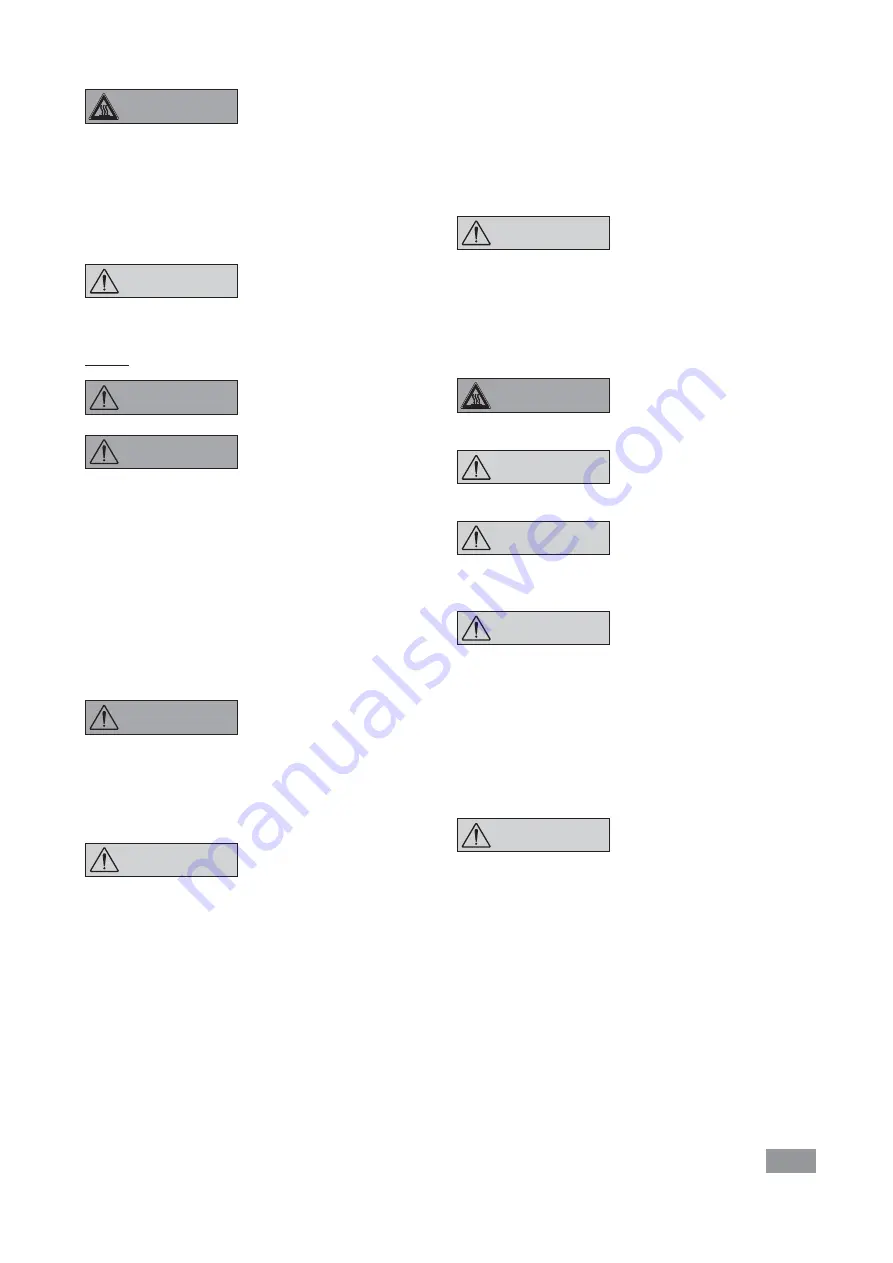
6
• Continuous monitoring of the bath and the filling level of
the bath fluid is required, especially at high temperatures.
• For optimum temperature stability, the fluids viscosity
should be 50 mm
2
/s or less at its lowest operating tem-
perature. This permits good fluid circulation and mini-
mizes heating from the pump.
If water is used at higher tem-
perature, there is heavy loss of
fluid due to the evaporation.
• Untreated tap water is not recommended. It is recom-
mended to use distilled water or high purity water (ion
exchangers) and add 0.1 g soda (sodium carbonate
Na
2
CO
3
) /liter, to reduce corrosive properties.
Risk of burning caused by va-
por or hot water at the outlet
of the cooling coil (accessory).
Do not use the cooling coil with
water at bath temperatures >
95° C.
For bath temperatures > 60°C
make sure that the flow rate
through the cooling coil is high
enough.
Don't use following fluids:
- Untreated tap water
- Acids or bases
- Solutions with halides: chlorides, fluorides, bromides,
iodides or sulfur
- Bleach (Sodium Hypochlorite)
- Solution with chromates or chromium salts
- Glycerine
- Ferrous water.
When changing the bath fluid
from water to a heat transfer
fluid for temperatures above
100 °C, remove the remaining water from the complete
system (including hoses and external devices). When do-
ing this, also open the stopper and union nuts caps of
the pump outputs and inputs and blow compressed air
through all the pump outputs and inputs!
It is dangerous to touch the
heater. The temperature of the
heater can be very high.
• After a power failure during operation, the device may
start automatically (depending on operating mode).
• Transport the device with care.
• Do not transport or empty the bath while it is still hot.
This may result in accidents, especially scalding injuries.
In order to prevent the power
cable from falling into the fluid,
the mains cable must be se-
cured with the cable clamp (
13
, see
Fig. 2
and
Fig. 4
).
Fluids:
Beware of the risk of burning
due to delay in boiling!
Only use fluids, which fulfill the
requirements for safety, health
and device compatibility. Be
aware of the chemical hazards that may be associated
with the bath fluid used. Observe all safety warnings for
the fluids.
• Depending on the bath fluid used and the type of opera-
tion, toxic or flammable vapors can arise. Ensure suit-
able extraction.
• Do not use any fluid which may cause dangerous reac-
tions during processing.
• Only use recommended bath fluid. Only use non-acid
and non corroding fluid.
Only process and heat up any
fluid that has a flash point high-
er than the adjusted safe tem-
perature limit that has been set. The safe temperature
limit must always be set to at least 25 ºC lower than the
flash point of the fluid used. Examine regularly the func-
tion of the safety temperature limiter.
Never operate the device with-
out sufficient heat carrier fluid!
You should also be careful to
ensure that the minimum clearances and immersion
depths in the fluid are observed. Check the fluid level
detection at a regular basis (see section "
Filling and
draining
").
WARNING
NOTICE
WARNING
WARNING
WARNING
NOTICE
NOTICE
WARNING
NOTICE
NOTICE
NOTICE
NOTICE