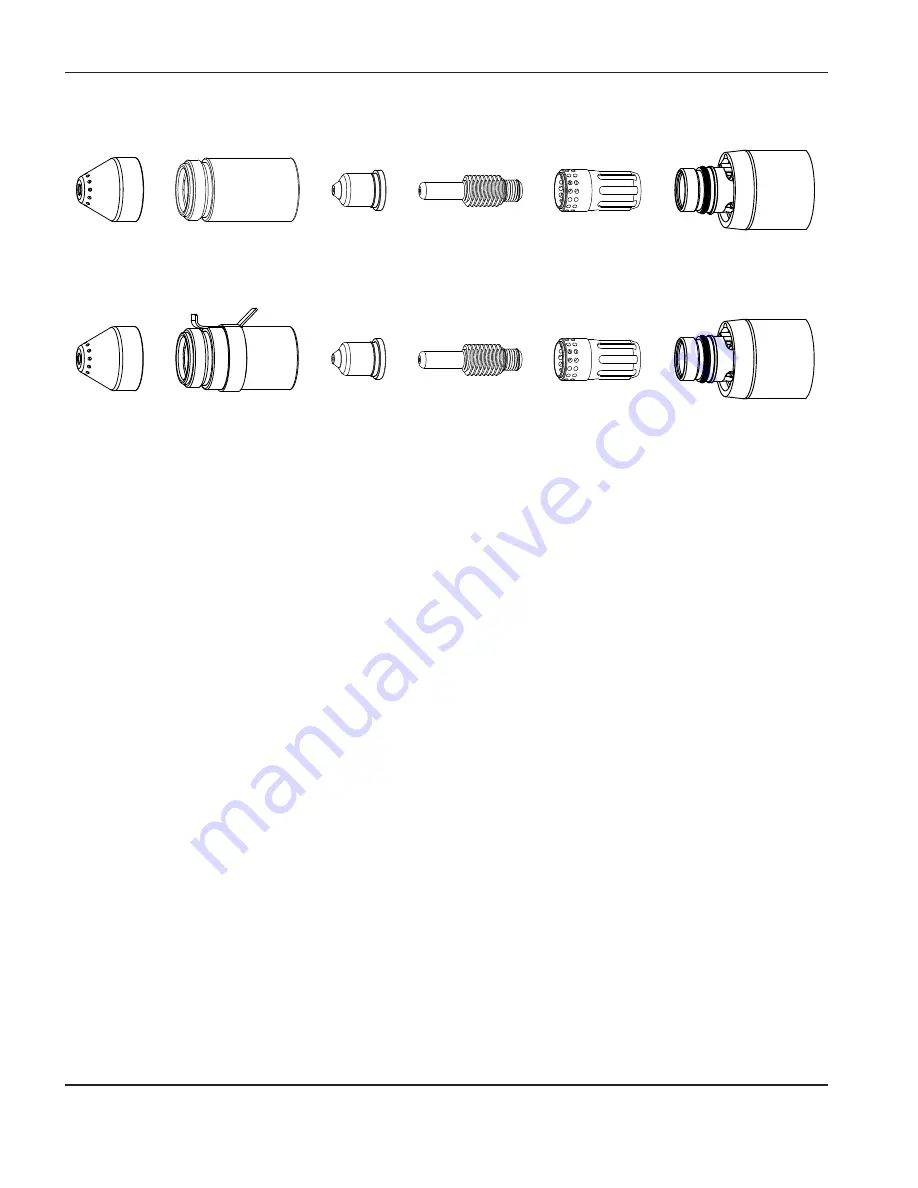
OPeRATION
3-14
Duramax Retrofit Torch
Operator Manual
65 amp mechanized shielded cutting for Powermax1250/1650
220817
Shield
220817
Shield
220854
Retaining cap
220819
Nozzle
220819
Nozzle
220857
Swirl ring
220857
Swirl ring
220842
Electrode
220842
Electrode
220953
Ohmic-sensing
retaining cap
65
A
65
A
• Best Quality Settings (cut speed and voltage) — Settings that provide the starting point
for finding the best cut quality (best angle, least dross, best cut-surface finish). Adjust the
speed for your application and table to obtain the desired result.
• Production Settings (cut speed and voltage) — 80% of the maximum speed ratings. These
speeds result in the greatest number of cut parts, but not necessarily the best possible cut
quality.
Содержание HRT
Страница 1: ...Duramax Retrofit Torch HRT HRTs MRT Operator Manual 807190 Revision 1 ...
Страница 2: ......
Страница 10: ...WARRANTY 9 10 W 4 Compliance Information ...
Страница 16: ...Specifications 1 4 Duramax Retrofit Torch Operator Manual ...
Страница 34: ...Torch setup 2 18 Duramax Retrofit Torch Operator Manual ...
Страница 88: ...OPERATION 3 54 Duramax Retrofit Torch Operator Manual ...