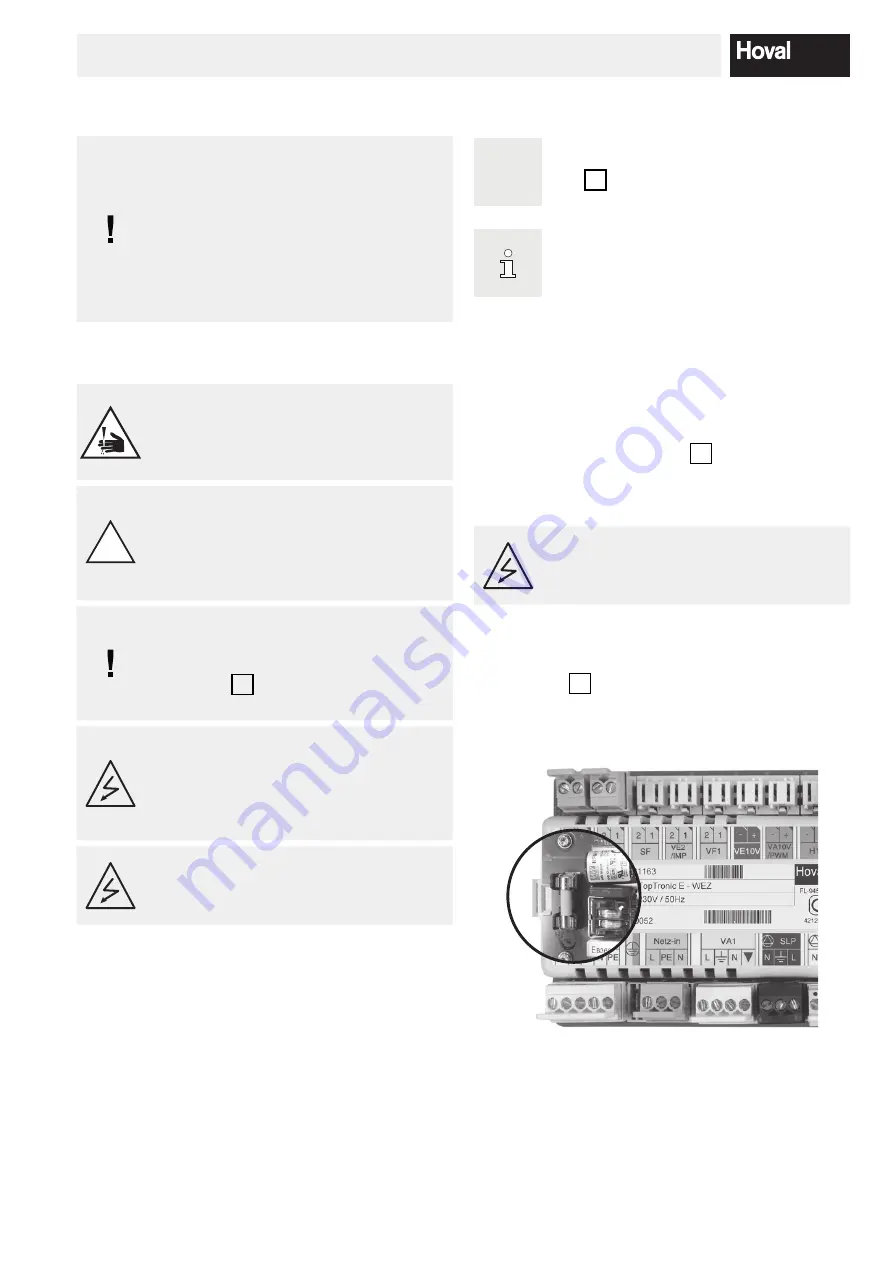
6.
Maintenance
NOTICE
Missing or faulty cleaning and maintenance
may cause damage to the installation.
The heating installation must be surveyed
and cleaned once a year.
If required, installation maintenance must be
carried out. Defects must be remedied im-
mediately in order to prevent damages to the
installation!
6.1
Safety information
CAUTION
Sharp edges pose a cutting hazard.
Handle the cladding parts with care and
avoid contact with sharp edges.
!
CAUTION
Danger of injury for unqualified personnel.
Maintenance and cleaning work may only be
performed by trained personnel or by the Ho-
val Customer Service.
NOTICE
After repair work respectively exchanging
boiler parts, a flue gas measurement accord
-
ing to point 6.7 must be carried out impera-
tively.
WARNING
The heat generator must be de-energised for
maintenance. Set the blocking switch to «0»
and disconnect the heat generator from the
mains (main switch, fuse).
WARNING
All electric power supply circuits must be
switched off before accessing the terminals.
Perform reset. See operating manual.
6.2
Bleeding
1. Open all radiator valves.
2. Heat up the system for at least half a day with a high
flow temperature.
3.
Turn off the boiler and wait 5 minutes.
4.
Bleed all the air form the system.
6.3
Water refilling
§
The European Standard EN 14868 and the
Directive VDI 2035 must be observed (see
The systems warns when the water pressure
falls below 1 bar and the boiler output is re-
duced to 50 %. If the water pressure falls be-
low 0.5 bar, the boiler is set automatically to a
fault state.
The system must be refilled with water when the pressure
falls below the minimum system pressure:
5.
Connect the filling hose to the water supply
6.
Remove the air from the filling hose
7.
Connect the filling hose to the filling and draining cock
8. Top up with water (see point 5.2).
6.4
Renewing fuse
WARNING
Electrical installations may only be carried
out by a qualified electrician.
1.
Set the blocking switch to «0» and disconnect the
heat generator from the mains (main switch, fuse).
2. Remove the front casing according to the procedure
3.
Remove the cover from TopTronic
®
E - WEZ (press to
the side and remove).
4.
Renew fuse (T 10A 250V).
Fig. 30
5.
Mount protecting cover, close casing.
6. Restore the electrical power supply.
39
4 217 213 / 01
MAINTENANCE
Содержание UltraGas 15
Страница 48: ...48 4 217 213 01...
Страница 49: ...49 4 217 213 01...