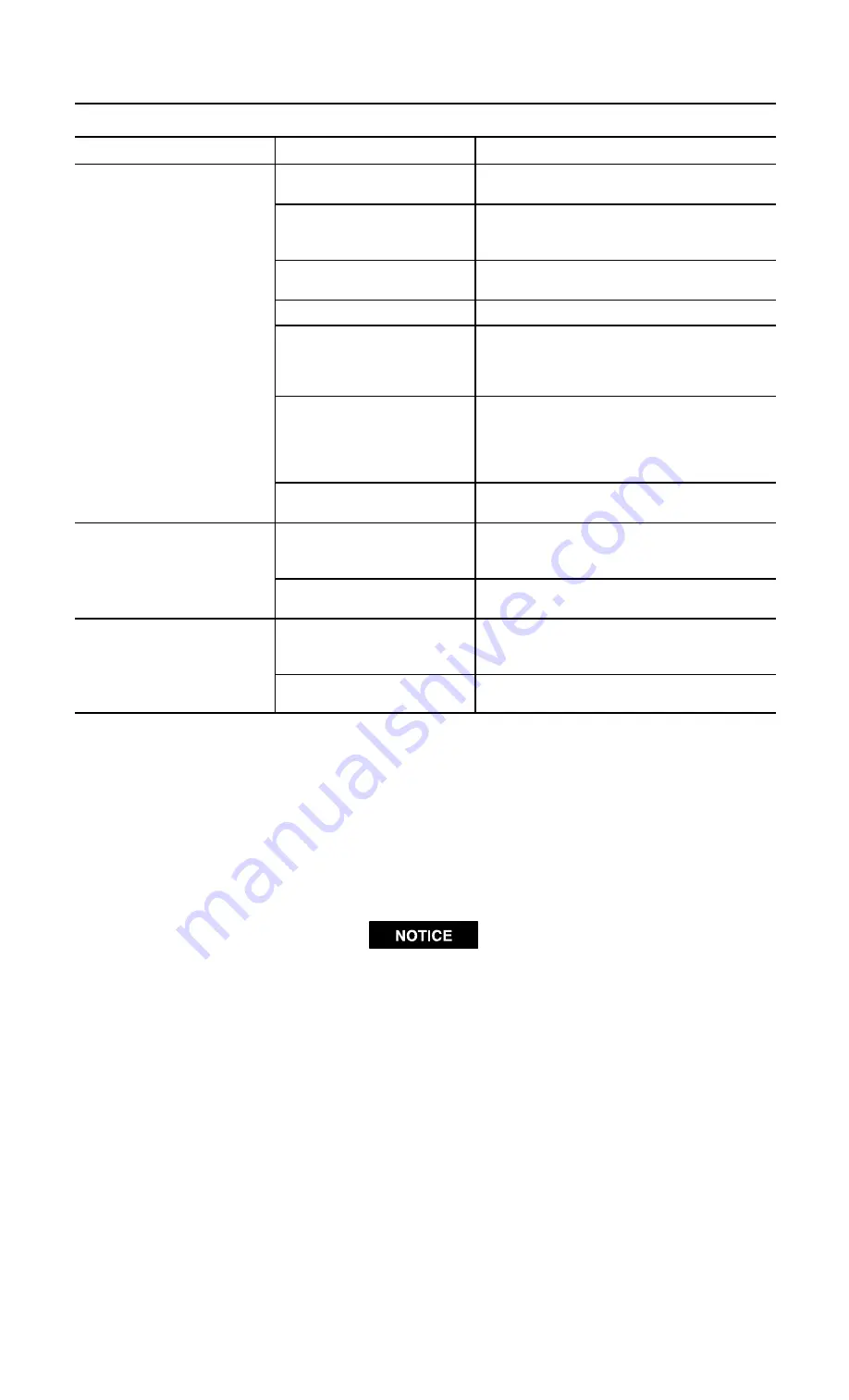
33
MAINTENANCE SECTION
TROUBLESHOOTING GUIDE
Trouble
Probable Cause
Solution
Low power
Dry Motor
Daily, inject 3 cc of Ingersoll–Rand No. 50 Oil into
the inlet and run the tool to lubricate the motor.
Inadequate air supply
Install proper air supply and connection. Refer to
Dwg. TPD905–1 and Dwg. TPD1674–1 on pages
2 and 3.
Dirty Inlet bushing Screen
Using a clean, suitable, cleaning solution in a well
ventilated area, clean the Inlet Bushing Screen.
Worn or broken Vanes
Replace a complete set of Vanes
Worn or broken Cylinder and/or
scored End Plates
Examine Cylinder. Check outside and ends for
wear or damage and inside for scored or wavy bore.
Replace Cylinder if any of these conditions exist.
Replace End Plates if they are scored.
Dirty motor parts.
Disassemble the Tool and clean in a clean, suitable,
cleaning solution in a well ventilated area.
Assemble the Tool and inject 3 cc of the
recommended oil into Inlet and run Tool to lubri-
cate internal parts.
Damaged Reverse Valve
Replace Reverse Valve. Refer to Installation of
Reverse Valve.
Motor will not run
Incorrect assembly of motor
Disassemble motor and replace worn or broken
parts and reassemble. Refer to Assembly of the
Motor.
Insufficient lubricant in impact
mechanism.
Lubricate impact mechanism through Hammer
Case Grease Fitting using the recommended grease.
Tool will not impact
Broken or worn impact mecha-
nism parts
Remove Hammer Case Assembly and examine im-
pact mechanism parts. Replace any worn or broken
parts.
Impact mechanism assembled
incorrectly.
Refer to Assembly of Impact Mechanism.
SAVE THESE INSTRUCTIONS. DO NOT DESTROY.