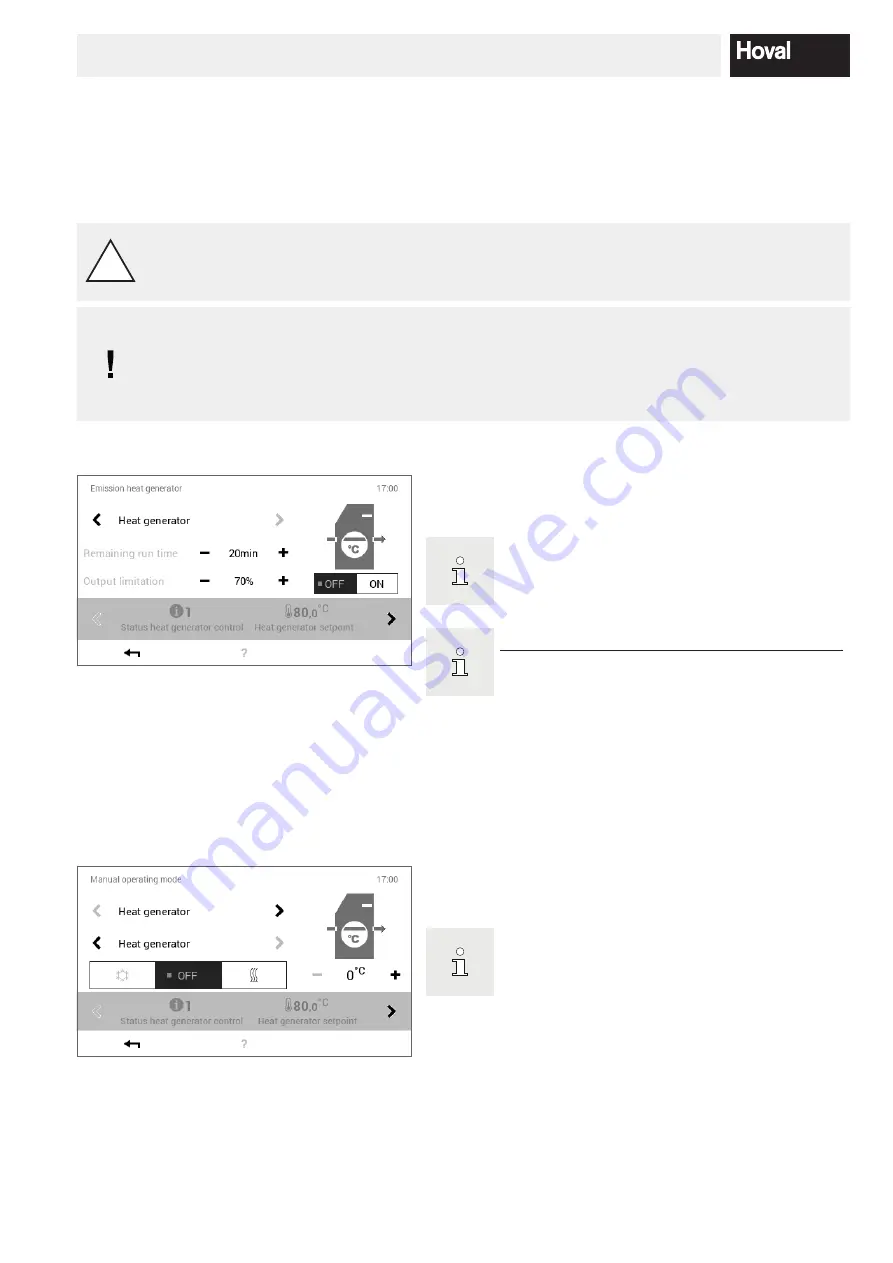
33
4 214 858 / 01
MAINTENANCE
6.
Maintenance
6.1
Information for combustion controller/chimney sweep regarding emission monitor key
This chapter is exclusively intended to describe the function of emissions and manual operation settings for the fi ring
monitoring technician / chimney sweep. All operating elements are described in the operating instructions.
!
CAUTION
Danger of scalding with hot water, since the hot water temperature can exceed the target setpoint
temperature.
NOTICE
In order to protect underfl oor heating systems against impermissible superheating during emissions
measurement / manual operation, it is necessary to implement appropriate safety measures (e.g. pump
switch-off with maximum thermostat). The output and duration of the emission measurement can be set in
the "Emission" main menu, and reactivated if required.
Emission metering
Setting at:
Home screen > Main menu (page 1) > Emission
.
For detailed information see operating instructions,
"Emission" chapter.
Power limitation with 2-stage burner:
0 to 50% = 1st stage
51 to 100% = 2nd stage
REACTION
to emission metering
•
Go back after expiry of the time unit/time specifi cation of return to the main menu
• Setpoint temperature = Maximum temperature limit
• Forced energy is used in an attempt to keep the corresponding heat generator temperature to 60 °C
•
Regulate heating circuits and the calorifi ers to their maximum temperature (in the direct heating circuit only if the hot
water basic program is set to parallel operation)
Manual mode
Settings under:
Home screen > Main menu (page 2) > Manual operation.
For detailed information see operating instructions,
"Emission" chapter.
REACTION
for manual operation
• Setting the required setpoint temperature using the selected heating or hot water circuit
• All heating pumps ON
• Note the maximum permissible temperature of surface heating!
Содержание 42-UltraOil 110
Страница 39: ...39 4 214 858 01...