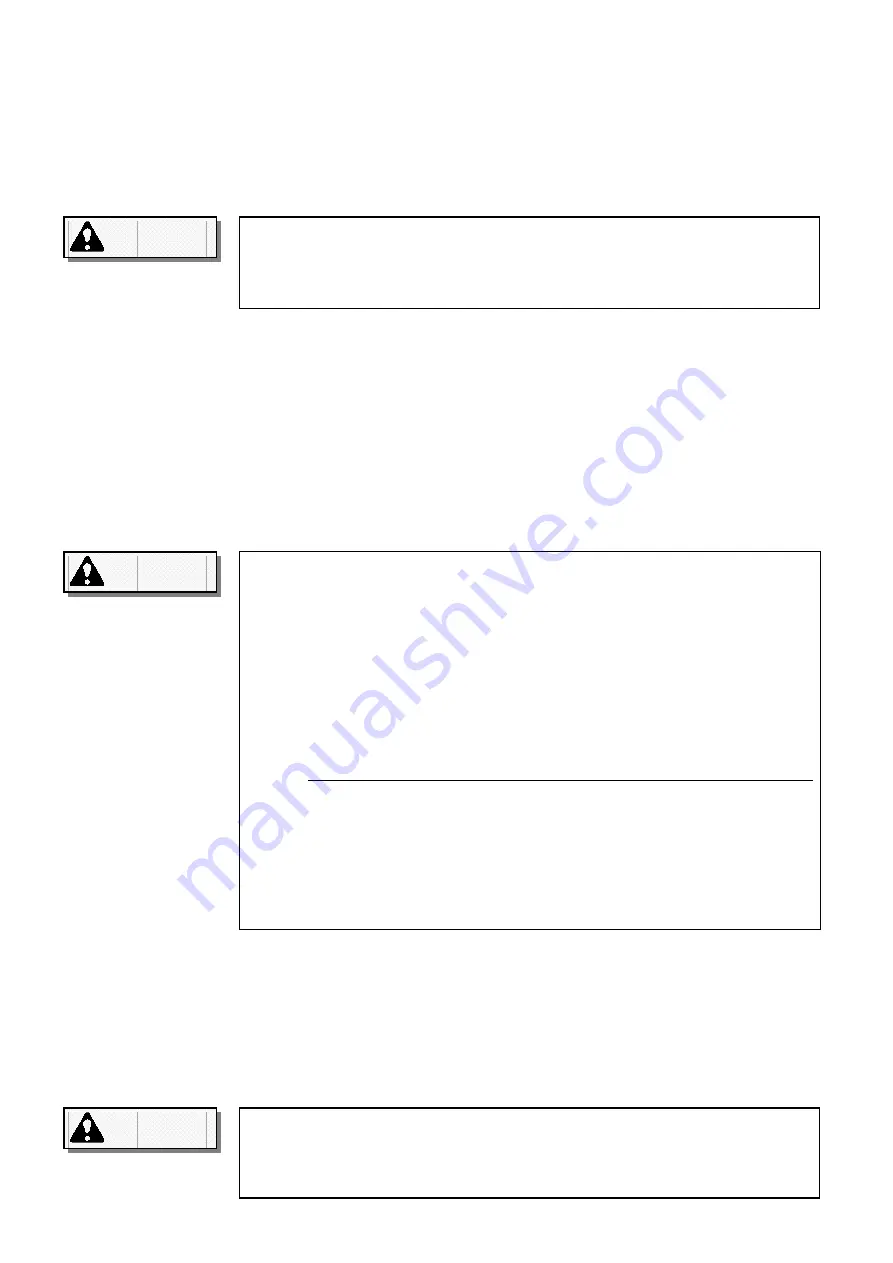
- -
12
3.4 Installing Stopper
The draw down chuck cannot grip stably if the work piece is not positioned in the chuck's axial
turning direction. To position the work piece here, the work piece must be pressed against the
chuck's work face, but in some cases, depending on the work piece configuration, a stopper
has to be equipped on the front face of the chuck. When designing a stopper, obtain Howa
approval of the stopper drawings. Accidents which occur using a stopper not approved by Howa
at the engineering design stage will not be Howa's responsibility.
3.5 Setting Working Conditions
The chuck using conditions includes not only cutting force but also many factors such as cutting
force, work gripping length, work protruding length, friction coefficient, and rotational speed. In
order to determine the ideal working conditions, all of these factors must be given due
consideration, with considerable time necessary to perform the calculations.
The "VDI Standard No 3 106" put out by the German Technicians Association is a good
reference in this regard. For your copy, write:
Beuth Verlag GmbH Postfach 1 145
NOTE: 1000 Berlin 30 West Germany
NOTE
:
Howa is happy to send you a copy of the English version of the above standard upon
request.
3.5.1 Permissible Cylinder Force
The permissible cylinder force indicated in the specification table or catalogue is the maximum
cylinder force at which the chuck will not suffer damage, presuming those standard soft jaws
are used. This maximum force may be used as required, of course, but ordinarily long-term use
under conditions of maximum force is not recommended. To maintain long-term gripping
precision, one must keep sufficient work-holding force in relation to the cutting force, and with
adjustment for sufficient but not excessive gripping force the most effective performance will be
achieved.
The gripping force during rotation can be determined from the chart in
subsection 6.3 "Gripping Force". The values shown in this chart are
obtained under the following conditions.
Standard soft top jaws are installed.
The gripping force-measuring instrument is held at the middle of the
full jaw stroke.
Gripped with maximum cylinder force.
The allowable maximum rotational speed is arbitrarily determined by
Howa in consideration of the chuck performance and the strength of
each part.
Hence, this speed is not suitable to assure safety in every situation,
because it is greatly influenced by top jaw configuration, weight,
dimensions and shape, cutting force, gripping force and the
maintenance conditions. All such influencing factors fall within the realm
of user responsibility.
Excessively high rotational speeds for a given set of conditions may
cause the work piece to fly off and may, in turn, cause serious injury or
death to the operator or bystanders.
The use of excessive input force will lead to breakage of chuck
parts or bolts and sudden loss or gripping force.
If such a mishap takes place while the chuck is rotating, the work piece
may fly oft, causing severe injury or death to the operator or bystanders.
If the work piece is not positioned in the chuck's axial turning
direction, a stable grip will not be achieved.
If cutting is carried out in this state, the work piece may fly off and may
cause severe personal injury or death to the operator or bystanders.
WARNING
WARNING
WARNING
Содержание H3EF
Страница 4: ...2 M6 M8 M10 M12 M16 N m 12 1 29 4 57 9 101 161...
Страница 5: ...3 8 1 4 1 EP...
Страница 6: ...4 1 1 1 1 1 1 1 1 3 H3EF H3EF H3EF H3EF JIS 8 1 2 1 2 1 2 1 2 3 T 2 1 2 1 2 1 2 1 kg 1...
Страница 9: ...7 2 2 6 8 T I R mm 0 020 T I R mm 0 020 3 3 M12 M16 N m 101 161 6 5mm 2 5 4 2 5 4 2 5 4 2 5 4 6...
Страница 11: ...9 3 3 3 3 5 5 5 6 8 M10 M12 L1 mm 20 24 mm 15 19 mm 10 11 N m 57 9 101 5 8 9 10...
Страница 12: ...10 3 3 3 3 3 3 3 3 1 4 1 4 12 11...
Страница 14: ...12 3 4 3 4 3 4 3 4 3 5 3 5 3 5 3 5 VDI No 3106 VDI No 3106 VDI No 3106 3 5 1 3 5 1 3 5 1 3 5 1 6 3 6 3 6 3 6 3...
Страница 18: ...16 4 1 4 1 4 1 4 1 EP 8 1 4 1 EP 100 0004 1 5 1 23F TEL 0120 77 6278 FAX 03 3287 1203 17...
Страница 19: ...17 4 2 4 2 4 2 4 2 1000 4 2 1 4 2 1 4 2 1 4 2 1 M4 90 M4 90 4 2 2 4 2 2 4 2 2 4 2 2 18...
Страница 20: ...18 4 4 4 4 4 4 4 4 ANSI B11 6 1984 section 7 1 9...
Страница 22: ...20...
Страница 26: ...24 6 5 6 5 6 5 6 5 6 8 M12 L 95 16 L 105 3 B 3 B 8 B 10 B 4 B 10 B 14 1 M10 1...
Страница 27: ......