighting the boiler
•
Check the seal of the gas system.
•
Check correct prefilling of the expansion tank.
•
Fill the water system and make sure all air contained in the boiler and the system
has been vented.
•
Make sure there are no water leaks in the system, DHW circuits, connections or boil-
er.
•
Check correct connection of the electrical system and efficiency of the earthing sys-
tem.
•
Make sure the gas pressure for heating is that required.
•
Make sure there are no flammable liquids or materials in the immediate vicinity of
the boiler
Checks during operation
•
Switch the unit on.
•
Check the tightness of the fuel circuit and water systems.
•
Check the efficiency of the flue and air/fume ducts while the boiler is working.
•
Make sure the water is circulating properly between the boiler and the systems.
•
Make sure the gas valve modulates correctly in the heating and domestic hot water
production stages.
•
Check correct boiler lighting by performing various tests, turning it on and off with
the room thermostat or remote control.
•
Make sure the fuel consumption indicated on the meter matches that given in the
technical data table in cap. 10.
•
Make sure that with no demand for heating, the burner lights correctly on opening a
hot water tap. Check that in heating mode, on opening a hot water tap, the heating
circulating pump stops and there is regular production of hot water.
•
Make sure the parameters are programmed correctly and carry out any required
customisation (compensation curve, power, temperatures, etc.).
4.3 Maintenance
Periodical check
To ensure correct operation of the unit over time, have qualified personnel carry out a
yearly check, providing for the following:
•
The control and safety devices (gas valve, flow meter, thermostats, etc.) must func-
tion correctly.
•
The fume exhaust circuit must be perfectly efficient.
(Sealed chamber boiler: fan, pressure switch, etc. -The sealed chamber must be
tight: seals, cable glands, etc.)
(Open chamber boiler: anti-backflow device, fume thermostat, etc.)
•
The air-fume end piece and ducts must be free of obstructions and leaks
•
The burner and exchanger must be clean and free of deposits. For possible cleaning
do not use chemical products or wire brushes.
•
The electrode must be properly positioned and free of scale.
fig. 12 - Electrode positioning
•
The gas and water systems must be airtight.
•
The water pressure in the cold water system must be about 1 bar; otherwise, bring
it to that value.
•
The circulating pump must not be blocked.
•
The expansion tank must be filled.
•
The gas flow and pressure must correspond to that given in the respective tables.
4.4 Troubleshooting
Diagnostics
The boiler is equipped with an advanced self-diagnosis system. In case of a boiler fault,
the display will flash together with the fault symbol (detail 11 - fig. 17) indicating the fault
code.
There are faults that cause permanent shutdown (marked with the letter "
A
"): to restore
operation, press the RESET button (detail 6 - fig. 17) for 1 second or RESET on the op-
tional remote timer control if installed; if the boiler fails to start, it is necessary to eliminate
the fault.
Faults marked with the letter "
F
" cause temporary shutdowns that are automatically reset
as soon as the value returns within the boiler's normal working range.
List of faults
Table. 2
3
±
0,5
=
=
Fault
code
Fault
Possible cause
Cure
A01
No burner ignition
No gas
Check the regular gas flow to the boiler
and that the air has been eliminated
from the pipes
Ignition/detection electrode fault
Check the wiring of the electrode and
that it is correctly positioned and free
of any deposits
Faulty gas valve
Check the gas valve and replace it if
necessary
Gas valve wiring disconnected
Check the wiring
Ignition power too low
Adjust the ignition power
A02
Flame present signal with
burner off
Electrode fault
Check the ionisation electrode wiring
Card fault
Check the card
A03
Overtemperature protection
activation
Heating sensor damaged
Check the correct positioning and
operation of the heating sensor
No water circulation in the system Check the circulating pump
Air in the system
Vent the system
F04
Fume thermostat activated
(after activation of the fume
thermostat, boiler operation
is prevented for 20 minutes)
Fume thermostat contact open
Check the thermostat
Wiring disconnected
Check the wiring
Flue obstructed or not correctly
sized
Check the flue
F05
Card parameter fault
Wrong card parameter setting
Check the card parameter and modify
it if necessary
A06
No flame after the ignition
phase
Low pressure in the gas system
Check the gas pressure
Burner minimum pressure setting Check the pressures
F07
Card parameter fault
Wrong card parameter setting
Check the card parameter and modify
it if necessary
A09
Gas valve fault
Wiring disconnected
Check the wiring
Faulty gas valve
Check the gas valve and replace it if
necessary
F10
Delivery sensor 1 fault
Sensor damaged
Check the wiring or replace the sensor
Wiring shorted
Wiring disconnected
F11
DHW sensor fault
Sensor damaged
Check the wiring or replace the sensor
Wiring shorted
Wiring disconnected
F14
Delivery sensor 2 fault
Sensor damaged
Check the wiring or replace the sensor
Wiring shorted
Wiring disconnected
A16
Gas valve fault
Wiring disconnected
Check the wiring
Faulty gas valve
Check the gas valve and replace it if
necessary
F20
Card parameter fault
Wrong card parameter setting
Check the card parameter and modify
it if necessary
A21
Card parameter fault
Wrong card parameter setting
Check the card parameter and modify
it if necessary
A23
Card parameter fault
Wrong card parameter setting
Check the card parameter and modify
it if necessary
A24
Card parameter fault
Wrong card parameter setting
Check the card parameter and modify
it if necessary
F34
Supply voltage under 180V. Electric mains trouble
Check the electrical system
F35
Faulty mains frequency
Electric mains trouble
Check the electrical system
F37
Incorrect system water pres-
sure
Pressure too low
Fill the system
Water pressure switch damaged or
not connected
Check the sensor
F39
External probe fault
Probe damaged or wiring shorted Check the wiring or replace the sensor
Probe disconnected after activat-
ing the sliding temperature
Reconnect the external sensor or disa-
ble the sliding temperature
A41
Sensor positioning
Delivery sensor or DHW sensor
detached from the pipe
Check the correct positioning and
operation of the sensors
F42
Heating sensor fault
Sensor damaged
Replace the sensor
F43
Exchanger protection trips.
No system H
2
O circulation
Check the circulating pump
Air in the system
Vent the system
F50
Gas valve fault
Modulating Operator wiring discon-
nected
Check the wiring
Faulty gas valve
Check the gas valve and replace it if
necessary
Содержание CLIZIA D LOW NOX 24 A
Страница 39: ......