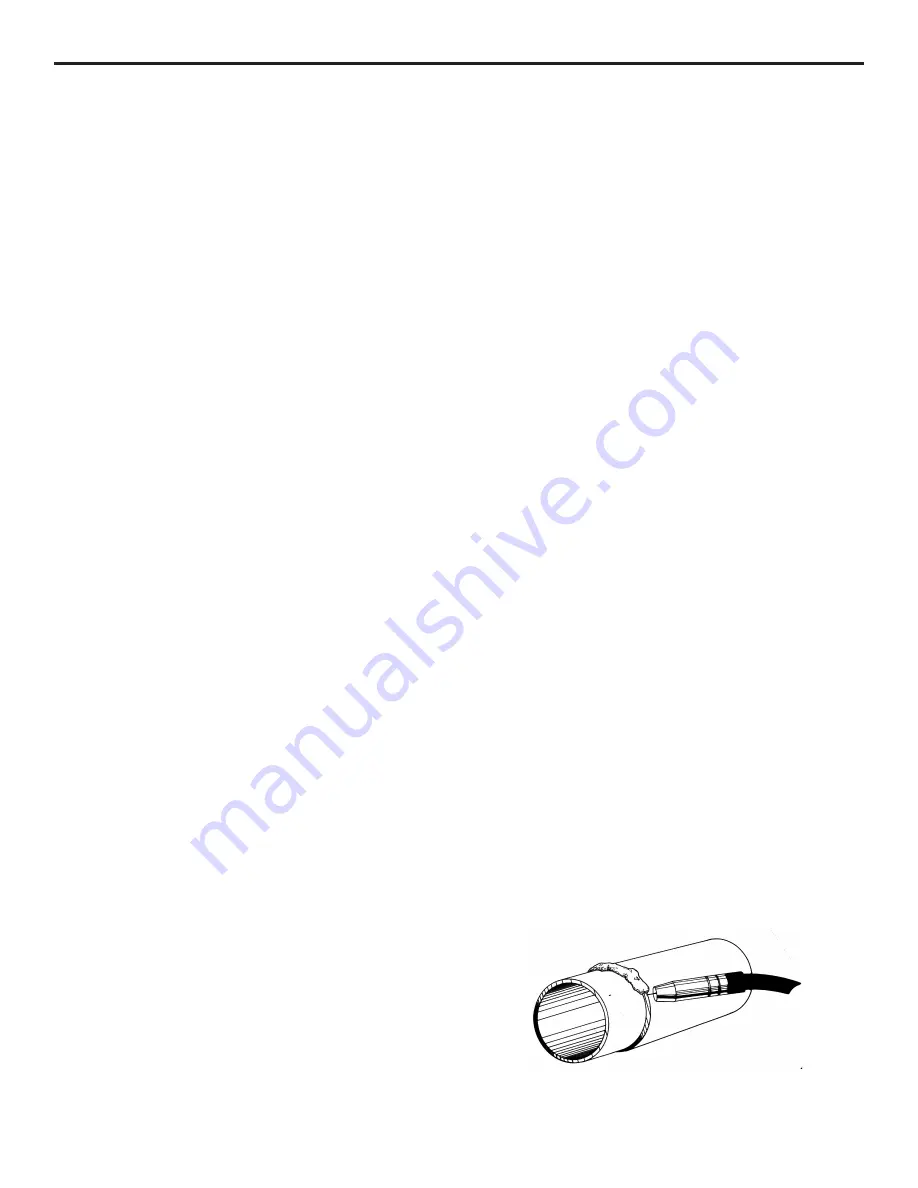
Shield Gas
– The shield gas required for welding aluminum
is 100% Argon. Due to the rate at which aluminum oxidizes,
the flow rate of the Argon gas must be increased to 25 cubic
feet per hour (cfh) or more. The cylindrical gas nozzle (Part
#S4330) is recommended for use on the standard welding
gun when welding aluminum. The larger opening area of
the nozzle will result in a wider dispersion of the shield gas,
insuring adequate gas coverage of the weldment.
Liner
– a Teflon liner (part #15041) is the preferred liner for
welding aluminum. To change the liner, see “Testing and
Changing the Liner”.
Welding Wire
– To weld aluminum, aluminum welding wire
must be used. HTP has aluminum wire available in two
diameters; Part #40230 - .030" diameter and Part #40235
- .035" diameter. The .030" wire is recommended for thin
gauge to 1/8" material, while the .035" is recommended for
.060" material and thicker. For installation of the aluminum
wire, see “Feeding the Wire.”
Cleanliness
– aluminum is very sensitive to impurities.
Therefore, it is extremely important that the surfaces to be
welded are clean from paint, grease and dirt. The only method
that will properly clean aluminum is the use of a stainless steel
wire brush (Part #40112 or #40110).
Technique
– Aluminum also requires a slightly different
technique when welding. The gas nozzle should be held
perpendicular to the welding surface and inclined 5 to 15
degrees away from the direction of travel. The motion of the
welding gun should be consistent and at a greater speed than
used for welding steel. To minimize the chances of producing
a black, sooty weld, you should always "Push the Weld".
Aluminum will require a much higher were feed rate than
steel for the same heat setting and same wire diameter.
Aluminum also has a very narrow heat range in which it can
be welded. When you first start to weld, you will notice the
weld has a tendency to sit up on top of the metal and not
penetrate. If you keep welding you may see that it begins to
penetrate fine and you will get a great weld. As you continue
to welding, all of the sudden, you have overheated the metal
and blow a big hole. This is one of the problems of welding
aluminum and just requires practice to overcome.
The end of the welding wire should always be clipped off with
side cutters to aid in striking the arc.
The thermal conductivity of aluminum is much higher than
that of steel. Therefore, when welding thin gauge aluminum a
heat sink (HTP’s Heat Sponge, Part #12080 or #12084) should
be used. Aluminum hoods and trunk lids may require the
stitch welding technique if burn-through is a problem.
The tendency for aluminum spatter to adhere to the swan neck,
contact tip and gas nozzle is much greater than that for steel.
Therefore, use of the nozzle spray is extremely important.
However, the nozzle spray will act as a contaminant, so after
treating the nozzle, it is important to test weld on a piece of
scrap aluminum to "burn off" the nozzle spray.
When welding thick sections of aluminum (Cylinder Head),
many times it is helpful to preheat the area with an oxy-
acetylene welding torch. Using a rosebud tip set the torch
acetylene rich and blacken the area to be welded with a light
coat of soot. Set the torch correctly, and begin to evenly heat
the part. Let the heat within the part (not the torch) burn off
the soot. When the soot has burned off, the part has been
sufficiently preheated.
CAUTION – Aluminum does not change color when hot.
Welding Muffler Pipe
Muffler pipe welding is generally done with the conical
nozzle installed on the welding gun. The conical nozzle is
used because the taper in the nozzle makes it easier to see the
welding process and allows you to weld in tighter spots.
Prior to welding two pieces of muffler pipe together, it is
recommended that two to three tack welds be placed around
the pipe. The tack welds will help hold the pipe in place while
welding, and also prevent gaps caused by warpage.
Have 1/4" to 1/2" of welding wire protruding from the end
of the gas nozzle. Have the welding gun inclined at a 45-
degree angle to the pipe. Aim the welding wire at the spot
to be tacked and momentarily depress the trigger. Hold
the trigger long enough for the welding sound to smooth
out (approximately one to two seconds). Tack welding is
generally done at the same power setting that normal pipe
welding would be welded.
12
Muffler Pipe
Содержание MIG 2400
Страница 21: ...21 HTP MIG 2400 Wiring Diagram...
Страница 22: ...22 Parts List MIG 2400...