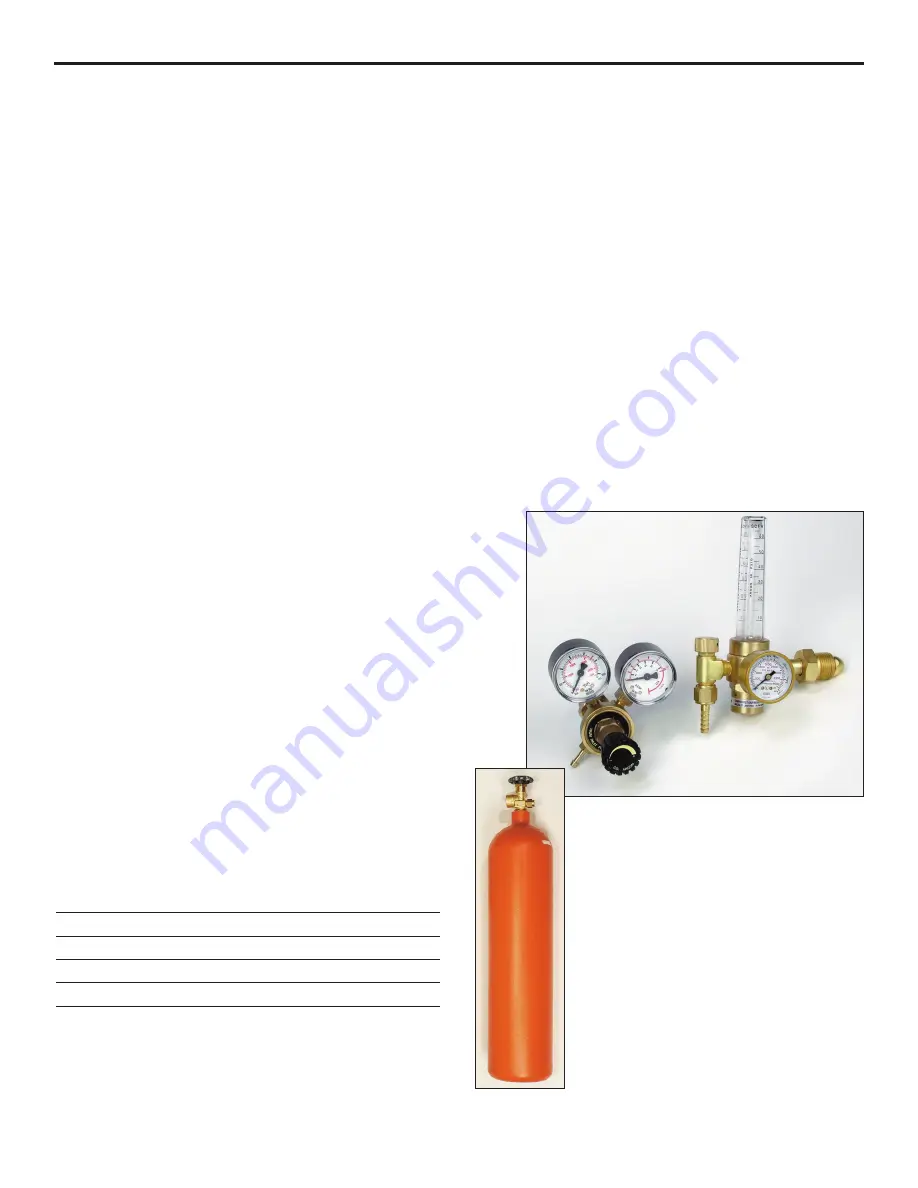
18
Monthly Maintenance
Your HTP MIG Welder is a very hardworking piece of
equipment and is very simple to maintain. However, your
HTP MIG Welder is more complicated than other types of
welding equipment. It is very important that these simple
maintenance procedures be followed to keep your welder
operating trouble free.
1. Wire Drive System
– The guide tube and inlet wire guide
should be check periodically to ensure that they are in correct
alignment with the drive rolls. Misalignment will result in
the copper plating of the wire being rubbed off. This copper
dust will be carried into the liner resulting in increased friction
causing wire feed problems.
2. Welding Cable
– You should not allow heavy equipment to
run over the welding cable. Avoid pulling the machine by the
cable.
Do not pull the welding cable over sharp edges.
3. Transformer and Internal Components
– Your MIG
2400 is equipped with a thermoswitch to protect the internal
components of the machine should the duty cycle be
exceeded. The thermoswitch is placed in the low voltage
circuit, so that when the duty cycle is exceeded, the main
relay will not operate, preventing power from going to the
main transformer, and the wire feed motor will not turn. The
indicator light will remain on, and the cooling fans will remain
on. The thermo indicator lamp will light up yellow, indicating
the duty cycle has been exceeded. When the machine cools
down (approximately 20 minutes) the thermoswitch will
automatically reset, the thermoswitch light will go out, and the
machine will be ready for use.
To keep the cooling system of your welder operating at peak
performance, it is necessary to remove the side panel and blow
this area out with dry, compressed air. This will remove dirt
and dust from the internal components.
Sheild Gas
Since no flux is used for solid wire MIG welding, the proper
shield gas must be used. Different materials require different
shield gases. Use the chart below for a guide.
Material
Shield Gas
Flow Rate
Steel
75% Argon - 25% CO2
10 – 25 cfh
Aluminum
100% Argon
25 – 50 cfh
Stainless Steel
90% 7.5% Argon – 2.5% CO2
15 – 35 cfh
Brazing
100% Argon
15 – 35 cfh
Cast Iron
75% Argon - 25% CO2
25 – 35 cfh
Use a gas regulator such as HTP Part #12020 or a flowmeter
such as HTP Part # 12020F which is compatible with both
Argon and C-25 gas cylinders and has a barbed fitting for the
delivery hose. Connect the gas hose to the brass fitting at the
rear of the machine and to the barbed fitting on the regulator.
HTP also has available small 60 cubic foot gas bottles (Part
#99900), which are ideal for use with your welder. These
bottles stand approximately 30" high and weigh less than 40
pounds, making your welder very easy to move around the
shop. Be sure to check with your local gas supplier about
filling these tanks before ordering.
If you already have a large cylinder, you can fill the small
cylinder from the large cylinder using the transfer manifold
(HTP Part #99905).
NOTE: 75% Argon – 25% CO2 may be used for stainless steel
welding. Stainless steel can also be welded with steel wire and
75% Argon – 25% CO2 gas, however, these welds will not be as
corrosion resistant as welds made with stainless steel wire.
12020
Gas
Bottle
Содержание MIG 2400
Страница 21: ...21 HTP MIG 2400 Wiring Diagram...
Страница 22: ...22 Parts List MIG 2400...