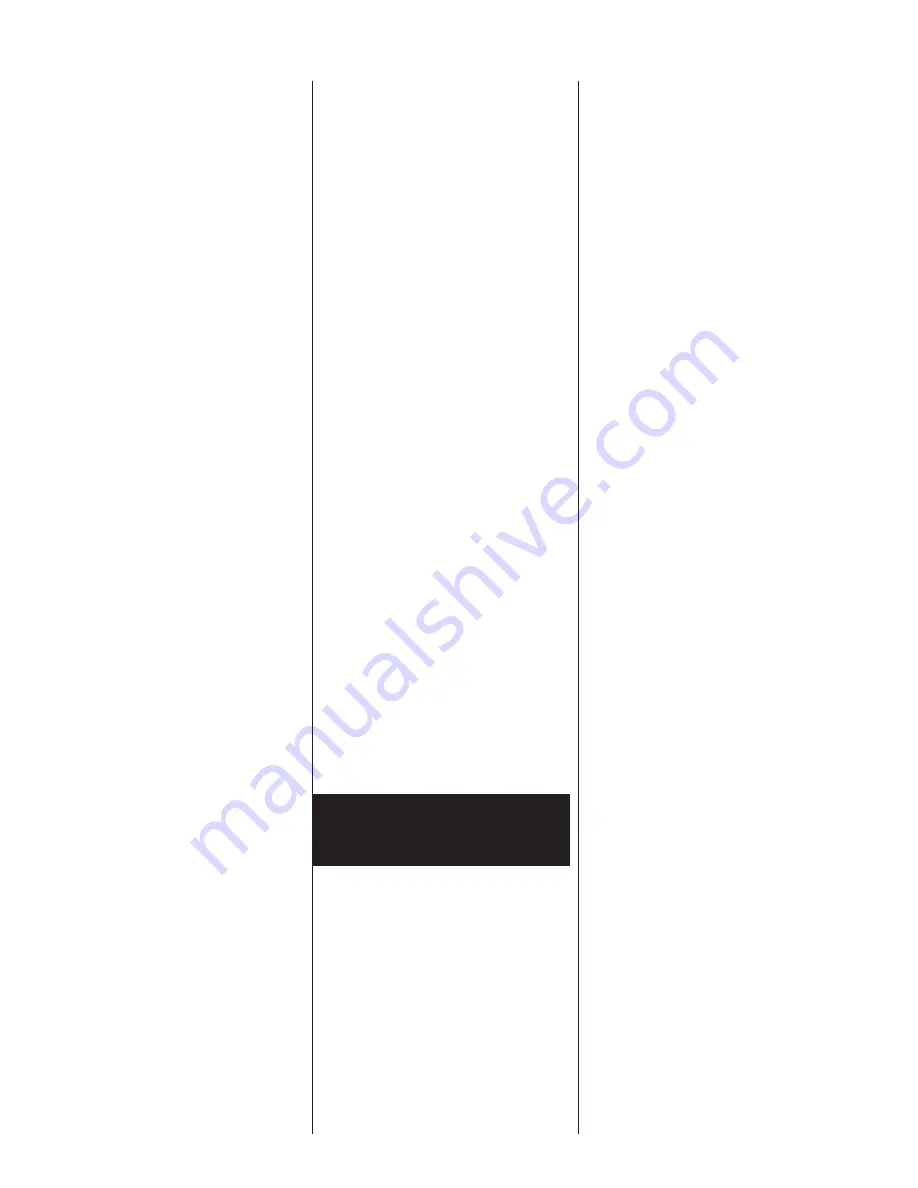
Submerge complete unit under
water and check for leaks.
14.Refill motor chamber with oil.
Use only a high grade
transformer oil or Hydromatic
special submersible oil. Fill
chamber until oil covers top of
windings. Leave air space
in top for expansion. Use
Permatex on plug threads.
Replacing Seals and Bearings:
1. Drain all oil from motor
chamber and seal chamber
as described.
2. Remove motor housing as
described.
3. Remove bolts that hold seal
chamber to pump housing.
Use back-off screws to break
loose.
4. Lift rotating assembly (rotor,
shaft, and impeller) from
pump case and place it
horizontally on bench.
5. Remove impeller by holding
the rotor and removing the
impeller retaining washer and
bolt. The impeller will be
taper fitted to the shaft with a
key. The impeller may need to
be jarred from the shaft by
tapping with a block of wood.
6. A shaft sleeve may be used in
conjunction with the lower
seal and will need to be
removed.
7. Remove lower seal spring
and pry out the seal with a
screwdriver.
8. To remove the seal housing,
take out socket head bolts and
using the bolts in the back-out
holes, pry plate loose. This
will force out lower seal if not
already removed.
9. Remove snap ring that holds
upper seal. Pull seal if it is
free. If not free, it can be
forced off when shaft is
removed.
8
10.Remove 4 bolts that hold
bearing housing in place. Set
assembly in upright position
and bump end of shaft with
hardwood block. This will
push the bearing from the
housing and will force upper
seal from shaft.
11. Use a bearing puller to remove
bearings. Replace with new
bearings. Press only on inner
face of the bearing when
replacing. Pressing on the
outer face can damage the
bearing. Bearings are standard
size that can be obtained from
any bearing supply house or
can be obtained from the
factory.
12.
IMPORTANT:
DO NOT
USE ANY OF THE OLD
SEAL PARTS. REPLACE
WITH ALL NEW SEALS.
13.Thoroughly clean all castings
before replacing seals. Any
dirt between the seal faces can
cause failure.
14.Examine all O-rings for nicks
before using and replace
damaged O-rings with new
ones.
15.Use Loctite on socket head
impeller locking screw in end
of shaft.
Below is a list of common
problems and the probable causes:
Pump will not start.
1. No power to the motor. Check
for blown fuse or open circuit.
2. Selector switch may be in the
Off position.
3. Control circuit transformer
fuse may be blown.
4. Overload heater on starter may
be tripped. Push to reset.
Pump will not start and
overload heaters trip.
1. Turn off power and check
motor leads with Megger or
ohmmeter for possible ground.
2. Check resistance of motor
windings. All 3 phases should
show the same reading.
3. If no grounds exist and the
motor windings check OK,
remove discharge elbow cover
and check for clogged or
blocked impeller.
Pump operates with selector
switch in Hand position but will
not operate in Auto position.
1. This indicates trouble in the
float level control or alternator
relay.
2. Check control panel for
trouble.
Pump runs but will not shut off.
1. Pump may be air locked. Turn
pump off and let set for several
minutes, then restart.
2. Lower float control may be
hung up in the closed position.
Check in wet well to be sure
the control is free.
3. Selector switch may be in the
Hand position.
Pump does not deliver proper
capacity.
1. Discharge gate valve may be
partially closed or partially
clogged.
Pump
Troubleshooting
Содержание DRY PIT
Страница 11: ......