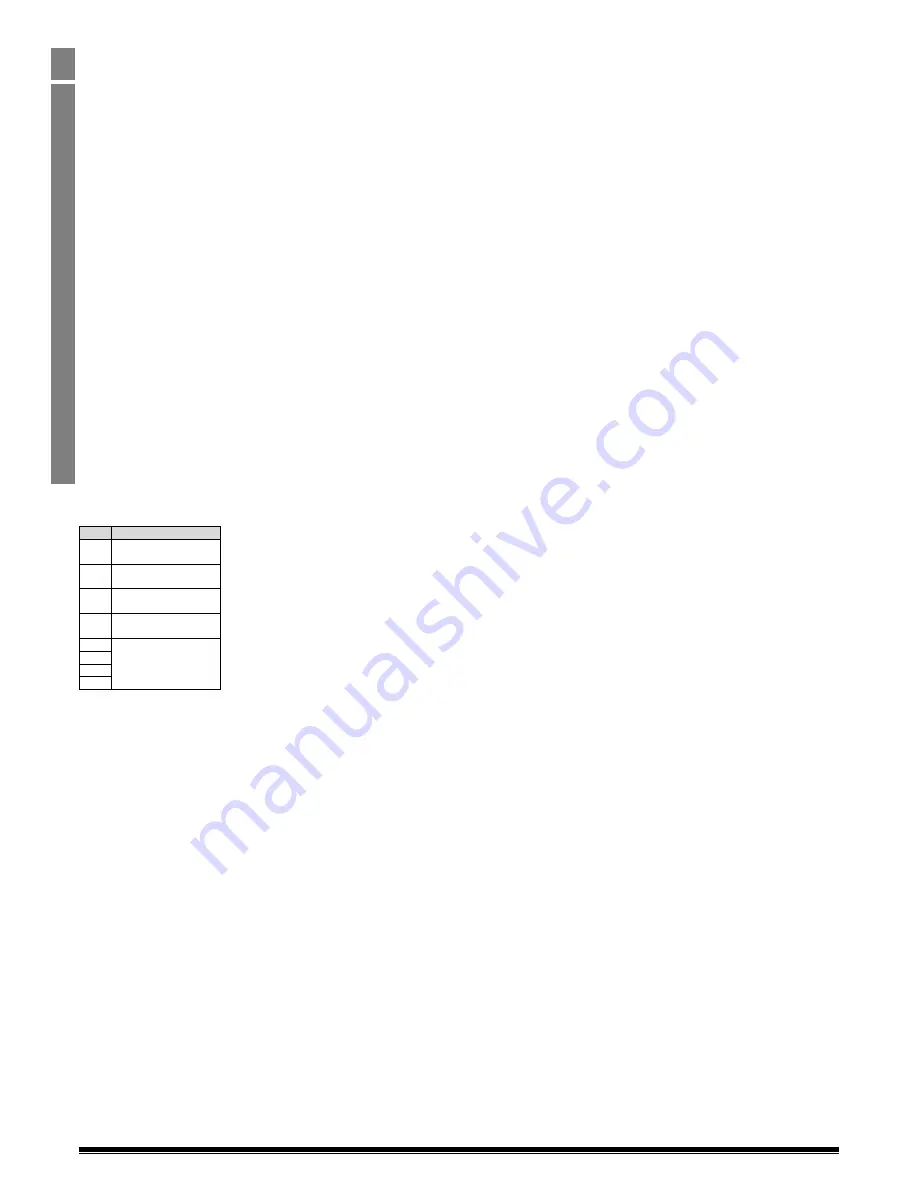
Optidrive ODP-2ETHEG-IN User Guide Revisions 1.00
12
www.invertekdrives.com
6
O
p
e
ra
ti
o
n
6.4.
Process Data Exchange
All Optidrives support a 4 word input, 4 word output process data exchange to allow control and monitoring of the drive. The functions and
overview of each word are described below.
6.4.1.
Process data Exchange Overview
All Optidrives support a 4 word process data exchange as follows:-
PDI : EIP Master
Drive
o
Word 1 : FIXED : Drive Control Word
o
Word 2 : FIXED : Frequency / Speed Setpoint
o
Word 3
Optidrive E3 : FIXED : No Function
Optidrive P2 / Eco : USER SELECTED Function determined by P5-14
o
Word 4
Optidrive E3 : FIXED : Ramp Control (When P-12 = 4 only)
Optidrive P2 / Eco : USER SELECTED Function determined by P5-13
PDO : Drive
EIP Master
o
Word 1 : FIXED : Drive Status
Low Byte : Drive Status Byte
High Byte : Trip Code
o
Word 2 : FIXED : Output Frequency / Motor Speed
o
Word 3
Optidrive E3 : FIXED : Output Current
Optidrive P2 / Eco : USER SELECTED : Function determined by P5-12
o
Word 4
Optidrive E3 : FIXED : No Function
Optidrive P2 / Eco : USER SELECTED : Function determined by P5-08
6.5.
Process Data PDI
6.5.1.
PDI Word 1: Drive Control Word
The drive control word can be used to control the drive as follows
Bit
Function
0
0: Stop
1: Run
1
0: Normal Operation
1: Fast Stop
2
0: No Function
1: Fault Reset Request
3
0: Normal Operation
1: Coast Stop
4
No function
5
6
7
6.5.2.
PDI Word 2: Drive Speed Reference
The drive speed reference value has one decimal place, e.g. commanded value = 500, the drive setpoint frequency will be 50.0Hz.
6.5.3.
PDI Words 3 and 4
As described in section 6.4.1, process data words 3 and 4 may be fixed function or configurable function depending on the drive in use. The
possible functions are described below.
6.5.4.
Drive Torque Reference
Where supported by the drive and correctly configured in the drive parameters, the torque limit or reference may also be sent to the drive
using the fieldbus PDI. In this case, the value is sent with 1 decimal place, e.g. commanded value = 500, the drive torque setpoint will be 50.0%
6.5.5.
Drive Ramp Times
When the drive parameters are configured to allow control of the drive ramp times through fieldbus, this register specifies the drive
acceleration and deceleration ramp times.
For P2 and Eco drives, when Fieldbus Ramp Control is selected (P5-08 = 1)
For E3 drives, setting P-12 = 4
The input data range is from 0 to 60000 (0.00s to 600.00s for P2, 0.0 – 6000.0s for Eco)
6.5.6.
User Registers
For P2 and Eco drives, which have internal function block programming capability, data may be written to the User Registers. This allows control
functions to be achieved within the drive by linking to the Group 9 parameters. The values may also be used within the function block program.