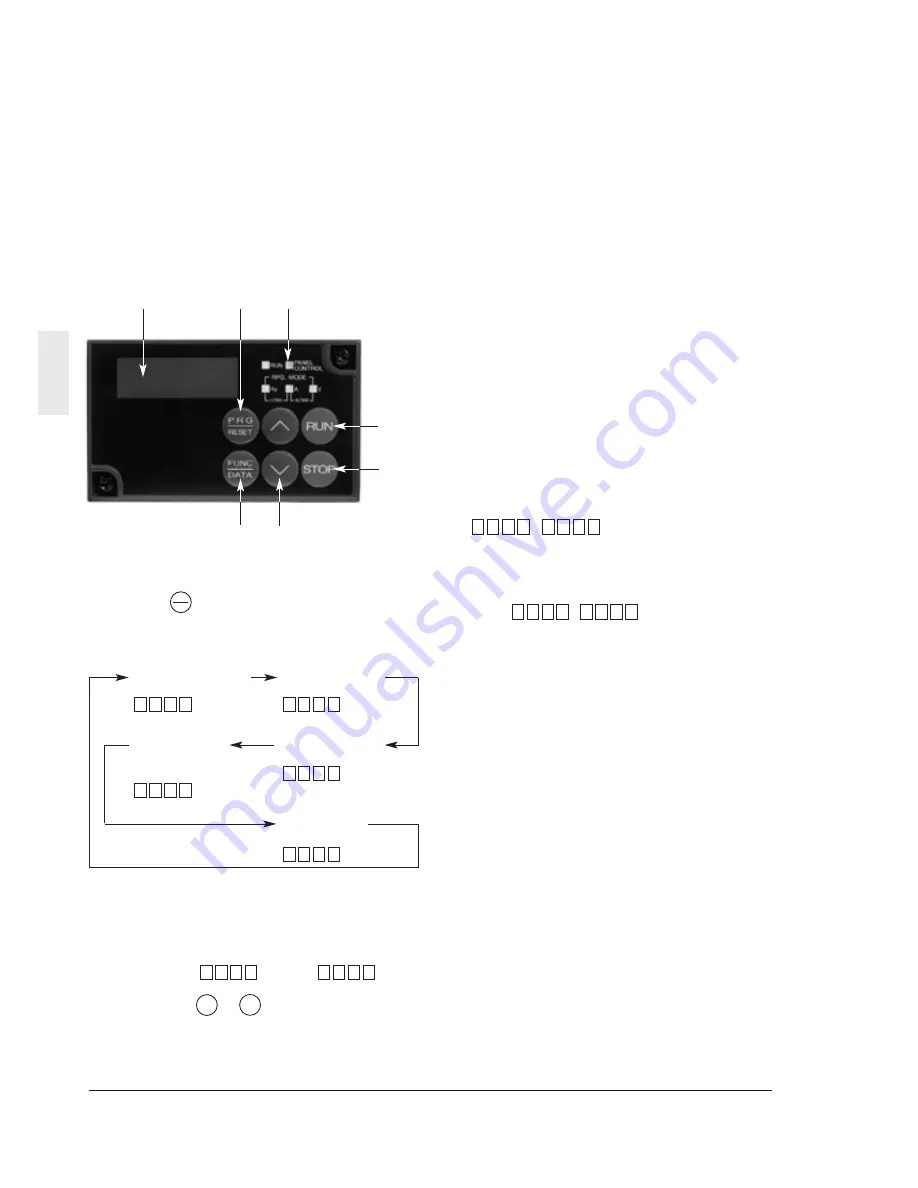
➀
Digital display
Various function codes and data codes for
programming are shown.
The output frequency, output current and
other data are displayed during operation,
and the cause of a trouble is displayed
using codes when protective function
works.
➁
Program (PRG)/RESET key
Press this key to switch over between the
regular operation mode and programming
mode. Use this key to reset an alarm
stopping state after activation of a protective
function.
➂
Unit and operation mode display
The unit of the data displayed at the digital
display is indicated with an LED. The
program mode is indicated. The PANEL
CONTROL lamp lights up in the keypad
panel operation mode.
➃
RUN key
Press this key to start operation. An LED
lights up during operation. When data code
=
, the key does not
function.
➄
STOP key
Press this key to stop operation. When data
code
=
, this key does not
function.
➅
Up/down keys
Press these keys to increase or decrease
the frequency or speed.
In the programming mode, use these keys
to change the function code or data setting.
➆
Function/Data key
Use this key to switch over between
frequency display, output current display
and other display in the regular operation
mode. In the programming mode, use this
key to retrieve or write various function
codes and various function data.
1
2
0
F
1
2
0
F
4-1
Keypad Panel
4
(1) Monitor display mode
In the regular operation mode, press the
key to switch between frequency
display, output current display and other
display.
4. Keypad Panel
The keypad panel is provided with various
functions such as operation (frequency setting
and start/stop commands) from the keypad
panel, monitor and alteration of function code
data, and various confirmation functions.
Be familiar with the operation method of each
function before starting operation.
4-1
Appearance of Keypad Panel
➀
➁
➆
➂
➅
➃
➄
FUNC
DATA
Output frequency *
1
0
0
0.
6
Output current *
2
0
2
1.
Output voltage *
2
0
0
2
Synchronization
rotation speed *
2
0
0
0
1
Line speed *
2
0
0
0
1
*1: In the PID control mode (when function H20
is at "1" or "2"), the value is in the percent
display and the dot at the least significant
digit always lights up.
Example: 10%:
, 100%:
*2: Press the , key during display of
these data to display the frequency setting.
0.
0.
0
1
0.
0.
1
V
V
Содержание VXSM150-1
Страница 3: ......
Страница 41: ...5 12 Selecting Functions 5 Frequency setting block diagram ...
Страница 45: ...5 16 Selecting Functions 5 Note The chain line indicates the motor speed ...
Страница 71: ...7 1 Troubleshooting 7 7 Troubleshooting 7 1 When Protective Function Activates 1 Overcurrent ...
Страница 72: ...Troubleshooting 7 2 7 2 Overvoltage 3 Undervoltage ...
Страница 77: ...7 7 Troubleshooting 7 3 The motor loses speed during acceleration 4 Excessive heat generation from motor ...