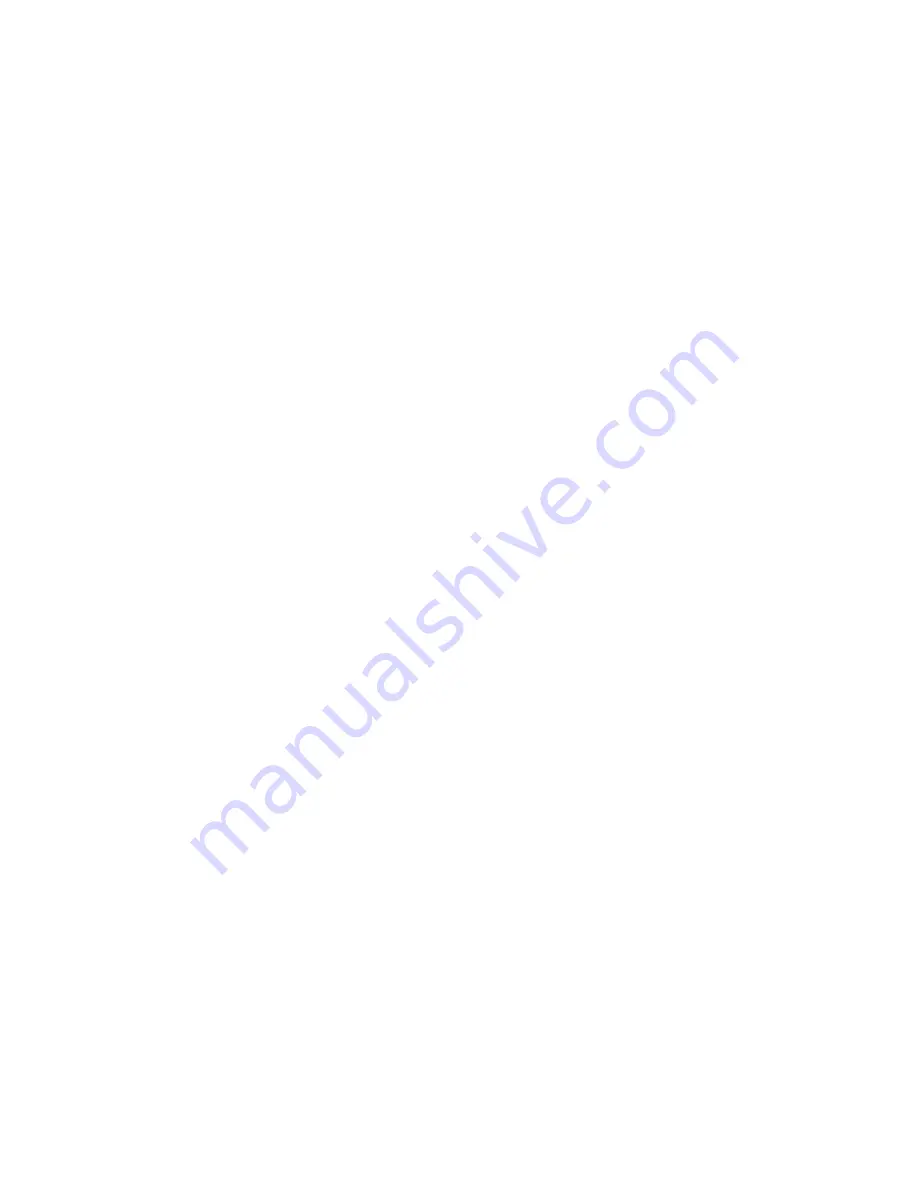
3.
Make sure that a vacuum is felt at the transducer end of the flex tube
during a start attempt. If vacuum is present, this assures the airend is
turning in the correct direction.
4.
Check for 5VDC on the transducer cable red and black wires at the
analog board.
5.
With the inlet vacuum transducer fully connected, check for a millivolt
reading on the green and white wires on the transducer cable at the
analog board. The range is 0 millivolts at 0 pressure, and 50 millivolts
at 15 psi vacuum.
6.
Make sure that the inlet valve closes fully during the first ten seconds
after the start button is depressed. The closed inlet valve causes a high
vacuum under the inlet valve, which confirms correct rotation.
7.
If 5 VDC is not found on the red and black wires at terminals 3 and 4 on
the analog board terminal strip BTS-1, check the other transducers
3APT and 4APT red and black leads for 5 VDC. If the other red and
black transducer leads read 5 VDC and the inlet vacuum transducer
does not, replace the analog board.
8.
If 5 VDC is available at the analog board terminals at the red and black
lead, but no millivolts are read on the green and white leads while a
vacuum is applied to transducer, replace the transducer or cable.
VOLTAGE CHANGE FOR AMBER "POWER ON" LIGHTS
(50 THROUGH 450 HORSEPOWER)
To improve bulb life for the two amber "Power On" lights on 50-450 horsepower
units, a change from 110V to 24V has been made.
Original units had 110V "Power On" lights connected to the Starter Interface
Board terminal strip BTS1 between terminals 4 and 35. The part number for a
complete 110V "Power On" light is 39478961 and the part number for a
replacement 110V bulb is 39132667.
Newer units have 24V amber "Power On" lights connected to the Starter
Interface Board terminal strip BTS1 between terminals 1 and 2. The part number
for a complete "Power On" light is 39485032 and the part number for a
replacement 24V bulb is 39485024.
The basic difference between either a 110 light and a 24V light is the bulb rating
and the connection points on BTS1.
WARNING
Prior to replacing any bulbs or making wiring changes, disconnect incoming
power and lock and tag the disconnect switch.
Should you desire to convert an older unit from 110V "Power On" lights to 24V,
install 24V bulbs and reconnect the light socket wires to BTS1 terminals 1 and
2 on the Starter Interface Board.
Whenever installing replacement bulbs on any unit, confirm the light voltage
supply matches the voltage rating of the bulb being installed.
This CFSM sheet is issued for information purposes only and field conversions
are not warrantable.
CONTROL VOLTAGE TRANSFORMER CONNECTIONS
(ALL UNITS)
When changing a unit from a lower operating voltage to a higher operating
voltage (Example: 230V to 460V) the control voltage transformer must be
properly reconnected or Intellisys damage will occur.
The damage results from higher than normal control voltage from an improperly
connected transformer.
The damage is easily identifiable and will be non-warrantable.
Refer to the connection diagram on the front of the control voltage transformer
and confirm the required reconnections have been made before applying
incoming power to the unit.
-89-
-90-
Содержание Intellisys SSR 10-40
Страница 32: ...29...
Страница 33: ...30...
Страница 72: ...70 FIGURE 1 INTERFACE MOUNTING LOCATION FIGURE 2 INTELLISYS CONTROLLER FIGURE 3 WIRING DIAGRAM 69...
Страница 73: ...70 FIGURE 1 INTERFACE MOUNTING LOCATION FIGURE 2 INTELLISYS CONTROLLER FIGURE 3 WIRING DIAGRAM 69...
Страница 74: ...71...
Страница 75: ...72...
Страница 76: ...72...
Страница 103: ...99 100 NOTES NOTES...
Страница 104: ...99 100 NOTES NOTES...
Страница 105: ...101 102 NOTES NOTES...
Страница 106: ...101 102 NOTES NOTES...