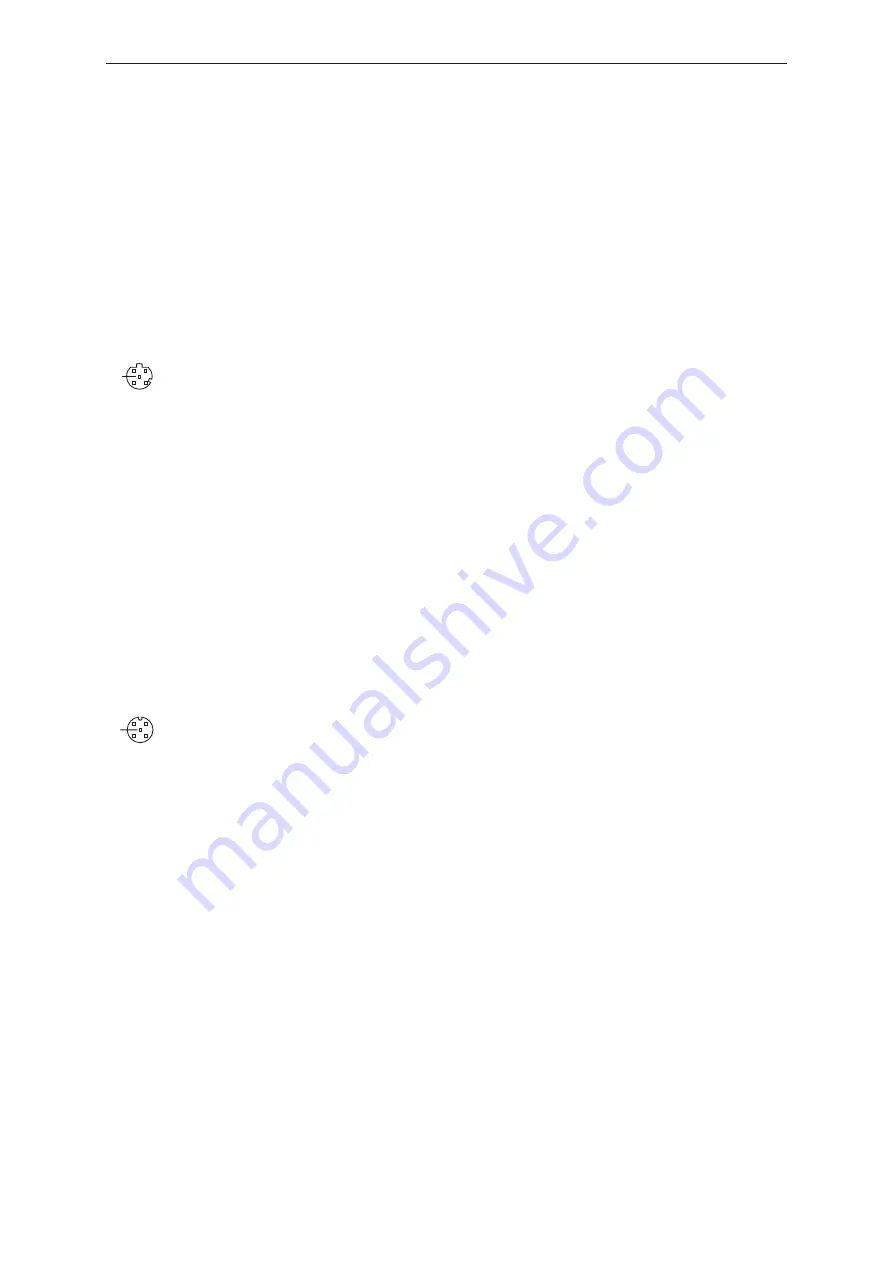
AL4042
Remote I/O module 16 DI
16
6.3 Ethernet
The device is connected to the ModbusTCP network via the Ethernet ports X21 / X22 (e. g.
ModbusTCP control, additional ModbusTCP device). In addition, the device can be connected to an IT
network via the Ethernet ports. The user can access functions of the ifm IoT Core via the IT network
(parameter setting software, IoT Core Visualizer).
u
Connect the device to the ModbusTCP network via a free Ethernet port.
u
Optional: Connect the device to the IT network via a free Ethernet port.
u
For connection, use an M12 connector (with at least protection rating: IP65 / IP66 / IP67).
u
Tighten the cable plug using 1.3 ± 0.1 Nm.
Wiring:
1
2
3
4
5
1: TX +
2: RX +
3: TX -
4: RX -
5: not used
6.4 Process connections
The sensors are connected to the device via the process connections.
The total current supply of the ports X01...X08 is limited to 3.6 A.
The ports feature short-circuit / overload detection.
u
Connect the sensors to ports X01...X08.
u
For connection, use M12 connectors (with at least protection rating: IP65 / IP66 / IP67; max. cable
length: 30 m).
u
Tighten the cable plug using 1.3 ± 0.1 Nm.
Wiring:
3
1
2
4
5
1: sensor supply L+ (US)
2: digital output 2 (DI2)
3: sensor supply L- (US)
4: digital output 1 (DI1)
5: functional earth (FE)
6.5 Voltage supply
The device is connected to the supply voltage US via the power IN port.
The US supply voltage supplies the device and the sensors connected to the ports X01...X08 with
voltage.
Port X31 has overvoltage protection (US).
Port X31 has reverse polarity protection (US).
Port X31 has an inrush current limitation.
u
Disconnect power.
u
Connect the device via port X31 to 24 V DC (20…30 V SELV/PELV).
u
For connection, use an L-coded M12 connector (with at least protection rating: IP65 / IP66 / IP67).
u
Tighten the cable sockets according to the torque specifications indicated by the cable
manufacturer. Maximum permissible tightening torque: 0.8 Nm
u
Observe the derating behaviour of the device
Wiring: