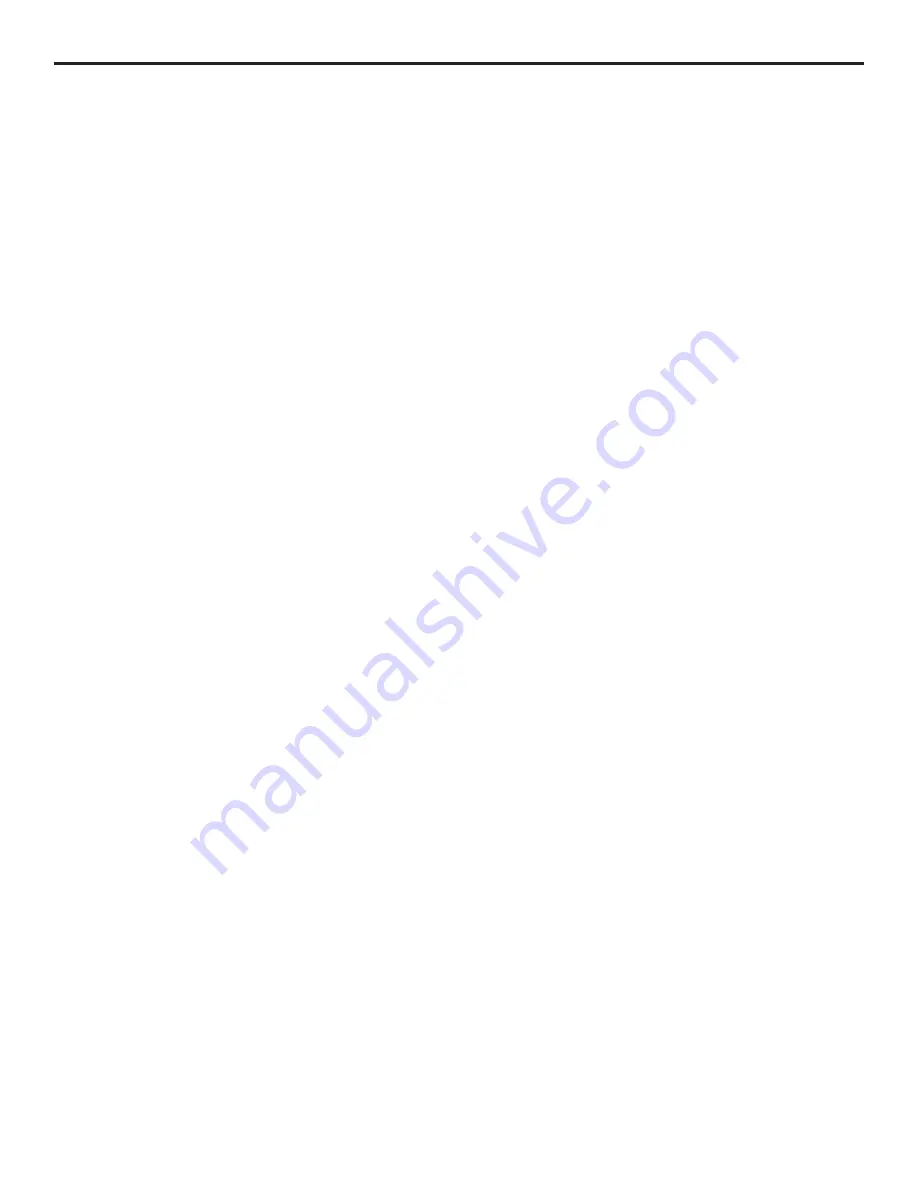
10. Course Power Switch
– This switch controls the welding
current and has 4 settings. The higher the number, the
higher the welding current. Each setting increases the
amperage between 20 and 100 amps, depending on
the wire diameter and the setting you are moving between.
For example, welding with .023" wire, going from coarse
setting 1 to coarse setting 2 will increase the amperage
by 20 amps. When welding with .035" wire, going from
coarse setting 3 to coarse setting 4 will increase the
amperage by 100 amps.
WARNING: DO NOT CHANGE SWITCH POSITION WHILE
WELDING. THIS WILL CAUSE THE CONTACTS TO ARC
DAMAGING THE SWITCH.
11. Fine Power Switch
– the Fine Power switch has 6
positions. 1 is the lowest while 6 is the highest. This
means the 2400 has 6 different heat setting inside of each
of the 4 coarse heat settings on the coarse power switch
(#10) for a total of 24 heat settings. For example if the
power switch is set to 2, then the lowest heat setting for
heat 2 would be set to Fine Power switch 1. Let’s call
this setting 2,1. The next setting would be to set the fine
power switch to position 2, or 2,2. Then it would be 2,3,
2,4, 2,5, and finally 2,6. If you still want a higher power
setting, you would increase your power switch to 3, an
then turn the fine power switch down to position 1 for a
setting 3,1.
12/13. Power Output Receptacles
– 12 is the positive
power output receptacle and 13 is the negative power
output receptacle. These control the polarity of the
machine. For most welding applications, the ground
cable will be connected to the negative receptacle (#12)
and the welding gun lead (#14) will be connected to
the positive receptacle (#13).
When using flux cored wire the polarity should be
reversed. The ground cable would then be connected to
the positive receptacle and welding fund lead would be
connected to the negative receptacle.
If you have having burn-through problems when welding
on extremely thin material with a solid wire and shielding
gas, you may want to reverse the polarity as this will reduce
the penetration and make it easier for you to weld thin
material.
When inserting the end of the ground cable into either
power output receptacle, secure the ground cable by
twisting it clockwise _ turn. It is important that the ground
clamp be connected to a good, clean, surface. Failure to do
so will cause poor quality welds. Place the ground clamp as
close as possible to the area to be welded.
14. Welding Gun Lead
– The welding gun lead takes the
power from either power output receptacle and runs
it to the welding fun. Secure it by twisting it clockwise
1/2 turn. For general welding, the welding gun lead will be
connected to the positive power output receptacle.
Controls in the Wire Feed Compartment
1. Burnback Time
– As soon as you release the trigger
on the welding gun, the wire feed motor stops turning
immediately. The Burnback Time is the amount of time
your welder is still applying welding current to the welding
wire after the wire feed motor has stopped feeding the
welding wire. If the current stopped at the same time the
motor wire stopped turning, then there is a chance the
welding wire would “freeze” in the molten welding puddle
as it solidified. If there is too much Burnback Time, then
the wire would melt to the contact tip.
Turning the Burnback Time knob counter clockwise
shortens the amount of time welding current is applied
to the wire, LENGTHENING the amount of wire sticking
out past the contact tip. Turning the burnback time knob
clockwise increases the amount of time welding current
is applied to the wire, SHORTENING the amount of wire
sticking out past the contact tip.
Higher amperages and aluminum wire require a shorter
burnback time. To set the burnback time, a good starting
point is to rotate the burnback time knob approximately
25% in the clockwise direction. The burnback is set
correctly when the welding wire does not stick to the
workpiece and does not melt to the contact tip.
2. Wire Feed Accelerator – The wire feed accelerator has
3 positions, normal, medium, and slow. This controls
how fast the wire drive motor accelerates to the speed you
have the wire feed rate set to. The Mig 2400 has this feature
since it can handle large diameter wires fed at high speeds
and at high welding amperages.
For example, when using a .035" or .045" diameter steel
wire with the machine set at 240 amps, you would want
the wire to begin to feed slowly into the work piece and
then gradually accelerate to speed. This provides more
consistent arc starting with less hesitation.
Using a .023" diameter with the machine set at 60
amps, the normal acceleration setting would be used.
Adjust the wire feed accelerator to suit your personal
welding preference.
6
Содержание MIG 2400
Страница 21: ...21 HTP MIG 2400 Wiring Diagram...
Страница 22: ...22 Parts List MIG 2400...