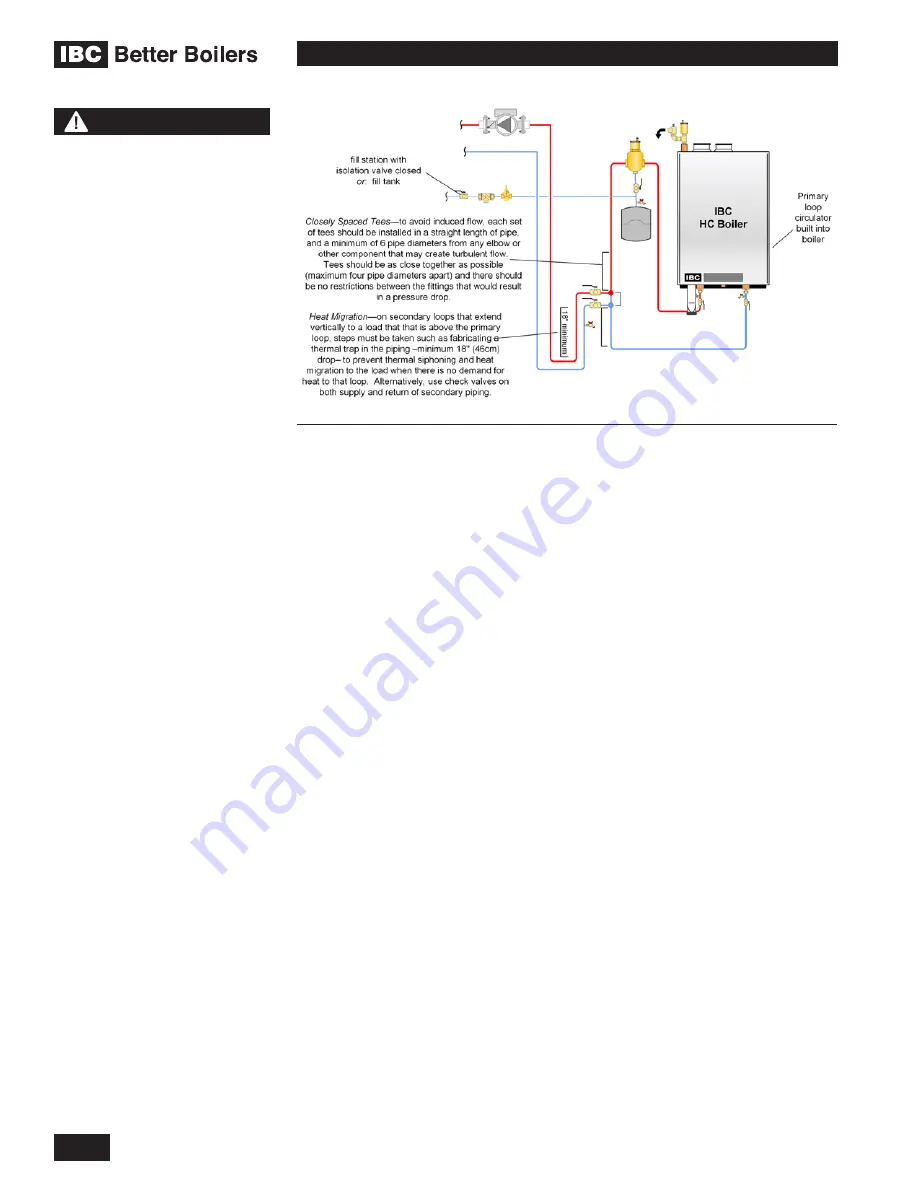
INSTALLATION AND OPERATION INSTRUCTIONS
1-22
HC SERIES BOILERS
HC 13-50, HC 23-84, HC 29-106, HC 33-124, HC 20-125, HC 33-160
We recommend water flow after burner shutdown to utilize legacy heat – this is
significant due to the mass of the heat exchanger. The boiler pump is under the
control of the boiler to allow pump purge after burner shut-down. Default software
values will run the boiler’s pump for 1 minute after the burner shuts down.
Schematics for several piping layouts are provided herein, and additional
drawings are available at
www.ibcboiler.com
. Installers shall conform the piping
design to one of the provided configurations to simplify the control application,
promote good loads and flow management.
Propylene glycol solution is commonly used in a closed loop where freeze
protection is required. Its density is lower than that of water, resulting in
lower thermal performance at a given flow and pressure. As a rule of thumb,
a 50%:50% solution of propylene glycol and water will require an increased
system circulation rate (gpm up 10%), and system head (up 20%) to provide
performance equivalent to straight water.
The HC series modulating boilers offer exceptional matching of heat generation
to radiation. The low minimum firing is better suited to low thermal loads
presented in a typical multi-zoned radiation system. However, where individual
zones in a heating system have loads under 10,000 Btu/hr, the system will still
benefit through use of a buffer tank to ensure a controlled supply temperature,
and to prevent short cycling. Buffering should be added on the secondary piping
of the relevant load, to avoid bulking up the thermal mass of the primary piping
circuit (and potentially lengthen the duration of the transition from hot to cool
loads).
HC modulating series boilers can be connected directly to a floor of non-
oxygen barrier polybutylene material (PB tubing). The internal boiler piping, and
connections are all non-ferrous with the exception of the corrosion resistant
epoxy coated cast iron pump. For maintenance of warranty on such systems,
we require evidence of a thorough flushing of all loops, plus installation of a dirt
separator or side stream filter. A separator/filter maintenance routine shall be
carried out after the retrofit, with filter clearing after the 1st day, 1st week, month
and annually thereafter.
The installer must insure that all external piping
components and pumps are non-ferrous when connecting the boiler to a
system with non-oxygen barrier tubing.
Figure 25: Basic Primary/Secondary piping with closely-spaced tees concept – concept
drawing. This drawing is only a simple schematic guide.
WARNING
Water quality has a significant
impact on the lifetime and
performance of an IBC Boiler
heat exchanger.
Improperly prepared water in
a heating circuit may cause
damage to the heat exchanger
through corrosion or fouling.
Repeated or uncontrolled
water fills will increase the
potential for damage.
High levels of dissolved
solids or minerals may
precipitate out of the fluid
onto the hottest part of the
heat exchanger, impairing
heat transfer and resulting in
overheating and premature
failure. The amount of solids
that may form on the heat
exchanger will depend on
the degree of hardness and
the total water volume in the
system. A high water volume
system with a low hardness
count may cause as much
damage as a system with less
volume and higher hardness,
so it is recommended to treat
water so as to remove all
dissolved solids. Other water
chemistry allowable limits are
as follows:
•
Acidity pH is to be between
6.5 and 8.5
•
Chloride is to be less than
125 mg/l
•
Iron is to be less than 0.3
mg/l
•
Cu less than 0.1 mg/l
•
Conductivity is to be less
than 400μS/cm (at 25°C)
•
Hardness is to be 7 Grains
or less
IMPORTANT: Ensure that
these limits are acceptable
for the other water-side
components in the system.
Содержание HC 33-124
Страница 76: ...SERVICE RECORD DATE LICENSED CONTRACTOR DESCRIPTION OF WORK DONE...
Страница 77: ...NOTES...