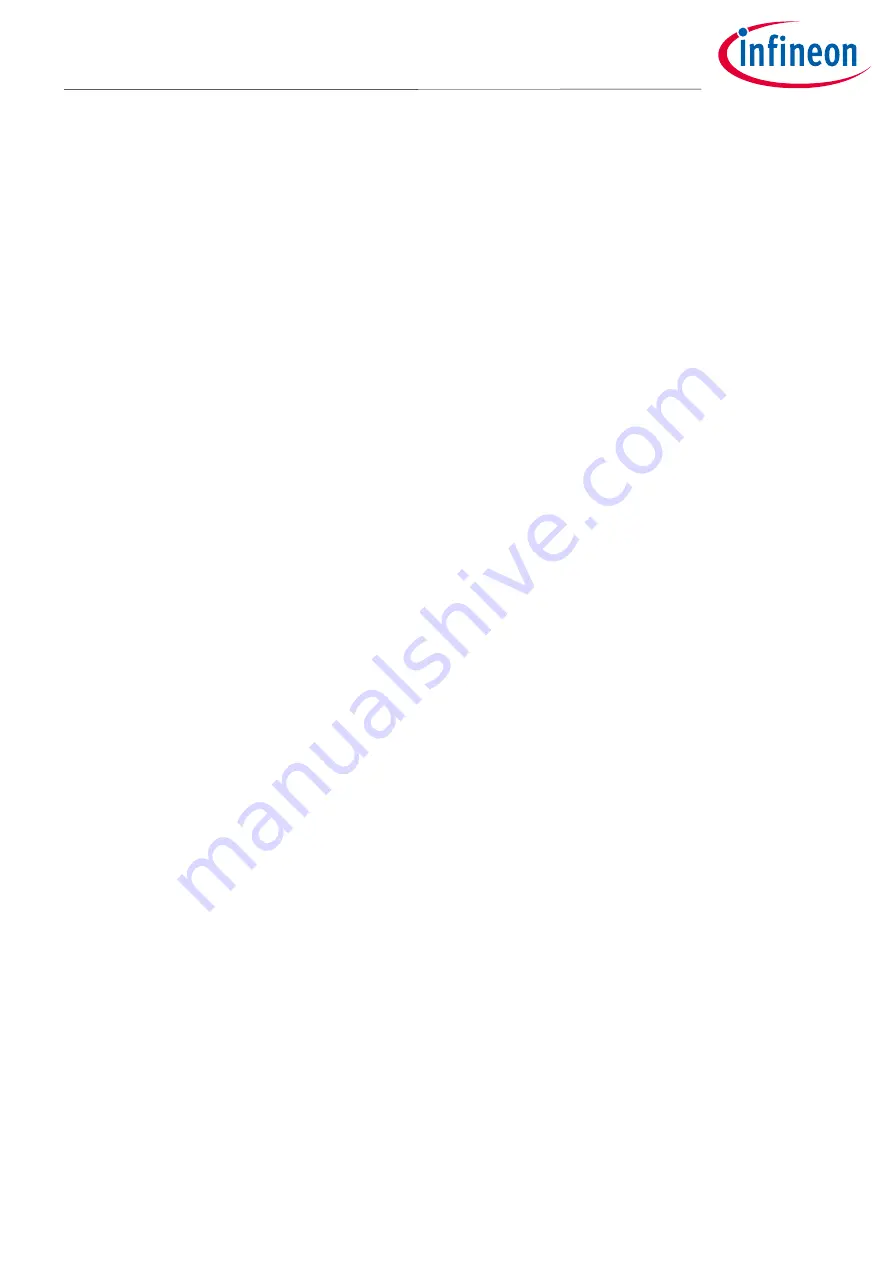
Additional Information
11 of 20
Revision 6.0
2020-11-12
Recommendations for Board Assembly of Infineon Quad Flat
Packages
PCB Assembly
3
PCB Assembly
3.1
Solder Paste Stencil
In SMT the solder paste is applied onto the PCB metal pads by stencil printing. The volume of the printed solder
paste is determined by the stencil aperture and the stencil thickness. While an excessive solder paste volume
will cause solder bridging, an insufficient solder paste volume can lead to reduced solder spreading between all
contact surfaces. To ensure a uniform and sufficiently high solder paste transfer to the PCB, laser-cut stencils
(mostly made from stainless steel) are preferred.
The stencil apertures are usually of the same dimensions as the relevant pad on the PCB. In most cases, the
thickness of a stencil has to be matched to the needs of all components on the PCB. For typical QFP with pitch
0.5 mm, stencils 130 µm to 150 µm (5 to 6 mil) thick are recommended. QFP with pitch 0.4 mm should be
printed with a maximum stencil thickness of 130 µm (5mil).
The solder paste volume in apertures larger than approximately 5 mm may be scooped out depending on the
specific squeegee pressure and rigidity. Such apertures necessary for many exposed pad prints, should be
segmented into smaller areas.
When reducing the die pad print the stand-off between gullwing landing area and exposed pad plane has to be
considered. The QFP stand-off can vary around the nominal value of 100 µm by ±50 µm. Therefore, the
recommended reduction of approx. 70% to 80% is lower compared with e.g. some leadless packages, where
pins and pads are in one plane. When choosing the print pattern and reduction, also the volume and height,
provided by the solder stencil thickness has to be considered. Areas on the pad, which are not covered by the
print, are preferred positions for vias as shown in
For individual design adaptations to reach the optimum amount of solder, the stencil thickness, the PCB pad
finish, solder mask quality, the via layout, and the solder paste type should be considered. In every case,
application-specific experiments are recommended.
Further details and specific stencil aperture recommendations can be found in the package data base that is
available on the Infineon web page [1]. Please choose a specific package when searching the data base, which
will then show an example of the stencil aperture layout for each package.
For further information about solder stencil design, please refer to the
General Recommendations for Board
Assembly of Infineon Packages
document that is available on the Infineon web page [1]. Please also feel free to
contact your local sales, application, or quality engineer.
3.2
Solder Paste
Pb-free solder pastes typically contain some type of SnAgCu alloy (SAC solder with typically 1-4% Ag and <1%
Cu). The most common alloy is SAC305 (3.0% Ag and 0.5% Cu). The average alloy particle size must be suitable
for printing the solder stencil aperture dimensions. Using Type 4 paste is recommended for the assembly of
QFP. The decision for lower type numbers and therefore higher grain sizes should depend on the specific stencil
aperture size and therefore solder paste transfer efficiency.
The solder alloy particles are dispersed in a blend of liquid flux and chemical additives (approx. 50% by volume
or 10% by weight), forming a creamy paste. The flux and chemical solvents have various functions such as
adjusting the viscosity of the paste for stencil printing or removing contaminants and oxides on the surface.
The solder paste solvents have to evaporate during reflow soldering, while residues of the flux will remain on
the joint. The capacity of the flux additive for removing oxides is given by its activation level, which also affects
the potential need for removing the flux residuals after the assembly. Generally, “no-clean” paste is
recommended to avoid subsequent cleaning steps underneath the package. The small gaps can make cleaning