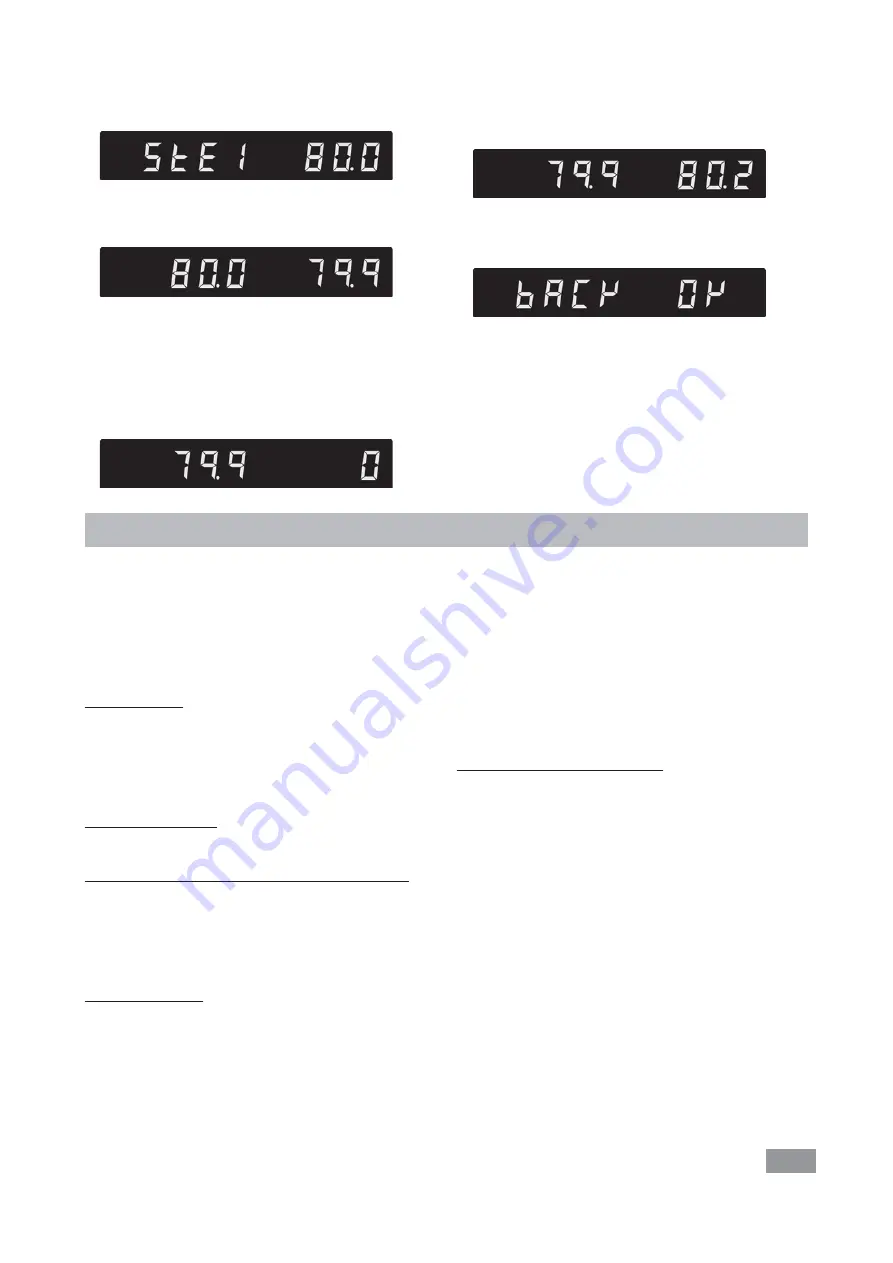
13
Interface and output
The device can be operated in “Remote” mode via the RS 232
interface (
10
) or the USB interface (
11
) connected to a PC
and with the laboratory software Labworld
soft
®
.
Note:
Please comply with the system requirements to-
gether with the operating instructions and help section
included with the software.
USB interface:
The Universal Serial Bus (USB) is a serial bus for connecting
the device to the PC. Equipped with USB devices can be con-
nected to a PC during operation (hot plugging). Connected
devices and their properties are automatically recognized.
The USB interface can also be used to update firmware.
USB device drivers:
First, download the latest driver for
IKA
®
devices with USB
interface from:
http://www.ika.com/ika/lws/download/usb-driver.zip.
Install the driver by running the setup file. Then connect
the
IKA
®
device through the USB data cable to the PC.
The data communication is via a virtual COM port. Con-
figuration, command syntax and commands of the virtual
COM ports are as described in RS 232 interface.
RS 232 interface:
Configuration
- The functions of the interface connections between the
stirrer machine and the automation system are chosen
from the signals specified in EIA standard RS 232 in ac-
cordance with DIN 66 020 Part 1.
- For the electrical characteristics of the interface and the al-
location of signal status, standard RS 232 applies in accor-
dance with DIN 66 259 Part 1.
- Transmission procedure: asynchronous character trans-
mission in start-stop mode.
- Type of transmission: full duplex.
- Character format: character representation in accordance
with data format in DIN 66 022 for start-stop mode. 1
start bit; 7 character bits; 1 parity bit (even); 1 stop bit.
- Transmission speed: 9600 bit/s.
- Data flow control: none
- Access procedure: data transfer from the stirrer machine to
the computer takes place only at the computer’s request.
Command syntax and format:
The following applies to the command set:
- Commands are generally sent from the computer (Master)
to the device (Slave).
- The device sends only at the computer’s request. Even
fault indications cannot be sent spontaneously from the
device to the computer (automation system).
- Commands are transmitted in capital letters.
- Commands and parameters including successive parame-
ters are separated by at least one space (Code: hex 0x20).
- Each individual command (incl. parameters and data)
and each response are terminated with Blank CR LF
(Code: hex 0x20 hex 0x0d hex 0x20 hex 0x0A) and have
a maximum length of 80 characters.
- The decimal separator in a number is a dot (Code: hex
0x2E).
The above details correspond as far as possible to the rec-
ommendations of the NAMUR working party (NAMUR rec-
ommendations for the design of electrical plug connections
for analogue and digital signal transmission on individual
items of laboratory control equipment, rev. 1.1).
Input the calibration value from the reference mesuring
instrument (e.g. 80.2 °C) with the “
Pump
(
+
)“ button
(
H
) or “
Pump
(
-
)“ button (
I
).
Confirm the value by pressing the “
OK/Pump
“ button (
G
).
Back to previous screen for input a new value by press-
ing the “
Temp
“ button (
D
).
Back
OK
The first point calibration is finished now.
Calibration of the other points is performed in the same
way.
The temperature measured by the unit appears on the
left hand side.
Set the first point temperature (e.g. 80 °C). Confirm the
setting by pressing the “
OK/Pump
“ button (
G
).
Left area of the display appears the set value (80 °C) and
the right area of the display appears the actual tempera-
ture value measured. The set LED (
M
) flashes briefly.
The unit now starts and controls to the set value. When
the temperature has reached the set value and has be-
come constant, the “Set” LED (
M
) no longer flashes and
the following display appears.