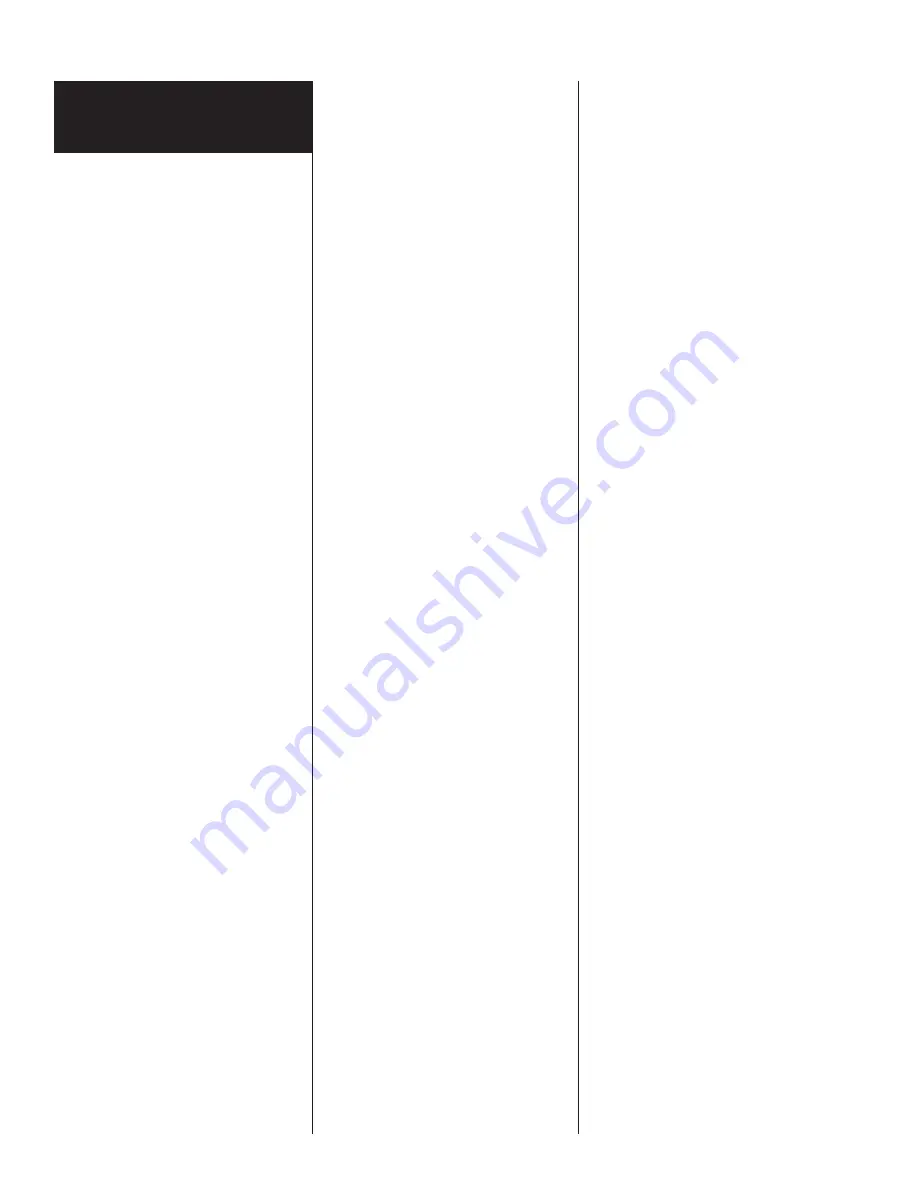
2
Shipping:
When unpacking unit, check for
concealed damage. CLAIM FOR
DAMAGE MUST BE MADE
AT THE RECEIVING END
THROUGH THE DELIVERING
CARRIER. DAMAGE CANNOT
BE PROCESSED FROM THE
FACTORY.
Pumps Not Operating or in
Storage:
Pumps with carbon ceramic seals
must have impellers manually
rotated (6 revolutions) after setting
nonoperational for 3 months or
longer and prior to electrical
start-up.
Pumps with carbide seals must
have impellers manually rotated
(6 revolutions) after setting
nonoperational for 3 weeks or
longer and prior to electrical
start-up.
Seal Failure:
An electrode is installed in the seal
chamber so if water enters the
chamber through the first seal, the
electrode will be energized and
a signal will be transmitted to
the sensing unit at ground surface,
causing an alarm activation. The
electrode probe is installed in all
units, but the sensing unit is
supplied at an extra cost and must
be ordered.
In operation the seal failure unit
indicates only that there is some
water in the seal chamber. The
pump will continue to operate
without damage, but the seal
should be checked immediately
after failure is indicated.
General
Information
The sensing unit is recommended
on all installations as good
insurance against motor failure.
Pump:
The dry pit submersible pump is
supplied for 1 or 3 phase and for
200, 230, 460 or 575 volts. Pump
is supplied with 30 feet of power
cord and/or 30 feet of auxiliary
control cord. Longer cable lengths
can be furnished but must be
specified at time of order. Be sure
green wire is connected to a good
ground such as water pipe or
ground stake. The auxiliary cable
for the seal failure and heat
sensors is also 4 wire and color
coded.
Heat Sensors:
All motors have heat sensor units
embedded in the motor winding
to detect excessive heat. The heat
sensors are set to trip at 120ºC.
The sensors automatically reset
when the motor cools to safe
temperature.
The sensors are connected in
series with the motor starter coil
so that the starter is tripped if heat
sensor opens. The motor starter is
equipped with overload heaters so
all normal overloads are protected
by the starter.
IMPORTANT: If Hydromatic
®
electrical starting equipment is
not supplied, the heat sensor
circuit must be connected in
series with the starter coil or
warranty on the motor is void.
Connection diagram is included
in the manual.
Wet Well Level Control:
Sump level is controlled by
Hydromatic switch controls. The
float is held in position in the
sump by a weight attached to the
power cord above the float. The
cord supports the float and is
adjusted for height from the
surface.
Duplex
systems
use
three
controls: one set at turn-off, one
set at turn-on for one pump, and
one set at turn-on for both pumps.
Pumps then alternate lead and
lag on each successive cycle. Two
pumps operate together only
when the sump level rises to the
third
or
override
control.
The override control also brings
on the second pump in case of
failure of the first pump. Extra
floats with appropriate controls
can be supplied for alarm
functions. Triplex systems use
four controls: One set at turn-off,
one set at turn-on for one pump,
one set at turn-on for two pumps,
and one set at turn-on for three
pumps. The pumps alternate with
each successive cycle.
Three pumps operate together
only if the sump level rises to the
fourth control (second override).
This control also brings on the
third pump in case of failure of
either or both of the first two
pumps.
Alarm Controls:
The alarm level is usually set
above the override level so the
alarm will signal only if the
override level is exceeded.
However, some engineers prefer
to have the alarm level set below
the override level as it is possible
for one pump to fail and the other
pump to operate on the override
level with the sump level never
reaching the alarm level. This is
particularly true in cases of low
inflow capacity.
Electrical Control Panel:
It is recommended that the
Hydromatic control panel be used
with all pumps as proper starter
Содержание DRY PIT
Страница 11: ......