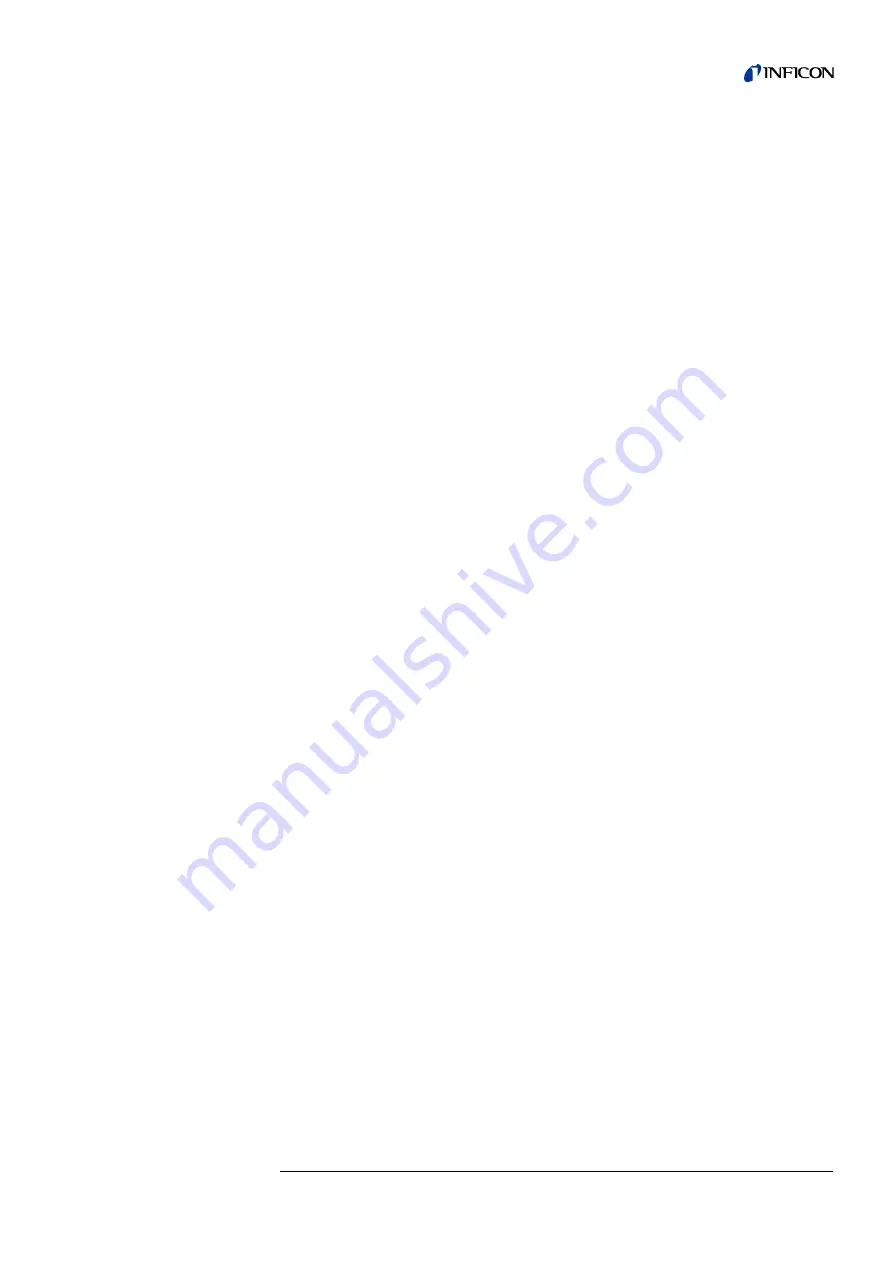
Table of Contents
3
iin
a
7
0
e
con
ten
t.fm
Tech
ni
ca
l Ha
nd
bo
ok
(1
40
8)
Table of Contents
7
Notes on the Use of this Handbook
Connections for the Data Acquisition Systems
Table of Contents
3
iin
a
7
0
e
con
ten
t.fm
Tech
ni
ca
l Ha
nd
bo
ok
(1
40
8)
Table of Contents
7
Notes on the Use of this Handbook
Connections for the Data Acquisition Systems