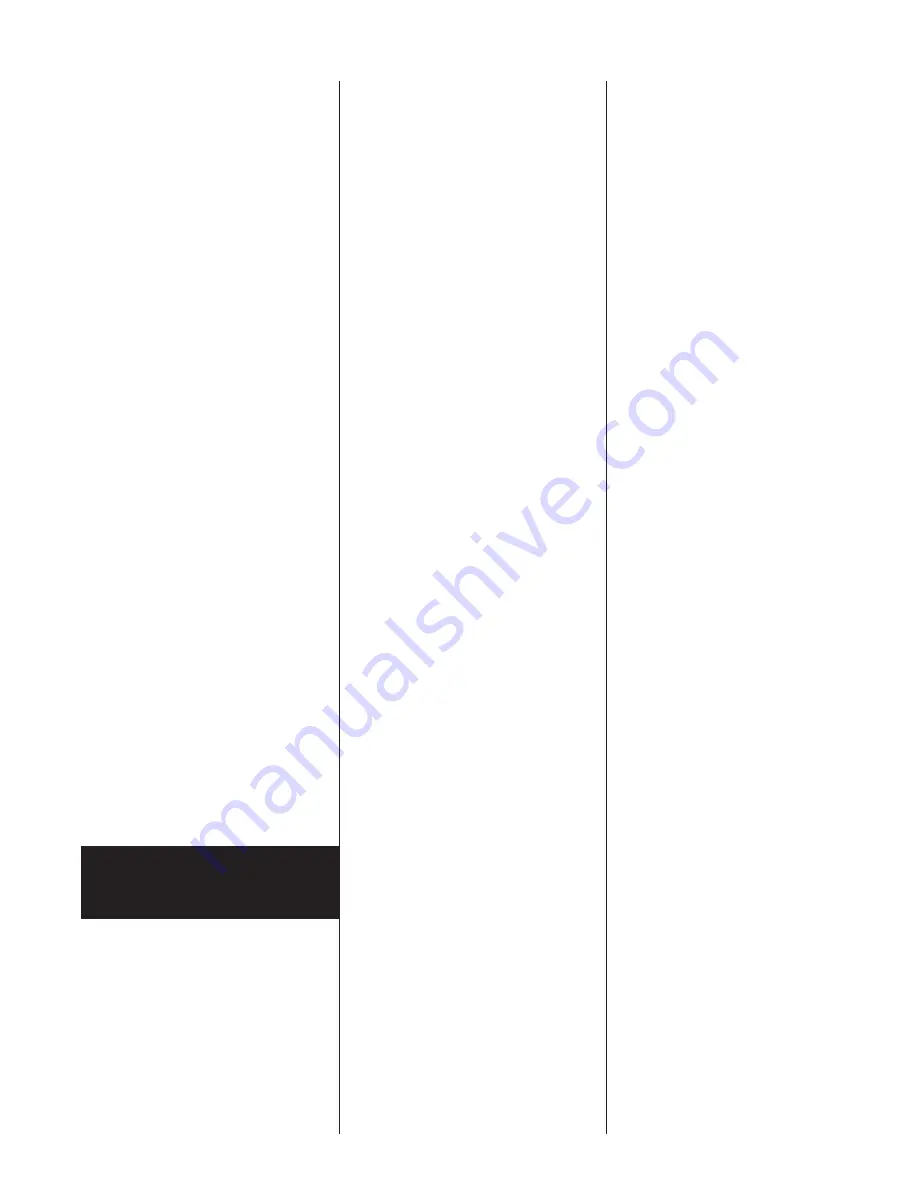
3
heaters and connections for heat
sensor wires are furnished.
IMPORTANT: If Hydromatic
electrical controls are not used
and the motor fails because of
improper components or if the
heat sensors are not properly
connected, the motor guarantee
is void.
Hydromatic electrical equipment
is installed in a weatherproof
NEMA 3R enclosure. The
electrical equipment includes a
main circuit breaker for each
pump, a magnetic starter with
overload protection for each
pump, an H-O-A switch and a run
light for each pump, an electrical
alternator and a transformer to
provide appropriate control for
control circuit and alarms.
Overload Heaters:
Starters with 3 leg overload
protection must be supplied if the
Hydromatic electrical panel is not
used. The heaters must be sized in
accordance with the nameplate
amps on the motor. The amp
draw on these oil-filled motors
is
slightly
higher
than
a corresponding horsepower
surface motor, so heaters must be
sized by the nameplate rating.
Installation
Instructions
Installing Pump in Dry Pit:
Before installing pump in the dry
pit, lay it on side and turn the
impeller manually. The impeller
may be slightly stuck due to
factory water testing, so it must be
broken loose with a small bar or
screwdriver in the edge of the
vanes. The impeller must turn
freely.
Clean all trash and debris from
pump installation area and
connect pump to plumbing.
A check valve must be installed
on each pump. A gate or plug
valve in each pump discharge line
is also recommended. This valve
should be installed on the
discharge side of the check valve
so the line pressure can be cut off
to service the check valve. Single
pump systems are sometimes
installed without a check valve
where it is desirable to self drain
the discharge line to prevent
freezing. This can be done only
with short discharge lines.
Otherwise water will return to the
sump and cause short cycling of
the pump.
Mounting Pump Stand:
The pump will ship from the
factory on a dry pit pump stand.
The suction and discharge of the
pump will be oriented at the
factory per the prescribed
customer order.
The dry pit pump must be
anchored to the pump station
floor. This must be done to
alleviate stress on the suction and
discharge piping while the pump
is in service. When securing the
pump stand to the contractor
supplied anchor bolts, it may be
necessary to shim the stand to
ensure the suction and discharge
piping properly aligns.
Plumbing (General):
The site contractor must supply
the use of necessary pipe hangers
or other piping supports. Both the
suction and discharge piping must
be independently supported and
properly aligned to ensure no
strain is transmitted to the pump
when connections are tightened.
The use of expansion joints or
vibration pads does not preclude
the need to properly support the
piping.
NOTE: Do not support the
piping by the pump. Do not
force piping when making
connections.
Suction-Inlet Piping:
The correct sizing and installation
of the suction plumbing is
particularly
important.
The
suction piping must be selected
and installed in such a manner that
it minimizes pressure losses and
allows for sufficient flow during
starting and operation. Most
NPSH problems can be traced
directly to improper design of
suction piping systems.
It is recommended that the piping
be as direct as possible and the
length should be at least 10 times
the diameter of the pipe. When a
pipe diameter larger than the
suction of the pump is used, an
eccentric reducer should be used
with the eccentric side down.
This will allow for the elimination
of a potential air pocket in the
suction plumbing.
NOTE: A pipe diameter smaller
than the suction of the pump
must never be used.
It is also recommended that a
valve be installed in the suction
piping to isolate the pump during
routine
maintenance
and
shutdown. A globe valve should
not be used when NPSH is
critical.
It is recommended that a
compound pressure gauge be
installed in the suction piping to
assist in troubleshooting potential
performance problems.
Содержание DRY PIT
Страница 11: ......