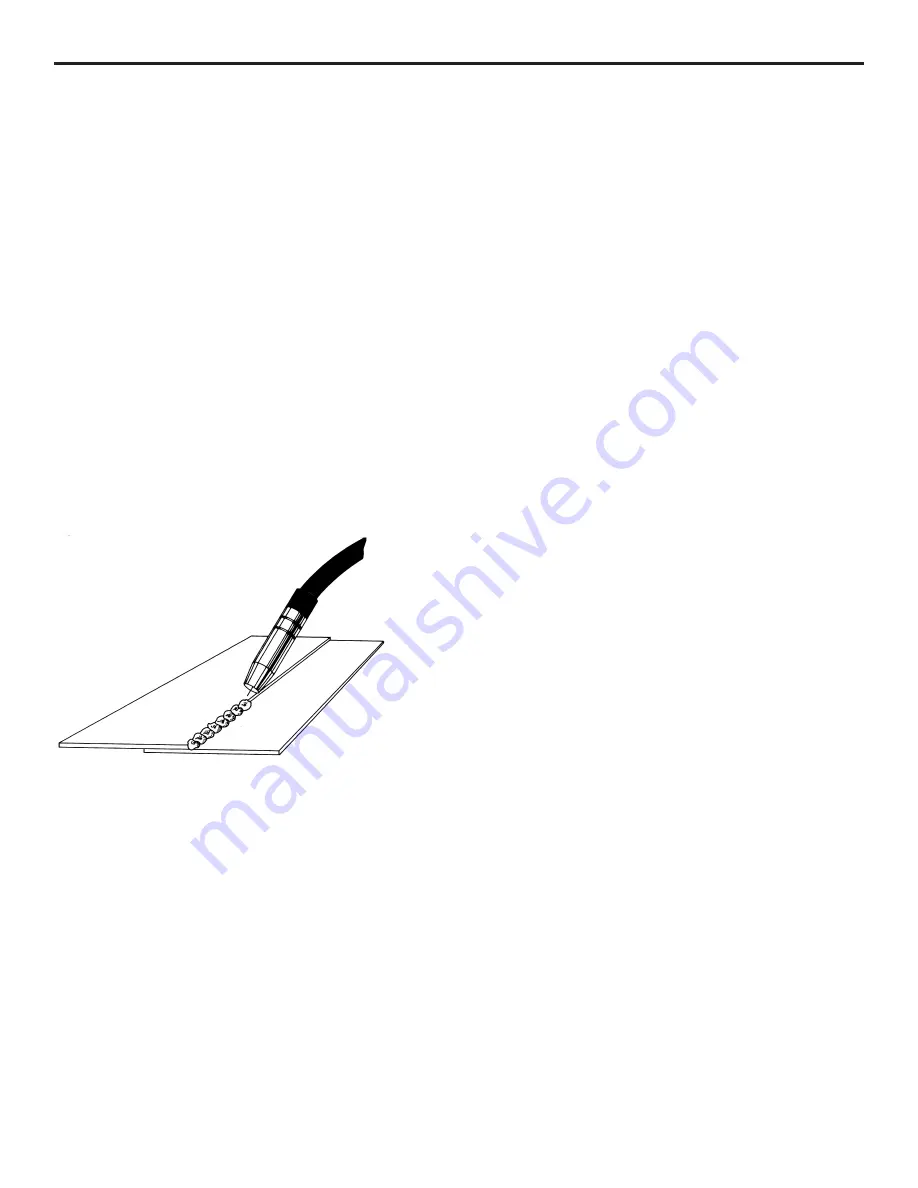
Stitch Welding
Your HTP MIG 2400 can perform a manual stitch weld.
Stitch welding refers to a method of welding where you will
weld, pause, weld, pause and continue in this cycle. This
method produces a welded seam which is actually a series
of overlapping spot welds that give the appearance of "Fish
Scales". Stitch Welding is recommended for use on very
thin materials, such as thin body panels or rusty exhaust pipe
and in areas where is desired to keep warpage to a minimum.
Stitch welding is also good for welders who have a problem
keeping a steady hand, or maintaining a constant travel rate.
Stitch welding is performed with either the conical nozzle
(#S4328) or the cylindrical nozzle (#S4330) and the decision
is up to the operator. For manual stitch welding, the trigger
on the welding gun is depressed until 3/16" diameter puddle
of metal is deposited on the workpiece. Release the trigger
and move the welding gun so that the center of the next puddle
will lie on the edge of the first puddle. Wait for the orange
glow from the first puddle to disappear and deposit the second
puddle of metal. Continue this process until the seam is
completed.
For a given thickness of metal, stitch welding is performed
at the same or one power setting lower than seam welding.
Stitch welding can be done on both steel and aluminum, and
is recommended under 120 amps. Stitch welding at higher
power settings can result in serious burnback problems.
Metal Shrinking
Metal Shrinking is done with the optional shrinking
attachment (Part #15003). Remove the contact tip. Release
the pressure on the pressure roller and swing pressure roller
out of the way. Reel enough welding wire back onto the spool
so that the shrinking attachment can be screwed into the swan
neck. Turn off the shield gas. You are now ready to shrink.
Shrinking with your shrinking attachment is similar with
any oxy-acetylene torch; the area is alternately heated and
cooled until properly shrunk. The advantage to the shrinking
attachment is that the heat is applied directly, the heat is much
more concentrated, and there is less chance of fire because
there are no open flames.
WARNING: SHRINKING SHOULD ONLY BE DONE WITH
THE COARSE POWER SWITCH IN POSITION 1 AND THE
FINE POWER SWITCH IN POSITION 1
Spot Welding
Install the spot weld nozzle (Part #S4329) on the welding
gun. Using the Punch & Flange Tool (Part #12005 {5/16"}
or #12003 {3/16"}) or the Heavy Duty Hole Punch (#12009)
punch holes in the upper panel to be spotted on. Feed some
welding wire out past the end of the spot weld nozzle. Using
sidecutters, clip the welding wire off flush with the end of
the spot weld prongs. This will aid you in centering the gas
nozzle over the punched hole.
Use a relatively high power setting, probably a minimum of
3 on the coarse setting, but it all depends on the thickness of
sheet metal you are working with.
Turn the power selector to position 3 on the coarse setting
and setting 3, 4, 5 or 6 on the fine setting (3 or 4 for thin
sheet metal, 6 for heavier sheet metal). Tune in the wire
feed rate until the proper frying noise is heard. Reduce the
wire feed rate just until the machine begins to sound out of
tune. A slightly slower wire feed rate will produce flatter
spot welds, however, do not reduce the wire feed rate when
performing overhead spot welds. Turn the spot weld timer
on to approximately 2. Place the welding gun so that the
welding wire is centered over the punched hole (see fig. 7).
Depress the trigger on the welding gun. Your welder will
stop automatically. Examine the spot weld. If the hole is not
completely full, either the welding wire was not centered over
the hole or there was not enough spot weld time. The spot
10
Figure 6
“Stitch Welding”
Содержание MIG 2400
Страница 21: ...21 HTP MIG 2400 Wiring Diagram...
Страница 22: ...22 Parts List MIG 2400...