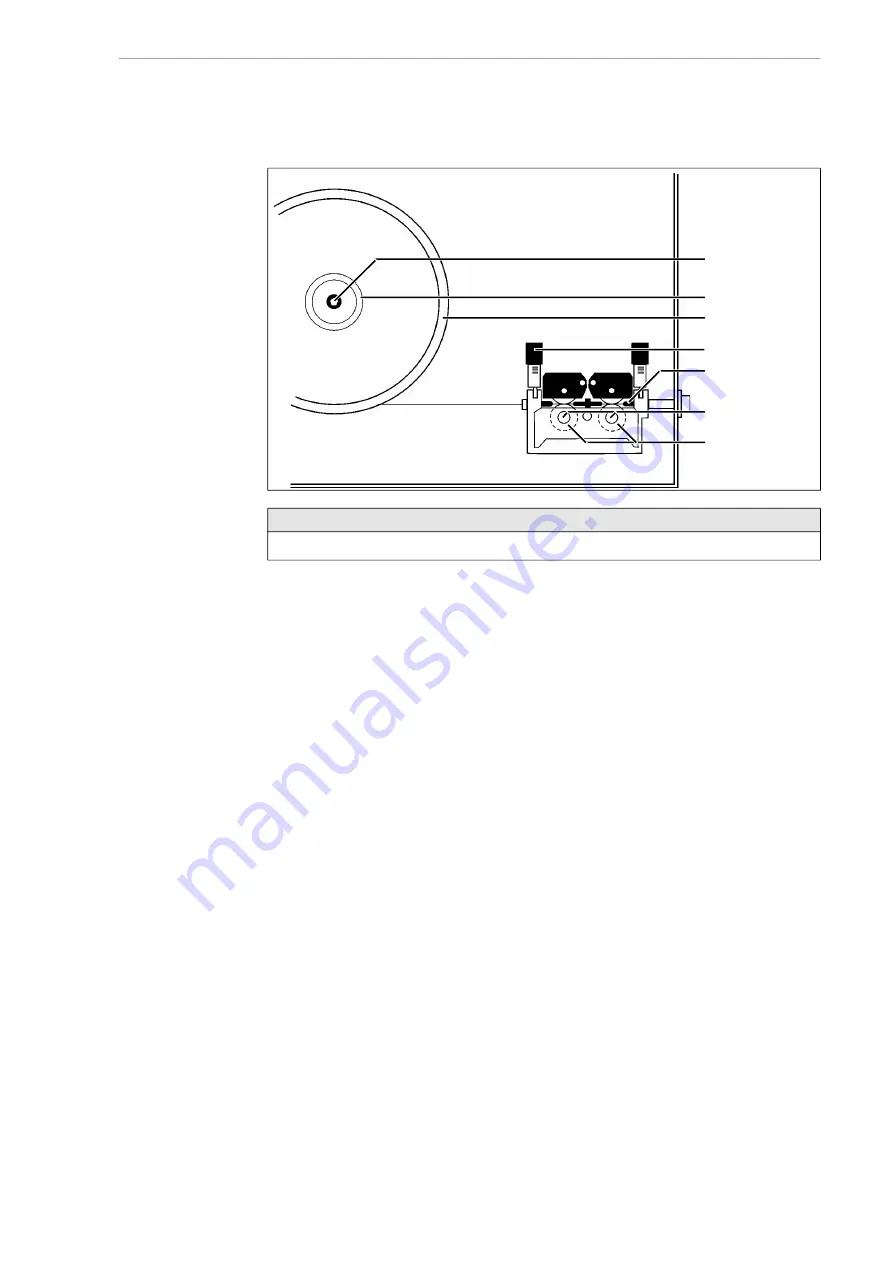
conMIG 300
10 Wire feeder
BA-0001 • 2020-12-01
EN
-
17
10 Wire feeder
10.1 Replacing the wire feed roller
1
Unscrew the knurled screw (F).
2
Ensure that the groove in the wire feed roller is aligned with the wire guide tube (E).
3
Ensure that the wire feed roller is installed in the correct position. Insert the wire feed roller in such a way
that the required size (e.g. 0.8) can be read from the front.
Use the spring pressure unit (D) to set the contact pressure of the wire feed roller so that the wire is fed
uniformly and does not buckle when the cable assembly is extended.
10.1.1 Wire spool brake
The wire-holding arbor (B) is equipped with a spool brake to prevent the wire spool (C) from continuing to
run when the wire feeder motor stops. You can increase the braking effect by turning the hexagon socket
screw (A) clockwise.
10.1.2 Wire guiding in the welding torch cable assembly
The friction resistance of the welding wire in the wire guide coil increases with the length of the cable
assembly. Therefore, the cable assembly should only be as long as necessary. When processing aluminium
welding wire, it is recommended that you replace the wire guide spiral with a Teflon wire guide liner. The
torch cable assembly must not exceed a length of 3 m.
We recommend air-blasting the wire guide spiral and the wire guide tube with compressed air after you
finish welding a spool of wire. The gliding quality of the wire guide spiral deteriorates in accordance with
the amount of wire that is fed and the wire properties. If wire guiding deteriorates noticeably, replace the
wire guide spiral.
Fig. 8
Replacing the wire feed roller
NOTICE
• Use a suitable groove for the respective wire diameter.
A
B
C
E
F
G
D