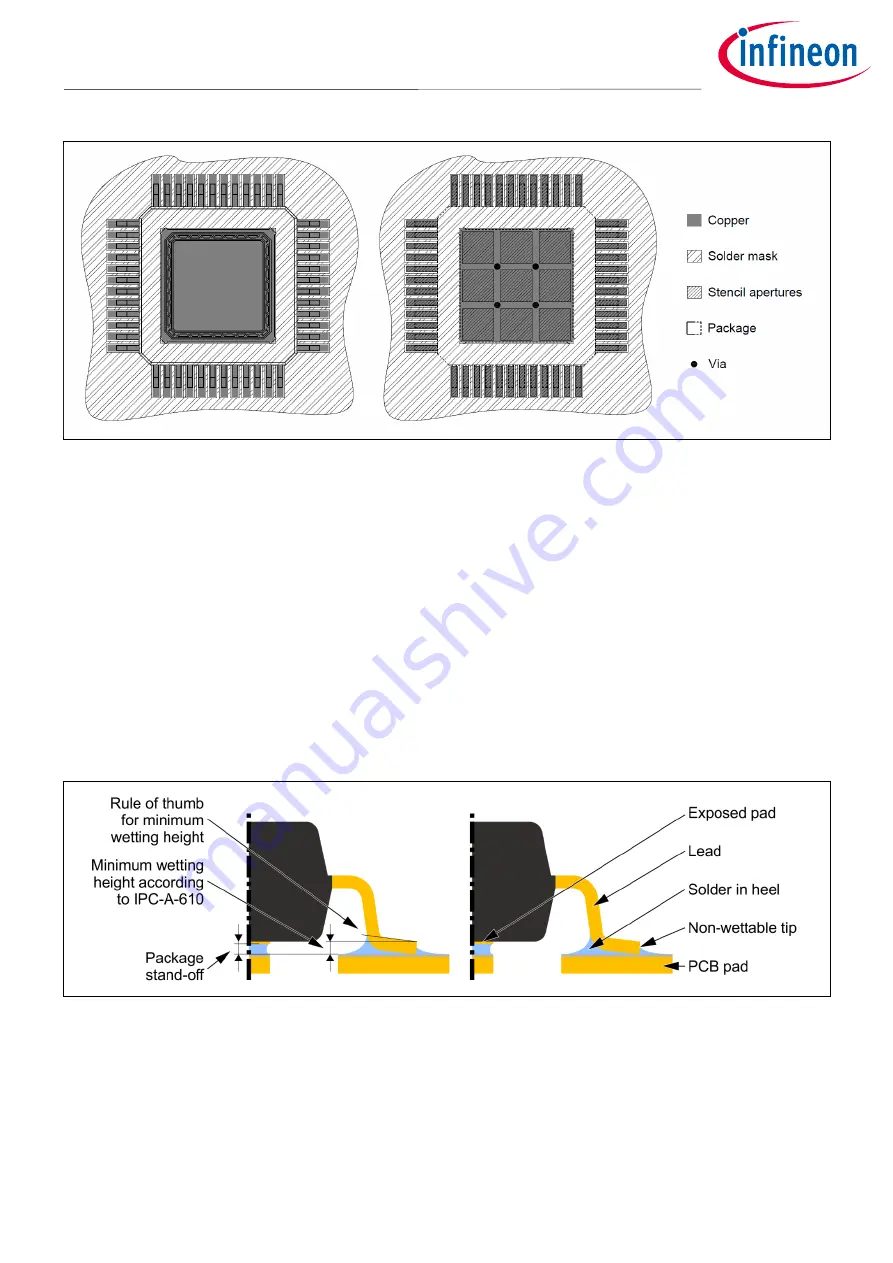
Additional Information
8 of 20
Revision 6.0
2020-11-12
Recommendations for Board Assembly of Infineon Quad Flat
Packages
Printed Circuit Board
Figure 5
Example of a pads and stencil design for QFP. The outer extension of the exposed pad
including the anti-flash profile is used as the reference for the PCB pad (left). Potential
vias-in-pad should be placed in between the stencil apertures to avoid solder flowing into
the vias (right).
shows schematic depictions of the backward PCB pad extension at the gullwing lead heel that is
necessary for an optimal solder fillet formation. According to the IPC-A-610 the minimum solder wetting height
shall reach an extended line projected from the lead tip top corner in parallel to the PCB pad plane [6]. As a rule
of thumb often the line parallel to the lead top plane is used to take into account the lower bend angle.
The PCB pad and therefore the solder paste print should have a distinct distance to the package mold in order
to avoid an unclean solder process as it is induced by e.g. solder spatters.
Generally, an optimal PCB design depends on the specific application as well as on the specific design rules of
the chosen board manufacturer.
Figure 6
Schematic depiction of a QFP mounted on a PCB. There are two critical parameters to
consider. First is the package stand-off between the landing plane of the exposed pad and
the copper plane of the PCB. The second is the pad extension for optimal solder fillet
formation at the gullwing heel according to the IPC-A-610 [6].
For further information about PCB pad design, please refer to the
General Recommendations for Borad Assembly
of Infineon Packages
document that is available on the Infineon web page [1]. Please also feel free to contact
your local sales, application, or quality engineer.