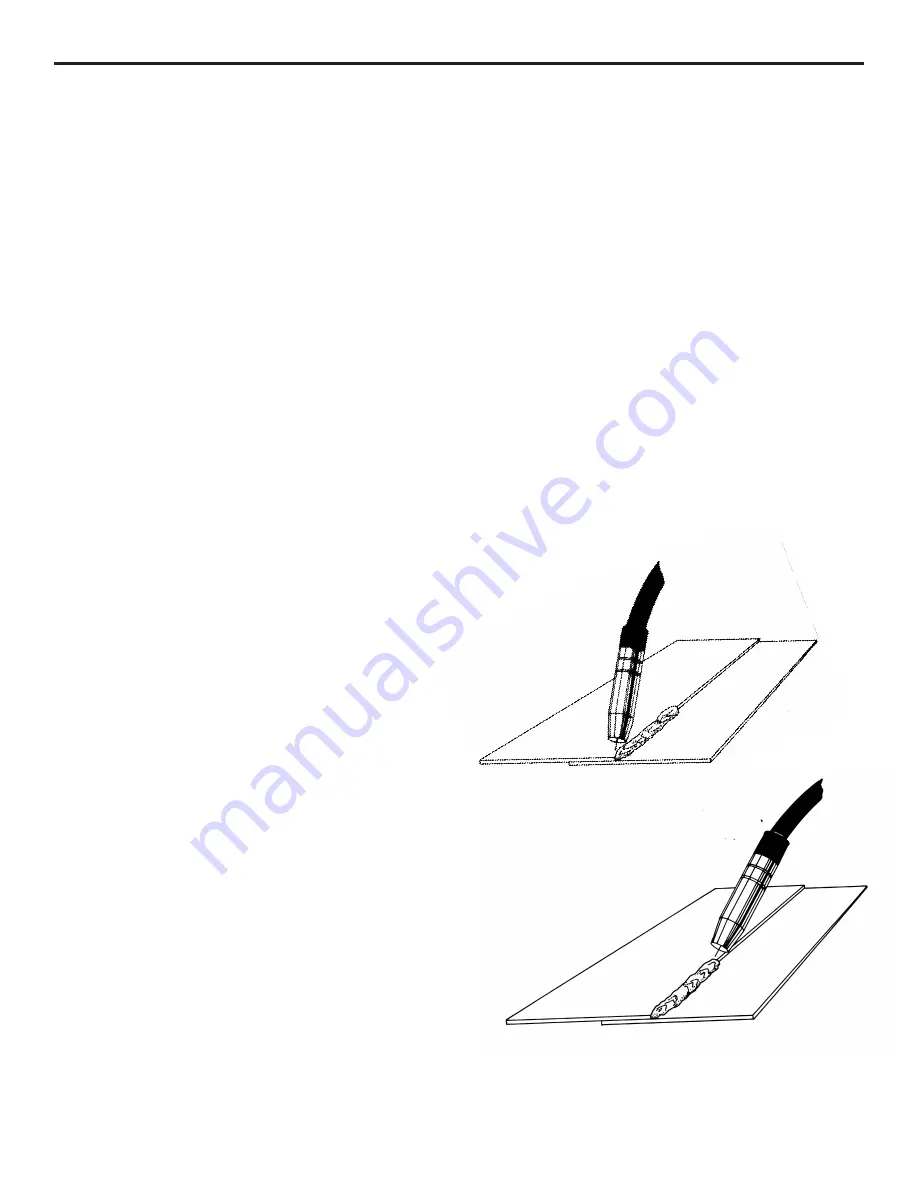
9
Figure 5 “Pulling the Weld”
Figure 4 “Pushing the Weld”
When tuning in your welding machine, it is best to start with
the wire feed rate too high. On the highest power setting,
you may actually want to start with the wire feed rate set at
maximum. Gradually decrease the wire feed rate until the
steady frying noise is heard. A common problem many people
have when trying to tun the wire feed rate is that they turn the
knob too rapidly. Many people never turn the wire feed rate
down low enough and then start to increase it again. If the
wire feed rate is slowly decreased, then eventually you will
cross the point where the machine will be tuned in. It is a
good idea to practice tuning in the welding machine. Power
setting #2, 3 is an ideal heat setting for this, as it has a nice,
crisp sizzle. Once you have mastered tuning in the machine
on power setting #2, 3, practice tuning in the machine on
different heat settings.
It is highly recommended that you practice with your welder
at different power settings so that you will become familiar
with your welder. This is important to do prior to welding on
a project so that you will know which heat setting to select for
the job.
Seam Welding
Install the conical nozzle (Part #S4328) on the welding gun.
The conical nozzle is used because it is much easier to see
the welding process due to the taper in the nozzle. Have 1/4"
to 1/2" of welding wire protruding from the end of the gas
nozzle.
Prior to running a seam weld, it is recommended that tack
welds be placed every 2 to 3 inches along the seam, even
closer for extremely thin panels. Tack welds will help to hold
the panel in place while welding, as well as to prevent panel
separation caused by warpage.
Hold the welding gun at a 45-degree angle and use the edge
of the gas nozzle to hold the two panels together, aim the
welding wire at the spot to be tacked. Momentarily press
the trigger (approximately 1 second) and tack the two panels
together. Do not lift up the welding gun until the weld has set.
Tack welding is done at the same power setting at which seam
welding is done. (1 or 2 on the course setting for sheet metal,
3 or 4 for heavier material.)
When you have the panel tacked into place, you are ready to
seam weld. Once again, have 1/4" to 1/2" of welding wire
protruding from the gas nozzle. The welding gun is generally
held at a 45-degree angle to the work piece. It may also be
tilted at a 45-degree angle to the side. Rest the gun nozzle on
the work piece and have the wire pointing at the spot where the
welding is to begin. Press the trigger and begin welding. It is
important that you can see the welding wire coming out of the
gas nozzle and the small halo formed at the end of the welding
wire where it is melting. This halo will provide the light
necessary to see through your helmet while welding.
The direction in which the welder travels will affect the
characteristics of the weld. When "pushing the weld" the
welding gun is tilted away from the direction of travel (see fig.
4). When "pulling the weld" the welding gun is tilted toward
the direction of travel (see fig. 5).
As you gain expertise with your welder, you will find that
is possible to reduce warpage when welding sheet metal by
welding at a higher power setting and moving faster along
the seam. In this way, you are reducing the amount of time
welding, therefore reducing the amount of heat which is put
into the panel.
Содержание MIG 2400
Страница 21: ...21 HTP MIG 2400 Wiring Diagram...
Страница 22: ...22 Parts List MIG 2400...