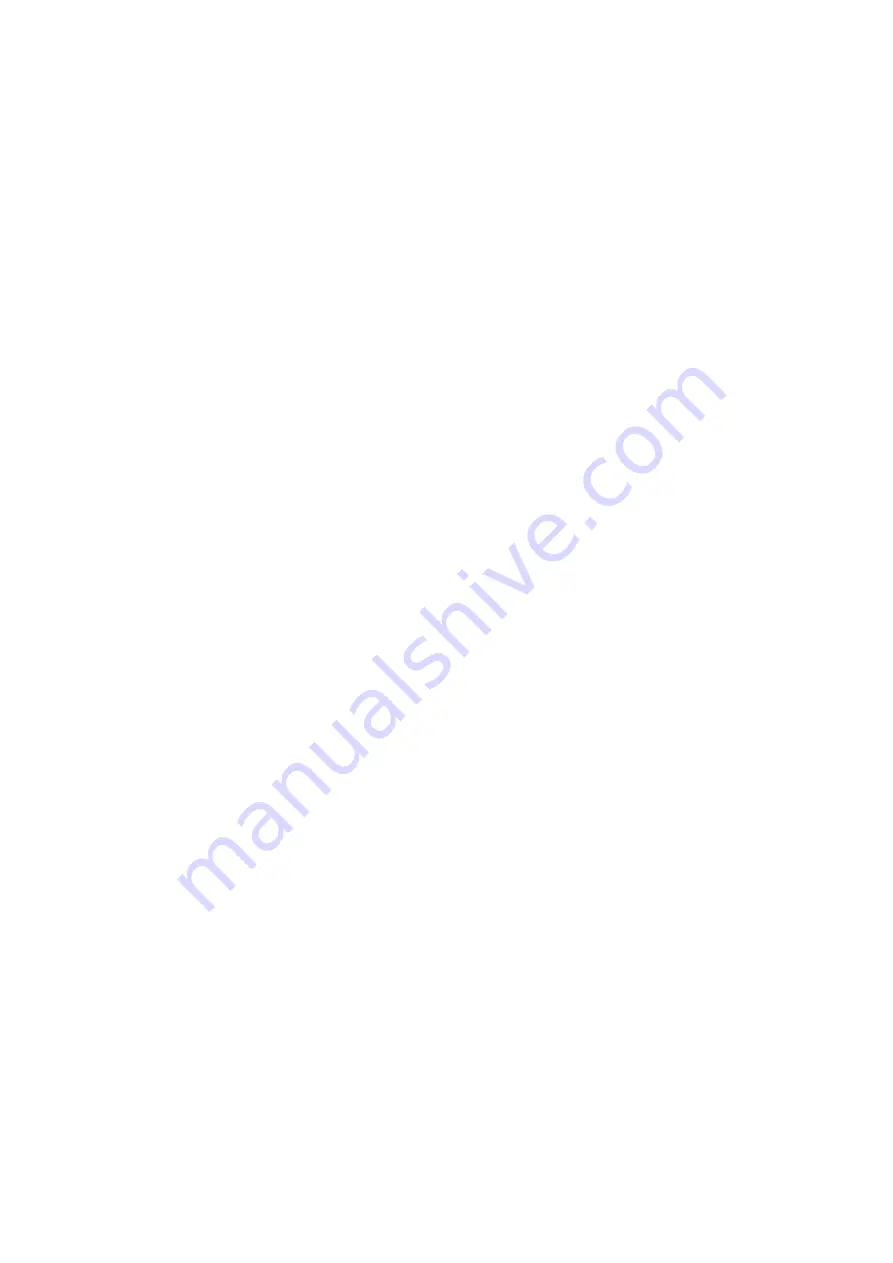
ii
IV. SERVICE DIAGNOSIS ---------------------------------------------------------------------------- 46
1. OUTPUT TEST ------------------------------------------------------------------------------------ 46
2. NO ICE PRODUCTION ------------------------------------------------------------------------- 47
3. EVAPORATOR IS FROZEN UP -------------------------------------------------------------- 50
4. LOW ICE PRODUCTION ----------------------------------------------------------------------- 51
5. ABNORMAL ICE ---------------------------------------------------------------------------------- 51
6. OTHER ---------------------------------------------------------------------------------------------- 52
V. REMOVAL AND REPLACEMENT -------------------------------------------------------------- 53
1. SERVICE FOR REFRIGERANT LINES ---------------------------------------------------- 53
[a] SERVICE INFORMATION ----------------------------------------------------------------- 53
[b] REFRIGERANT RECOVERY ------------------------------------------------------------- 54
[c] REFRIGERANT REMOVAL --------------------------------------------------------------- 54
[d] EVACUATION AND RECHARGE -------------------------------------------------------- 55
2. WELDING REPAIR FOR R290 REFRIGERATION CIRCUIT ------------------------- 56
3. COMPRESSOR ----------------------------------------------------------------------------------- 57
4. DRIER ----------------------------------------------------------------------------------------------- 58
5. HOT GAS VALVE --------------------------------------------------------------------------------- 59
6. EXPANSION VALVE - KM-80C-HC ONLY ------------------------------------------------- 61
7. FAN MOTOR --------------------------------------------------------------------------------------- 63
8. PUMP MOTOR ------------------------------------------------------------------------------------ 64
9. WATER VALVE ------------------------------------------------------------------------------------ 65
10. DRAIN VALVE ------------------------------------------------------------------------------------- 66
11. FLOAT SWITCH ---------------------------------------------------------------------------------- 67
[a] KM-40C-HC, KM-60C-HC ------------------------------------------------------------------ 67
[b] KM-80C-HC ------------------------------------------------------------------------------------ 68
12. BIN CONTROL SWITCH ----------------------------------------------------------------------- 70
13. THERMISTOR ------------------------------------------------------------------------------------ 72
14. CONTROL BOX ---------------------------------------------------------------------------------- 73
[a] FUSE -------------------------------------------------------------------------------------------- 73
[b] FUSE HOLDER ------------------------------------------------------------------------------- 73
[c] CONTROL BOARD -------------------------------------------------------------------------- 74
[d] OPERATION BOARD ----------------------------------------------------------------------- 74
[e] SWITCHING REGULATOR ---------------------------------------------------------------- 74
[f] RELAY ------------------------------------------------------------------------------------------- 75
15. WATER TANK ------------------------------------------------------------------------------------- 75
16. CUBE GUIDE ------------------------------------------------------------------------------------- 77
17. SEPARATOR -------------------------------------------------------------------------------------- 78
18. SPRAY TUBE, WATER SUPPLY PIPE, SPRAY GUIDE ------------------------------- 78
19. DOOR, DOOR STOPPER, DOOR SPRING, HOOK, SLOPE, LOUVER ---------- 80
20. TOP PANEL, FRONT FRAME ---------------------------------------------------------------- 81
VI. CLEANING AND MAINTENANCE INSTRUCTIONS -------------------------------------- 82
1. CLEANING ----------------------------------------------------------------------------------------- 82
[a] ICEMAKING WATER SYSTEM ----------------------------------------------------------- 82
[b] PARTS ------------------------------------------------------------------------------------------ 83