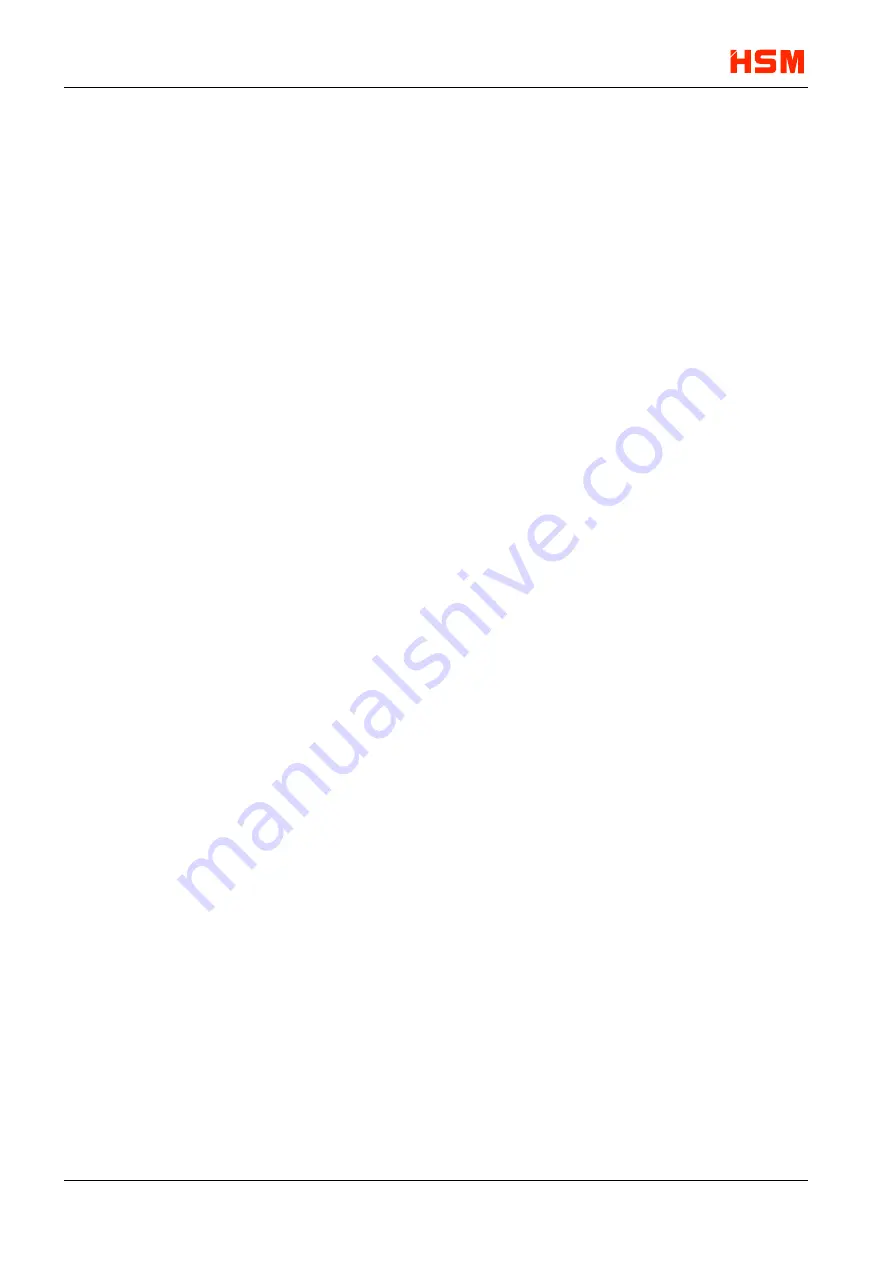
6.417.999.120
Issued 06/2005
1.2
Safety informations
VK 5012
1.3
Operating safety instructions
The HSM baling press has been inspected for safety by the examination board of
the technical committee on printing and paper processing.
The baling press has been built with the most up-to-date technology. However, the
machine can be dangerous if improperly used, even by trained staff, or if used for
purposes other than those for which it was designed.
Anyone in the operating company charged with installation, assembly, reassembly,
start-up, operation, inspection, maintenance or repair of the baling press must have
first read and fully understood the entire operating manual, paying particular
attention to the “Safety” section.
The operating manual must be kept available for staff at all times.
The baling press may not be operated by anyone under 16 years of age.
The baling press may only be operated, serviced and repaired by authorised,
trained staff. These staff must have been given special instructions on any dangers
which may possibly arise.
Areas of personal responsibility for installation, assembly, re-assembly, set-up,
operation and maintenance must be clearly defined and strictly adhered to, in order
to avoid confusion which might compromise safety.
When carrying out installation, disassembly, re-assembly, maintenance, operation,
adjustment and repair work always observe the shut-down procedures described in
the operating manual.
Never use any working practices which may be detrimental to the safety of the
baling press.
The operator must ensure that only authorised staff work on the baling press.
The operator must immediately report any changes in the baling press which impair
safety and shut down the machine until the problem has been resolved.
The user must undertake never to use the baling press unless it is in perfect working
order.
The user must ensure that the workplace at the baling press is clean and tidy by
means of appropriate instructions and inspections.
Unauthorised modifications which may impair the safety of the baling press are not
permitted. Protective devices may not be removed or otherwise rendered
inoperative.
No work may be performed on the machine while it is running.
Содержание VK 5012
Страница 16: ...6 417 999 120 Issued 06 2005 General information VK 5012 2 4 ...
Страница 17: ...6 417 999 120 Issued 06 2005 VK 5012 Technical data 3 1 3 Technical data 3 1 Dimensions ...
Страница 24: ...6 417 999 120 Issued 06 2005 Technical data VK 5012 3 8 ...
Страница 28: ...6 417 999 120 Installation VK 5012 Issued 06 2005 4 4 ...
Страница 64: ...6 417 999 120 Installation VK 5012 Issued 06 2005 5 36 ...
Страница 92: ...Spare parts and accessories VK 5012 6 417 999 120 Issued 06 2005 7 2 ...
Страница 94: ......
Страница 95: ......
Страница 96: ......