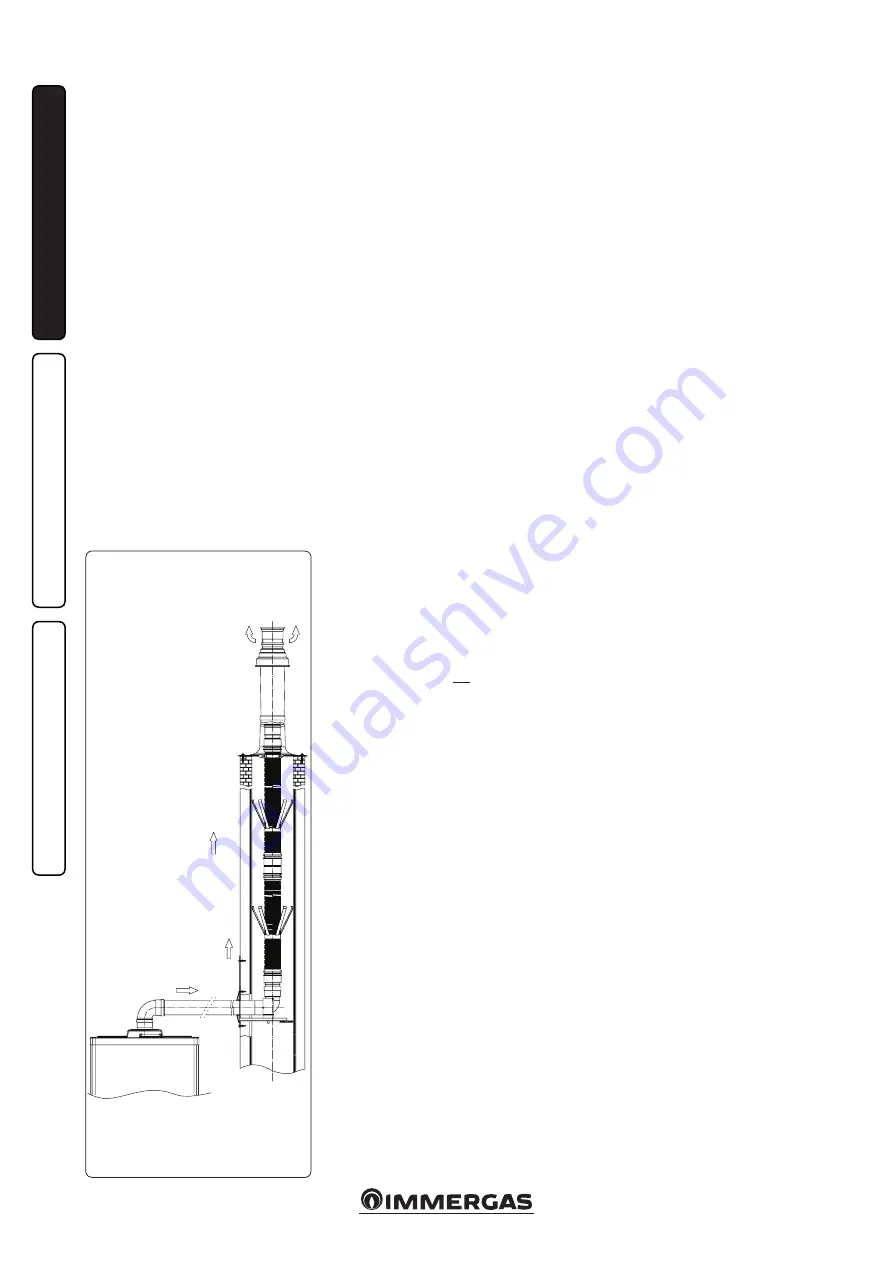
16
B23
1-23
INS
TALLER
US
ER
MAINTEN
AN
CE TECHNI
CI
AN
1.22 GAS SYSTEM START-UP.
To start up the system, refer to the technical
standard in force: This divides the systems and
therefore the start-up operations into three
categories: new systems, modified systems,
re-activated systems.
In particular, for new gas systems:
- open windows and doors;
- avoid presence of sparks or open flames;
- bleed all air from the pipelines;
- check the seal of the internal system by follow-
ing the instructions provided by the technical
regulations in force (refer to the pertaining lo-
cal regulations for the "sealing test" on systems
served by single or cascade generators with a
nominal thermal capacity greater than 35 kW.
1.23 BOILER START UP (IGNITION).
In order to issue the Declaration of Conformity
required by the regulations in force, one must
fulfil the following requirements to commission
the boiler (the operations listed below must only
be performed by qualified personnel and in the
presence of staff only):
- check that the internal system is properly sealed
according to the specifications set forth by
regulations in force; Up to operating pressures
of 40 mbar it is also possible to use the testing
method adopted by the technical regulations
in force for systems served by single appliances
(or in cascade set-up), with nominal thermal
capacities greater than 35 kW. For greater pres-
sure levels you will need to refer to legislation
in force and/or other effectively tried and tested
methods;
- make sure that the type of gas used corresponds
to boiler settings;
- check that there are external factors that may
cause the formation of fuel pockets;
- switch the boiler on and check correct ignition;
- make sure the fan rpm matches the value pro-
vided in the book (Par. 3.18);
- ensure that the safety device intervenes in the
event of gas supply failure and check the relative
intervention time;
- check activation of the main switch located
upstream from the boiler and in the boiler;
- check that the intake/exhaust concentric ter-
minal (if fitted) is not blocked.
The boiler must not be started up even if only
one of the checks should be negative.
N.B.:
the Immergas Authorised After-sales Centre
can carry out the initial boiler check (point 2.1)
required to activate the warranty of Immergas
solely upon completion of commissioning by an
installer. The test certificate and warranty is issued
to the user.
1.18 FLUE DUCT SYSTEMS FOR VOIDS
AND CHIMNEYS.
Flue ducts may be installed in suitable voids or
chimneys provided that the relevant building
regulations permit this. Flue ducting systems
must be installed in strict accordance with the
manufacturers instructions.
Immergas ducting system 80 Ø.
The "Green
Series" 80 Ø flexible ducting system must only be
used with Immergas condensing boilers.
In any case, ducting operations must respect
the provisions contained in the standard and in
current technical regulations; in particular, the
declaration of conformity must be compiled at
the end of work and on commissioning of the
ducted system. The instructions in the project
or technical report must likewise be followed, in
cases provided for by the standard and current
technical regulations. The system or components
of the system have a technical life complying with
current standards, provided that:
- it is used in average atmospheric and envi-
ronmental conditions, according to current
regulations (in particular, by the standards
regarding: absence of combustion products,
dusts or gases that can alter the normal ther-
mophysical or chemical conditions; existence
of temperatures coming within the standard
range of daily variation, etc.).
- Installation and maintenance must be per-
formed according to the indications supplied
by the manufacturer and in compliance with
the provisions in force.
- The max. possible length of the 80 Ø flexible
ducting vertical section
is equal to 28.0 m for
Victrix Pro 80
2ErP
, 14.0 m for Victrix Pro 100
2ErP
and 8.5 m for Victrix Pro 120
2ErP. This
length is obtained considering the complete ex-
haust terminal, 1m of 80 Ø pipe in exhaust, two
90° 80 Ø bends at the boiler outlet to connect to
the ducting system and two direction changes
of the flexible tube inside the flue/technical slot.
1.19
FLUE EXHAUST WITH BOILERS IN
CASCADE.
The boilers installed in cascade composed of
any number between 2 and 5 boilers, can be
manifolded to a unique flue exhaust pipe, which
flows into a flue.
Immergas supplied an appropriate and original
flue exhaust system separately to the boilers.
1.20 SYSTEM FILLING.
When the boiler has been connected, fill the sys-
tem. Filling is performed at low speed to ensure
release of air bubbles in the water via the boiler
and heating system vents.
The boiler incorporates two automatic vent
valves fitted on the circulator pump and on the
condensing module. Check if the cap is loose.
Open the radiator vent valves. Close radiator
vent valves when only water escapes from them.
N.B.:
during these operations start up the cir-
culation pump at intervals, acting on the main
switch positioned on the control panel.
Vent the
circulation pump by loosening the front cap and
keeping the motor running
. Tighten the cap after
the operation.
Attention:
this boiler is
not
equipped with an
expansion vessel on the system. It is mandatory
to install a closed expansion vessel to guarantee
correct boiler operation. The expansion vessel
must comply with the European Standards in
force. The dimensions of the expansion vessel
depend on the data relative to the central heating
system. Install a vessel whose capacity responds
to the requisites of the Standards in force (''R''
collection).
1.21 CONDENSATE TRAP FILLING.
On first lighting of the boiler combustion prod-
ucts may come out the condensate drain; after a
few minutes’ operation check that this no longer
occurs. This means that the trap is filled with
condensate to the correct level preventing the
passage of combustion products.
Exhaust
Exhaust