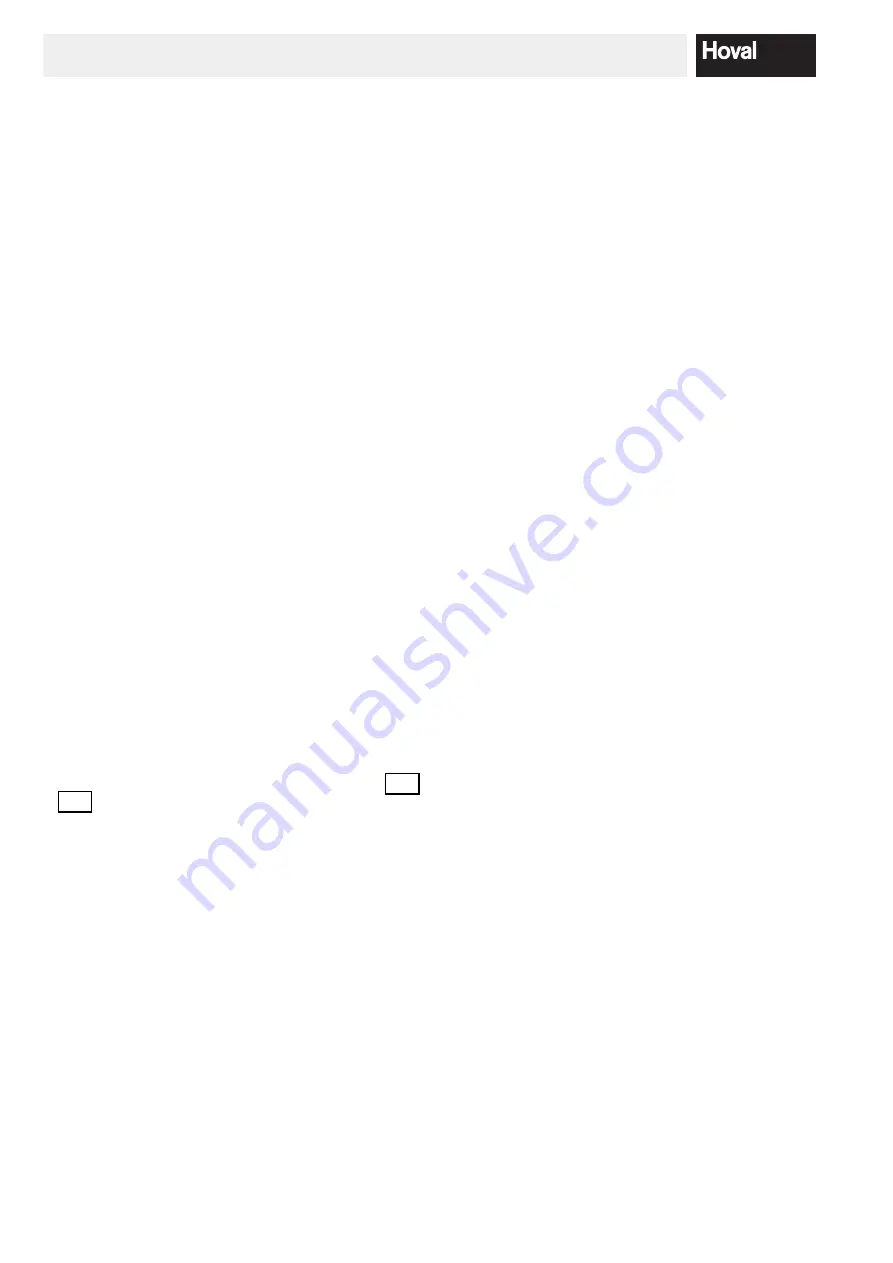
4 215 983 / 01
4
IMpORTanT nOTICES
1.3
On delivery
Carry out a visual inspection immediately on receiving the
boiler. If any damage is found, take the necessary steps
as defined in the delivery contract. The respective risk
carrier bears the cost of repairs.
1.4
Warranty
The warranty does not cover defects attributable to:
• Failure to comply with these instructions
• Failure to comply with the operating instructions
• Incorrect installation
•
Impermissible modifications to the product
• Incorrect handling of the product
• Damage caused by the application of force
• Contaminated operating materials
(gas, water, combustion air)
• Unsuitable chemical additives to the heating water
• Corrosion caused by not observing the required water
quality
• Corrosion by halogen compounds
(e.g. paints, adhesives, solvents)
1.5
Manuals
All instructions relevant to your system can be found in
the Hoval system manual please keep all manuals!
In exceptional cases, the instructions can be found with
the components!
Further sources of information:
• Hoval catalogue
• Standards, regulations
1.6
Regulations, official approvals
The standards and directives stated under chapter 1.6.1
to 1.6.3 must be taken into account during installation and
operation of the system.
1.6.1 Germany §
• DIN EN 12831 Heating systems in buildings Method
for calculation of the design heat load.
• DIN EN 303 Heating boilers with forced draught burners.
• DIN EN 12828 Sheet 1 and 2
Heating systems in buildings design of waterbased
heating systems.
•
DIN 4755 Oil-fired systems.
Design, construction and safety engineering require
ments.
•
DIN 4756 Gas-fired systems; construction, execution,
technical safety requirements, planning and execution.
•
DIN 18160 House chimneys; requirements, planning
and execution.
•
TRD 702 Steam boiler plants with calorifiers of the
group II.
• DIN EN 13384 Flue gas systems – Calculation methods
in heat and flow engineering.
• TRD 721 Safety devices against excess pressures /
safety valves / for steam boilers of Group II.
• VDI 2035 Prevention of damage by corrosion and the
formation of scale in hot water heating systems.
•
DIN 57 116 / VDI 0116 Electrical equipment for firing
systems (VDE Regulation).
• For further standards applicable in Germany, see ap
pen dix N430 020.
1.6.2 austria §
• ÖNorm 7550
•
ÖNorm B 8130 Open water heating systems;
safety devices.
•
Norm B 8131 Closed water heating systems;
safety, execution and testing requirements
•
ÖNorm B 8133 Hot water production systems;
technical safety requirements.
• ÖNorm B 8136 Heating systems, space requirements
and other building requirements.
•
ÖNorm M 7515 Calculations of dimensions of chimneys;
terminology, calculation procedure.
• ÖNorm H 5171
• ÖVGW TRgas (Austrian Gas and Water Confederation
Technical Guidelines)
1.6.3 Switzerland §
• VKF Association of Cantonal Fire Insurers
• Fire prevention authority regulations.
• SVGW Swiss Association for Gas and Water.
• SWKI 911 Aeration and ventilation of the boiler room.
• SWKI BT 10201 Water quality for building services
sys tems.
• SWKI 931 Safety engineering installations for heating
systems.
• KRW Corrosion caused by halogen compounds.
• KRW/VSO/FKR Plugin electrical connections on boil
ers and burners
and further regulations and standards issued by CEN,
CEN ELEC, DIN, VDE, DVGW, TRD and the legislative
body.
The regulations of the local building authorities, insurance
companies and chimney sweeps must also be taken into
account. The regulations of the responsible gas supply
company are to be complied with if using gas. Approval
by the authorities may be required.
Содержание 2-Max-3 condens
Страница 24: ...4 215 983 01 24...
Страница 25: ...4 215 983 01 25...