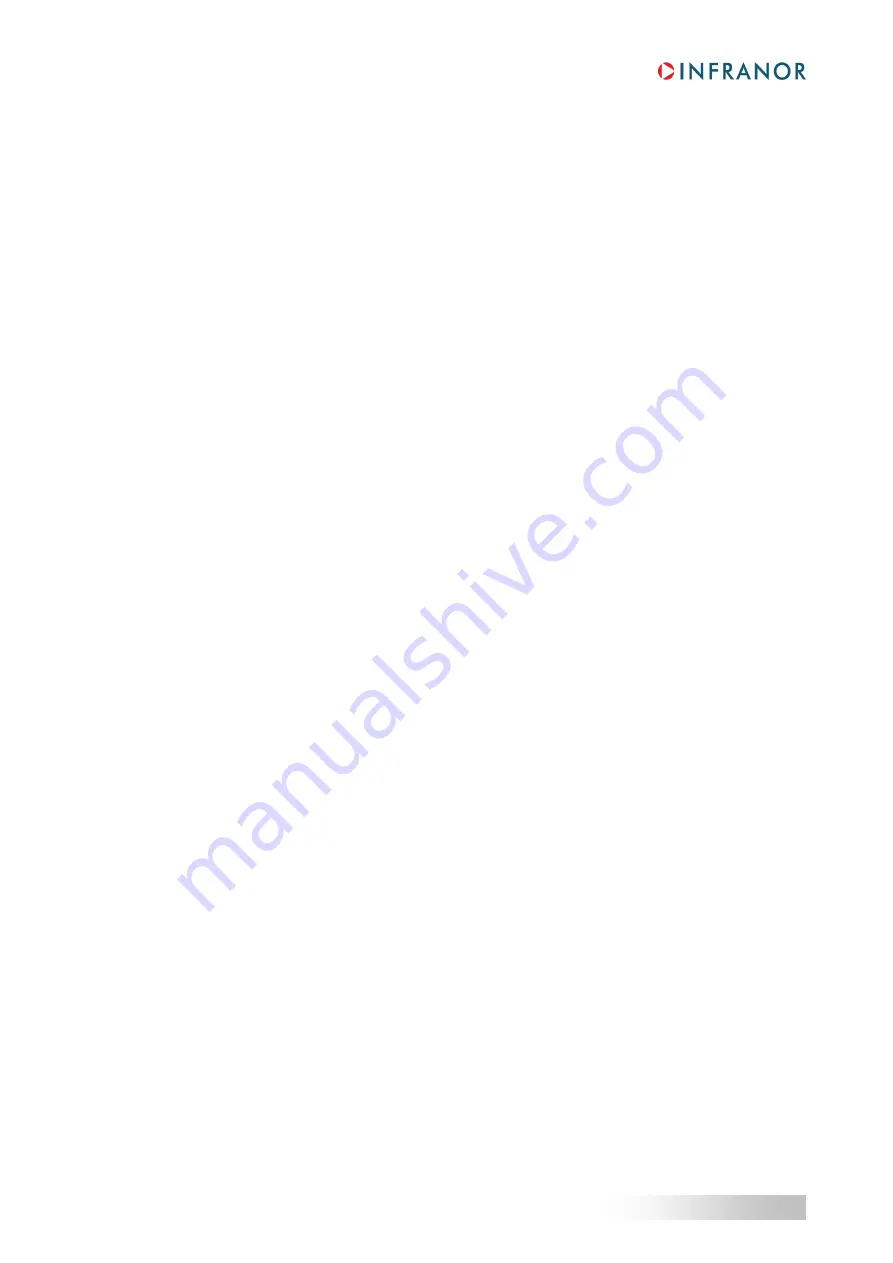
6
Chapter 1 - General description
XtrapulsCD1-pm
– Installation manual
Chapter 1
– General description
1- INTRODUCTION
Series XtrapulsCD1-pm Profibus positioners are PWM servo drives for the control of AC sinusoidal motors
(brushless) equipped with a position sensor.
The XtrapulsCD1-pm servo drive is available as a stand-alone single-axis block that includes all supplies and
mains filter. It is available in both mains operated versions 230 V
AC
and 400/480 V
AC
.
The XtrapulsCD1-pm positioner works with a PROFIBUS DP interface or in stand-alone by using only digital I/Os.
It generates itself the positioning trajectory that allows the programming of 128 positioning sequences.
2
– DESCRIPTION / COMPLIANCE WITH THE STANDARDS
2.1 - GENERAL DESCRIPTION
The XtrapulsCD1-pm drive directly controls the motor torque and speed by means of the information provided by
a high resolution position sensor (resolver or encoder). The sinusoidal current commutation based on this high
resolution position sensor provides very smooth motor torque/force control.
The XtrapulsCD1-pm drive can be configured for the feedback of various position sensor types. The appropriate
position sensor configuration is selectable by software and saved in the drive.
- With a resolver sensor feedback, the motor absolute position value over one revolution is available and the
servo motor can immediately be enabled after the drive power up.
- With a "SinCos tracks" sensor which provides two analog Sin and Cos signals electrically compliant with the
SinCos encoder signals and which period is equal to the motor pole pitch, the servo-motor can be immediately
enabled after the powering of the drive.
- With an absolute single-turn SinCos encoder feedback (Heidenhain ERN 1085 or compliant), the servo
motor can also immediately be enabled after the drive power up.
- With an incremental encoder only, a motor phasing procedure (Phasing) must be executed at each drive
power up before the motor enabling.
- With an incremental e Hall Effect Sensors (HES) feedback, the motor phasing procedure is no more
necessary and the servo motor can immediately be enabled after the drive power up.
- With an absolute single-turn, multi-turn or linear encoder using the ENDAT® or HIPERFACE® communication
protocols and fitted with incremental SinCos outputs, the servo-motor can also be immediately enabled after the
powering of the drive.
Series XtrapulsCD1-pm positioners have their own DC/DC converter to provide appropriate logic voltage to the
modules. An auxiliary 24 V
DC
+/- 15 % supply is generally available on all machines and supplies a DC/DC
converter with all logic supplies required by the positioner. The auxiliary supply allows to keep the logic board on,
after the power supply has been switched off, in order to keep all parameters in the memory and to avoid
initializing the machine all over again. A 24 V
DC
battery supply with specific wiring allows to keep the position
even after switching off the auxiliary 24 V
DC
supply. This wiring can be used for "absolute" operation with the
XtrapulsCD1-pm positioner (see chapter 4: Connections).
The power supply is depending on the positioner type:
•
XtrapulsCD1-pm-230/I: 230 V
AC
single-phase mains operation power supply with limitation of the
operation power (see chapter 2, section 1.1) or three-phase via a transformer or an autotransformer (or
direct three-phase mains operation if there are three-phase mains available in 200 to 230 V
AC
).
•
XtrapulsCD1-pm-400/I: 400 to 480 V
AC
three-phase mains operated power supply.
A soft start system of the power supply allows to limit the inrush current at power on.