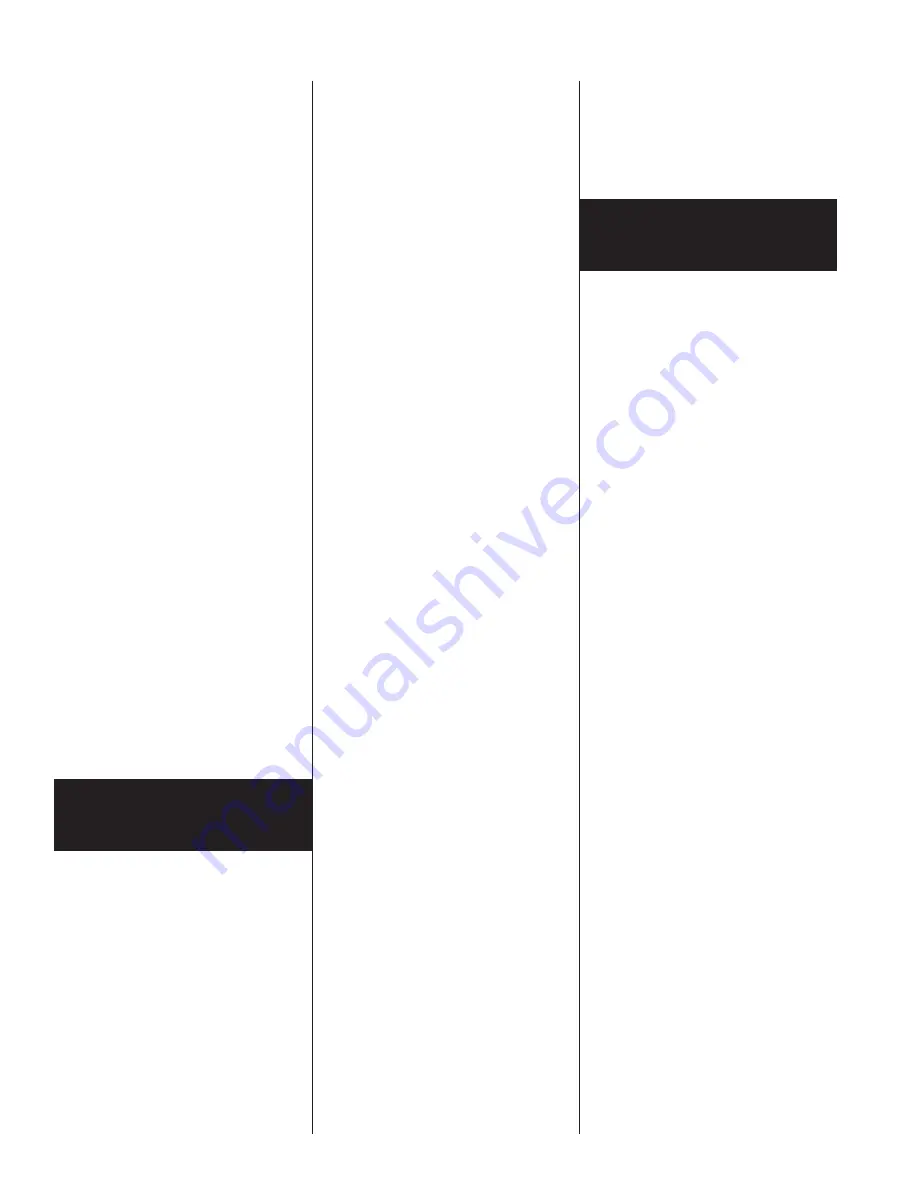
NOTE: The cooling fins must
be intact to ensure the pump
operates within the factory
specified temperature.
Water Jacket (Optional):
When additional cooling is
necessary, a water jacket is
supplied from the factory. All
necessary plumbing of the water
jacket is supplied from the factory
connecting to the suction and the
discharge piping. The plumbing
includes ball valves allowing for
removal of the water jacket for
periodic cleaning without shutting
the system down.
The water jacket is held in place
by clamps and is sealed both top
and bottom by O-rings. Upon
removal of the water jacket for
cleaning, care should be taken not
to damage the O-rings and replace
if necessary.
NOTE: Clean fresh water
supplied to the water jacket will
reduce the necessity of frequent
periodic cleaning of the water
jacket. This does not preclude
that the water jacket should not
periodically be cleaned.
Starting System:
1. Turn H-O-A switch to Off
position and then turn on main
circuit breakers.
2. Open all discharge valves and
allow water to rise in wet well.
3. Turn H-O-A switch to Hand
position on one pump and
notice operation. If pump is
noisy and vibrates, rotation is
wrong. To change rotation,
interchange any two line leads
6
to a three phase motor only.
DO NOT INTERCHANGE
MAIN INCOMING LINES. If
duplex system, check second
pump in the same manner.
4. Now set H-O-A switch to Auto
position and allow water to
rise in the wet well until the
pump starts. Allow pump to
operate until the level drops
to turn-off point.
5. Allow wet well level to rise to
start the other pump. Notice
run lights on the panel. Pumps
should alternate on each
successive cycle of operation.
6. Turn both H-O-A switches to
Off position and allow wet
well to fill to the override
control level.
7. Turn both switches to Auto
position and both pumps
should start and operate
together until level drops to
turn-off point.
8. Repeat this operation cycle
several times before leaving
job site.
9. Check voltage when pumps
are operating and check amp
draw of each pump. Check
amps on each wire, as
sometimes a high leg will
exist. One leg can be
somewhat higher (5 to 10%)
without causing trouble. For
excessive amp draw on one
leg, the power company
should be consulted.
Phase Converters:
Phase converters are generally not
recommended, but in cases where
only single phase current is
available, phase converters can be
used. Be sure to size the phase
converter large enough for the
amp draw specified on the motor
nameplate, not necessarily by
motor horsepower. The warranty
of all three phase submersible
motors is void if operated with
single phase power through a
phase converter and 3 leg ambient
compensated extra-quick trip
overload protectors are not used.
Lubrication or other maintenance
is not required, as the motors are
oil filled.
If a seal failure unit is used, no
attention is necessary as long as
the seal shows satisfactory
operation.
If seal failure is not used, the
pump should have the oil drained
from the seal chamber once every
two years and inspected for water.
Generally, these pumps give very
reliable service, and can be
expected to operate for many
years without failure under
normal operating conditions.
Lightning:
In some areas where considerable
lightning occurs, we recommend
that a lightning arrestor be
installed at the control panel.
Lightning arrestors are good
insurance against damage to an
expensive motor.
Servicing Instructions:
IMPORTANT: Read all
instructions prior to replacing
any parts.
WARNING: Before handling
these pumps and controls,
always isolate and disconnect
power first.
Do not smoke or use any
sparkable electrical devices or
Pump
Operation
Pump
Maintenance
Содержание DRY PIT
Страница 11: ......