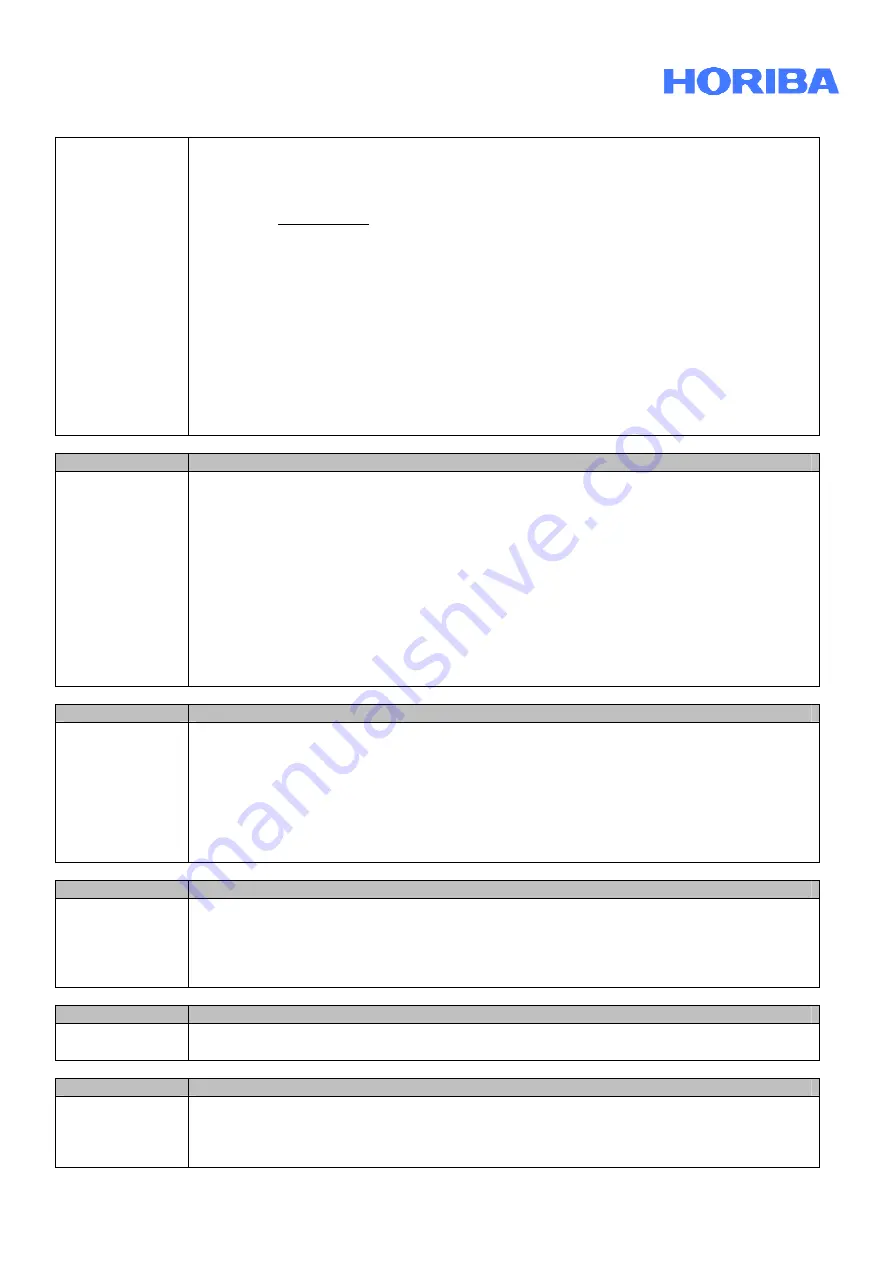
Operation Manual HORIBA APDA-371
Particulate Monitor
Date:
April, 2010
______________________________________________________________________________________________________________________
______________________________________________________________________________________________________________________
HORIBA Europe GmbH, Julius-Kronenberg-Str. 9, D-42799 Leichlingen, Telefon: +49(0)2175-8978-0, Fax: +49(0)2175-8978-50
Page 47
•
Verify the collocation setup requirements, especially making sure the inlets are
spaced correctly and the same height.
•
If the analog output of the APDA is being logged by an external datalogger, make
SURE the logger’s scaling of the APDA output is correct! In most cases, a 0.000
volt analog output on the APDA does NOT equal 0.000mg, but rather -0.015 or -
0.005mg. See Section 6.2 and Section 8. Periodically verify that the digital data log
from the APDA matches the external logger data.
•
Single event FRM samplers often perform better than multi-channel FRM samplers.
If a multi-channel unit is used, then filter collection must still be performed on a daily
basis. If the FRM filters are not properly collected and retained every day, then
correlation results with the APDA can suffer.
•
The daily 24-hour average of the APDA hourly values is calculated externally from
the APDA. It is important that the 24 hours worth of APDA data used for correlation
to the FRM is the same 24 hour period in which the sampler schedule is run. For
example, if the FRM is scheduled to stop for filter changes at 9:00 am each day, but
APDA data used for that same day is from midnight to midnight, then a bias can
result.
Problem:
The unit logs frequent “L” Power Failure errors.
Cause/Solution:
•
The 5 volt DC power supply output must be set to 5.25 volts. Contact the Service
dept for instructions to check or adjust this.
•
The CHASSIS terminal needs to be connected to a good earth ground.
•
Try plugging the APDA into a computer-style UPS.
•
Even a split second power failure will cause an “L” error. This will interrupt the
sample cycle until the top of the next hour.
•
Local high power RF fields must be avoided if possible.
•
Some vintages of the DC power supply used in the APDA can be prone to
oxidization which can cause the unit to reset frequently. Upgrade parts may be
available for certain units. Contact the Service department.
•
Rarely, some older 220 volt units can experience resets caused by the Smart
Heater control wiring inside the APDA. Contact the Service department.
Problem:
The APDA data shows repeated concentration values hour after hour.
Cause/Solution:
•
Certain error flags, such as the “T” (tape broken) flag will cause the APDA to repeat
the last known good concentration value until the error is resolved. Check the error
log to identify any errors for those hours.
•
If the RANGE setting on the APDA is set higher than 1.000mg, them the resolution
of the A/D system is reduced to 2 micrograms. If the ambient air concentrations do
not vary much over several hours, then the APDA data may show repeated values
due to lost resolution. Leave the RANGE set to 1.000mg unless very high
concentrations are expected.
Problem:
Frequent “D” membrane density errors.
Cause/Solution:
•
This usually indicates the membrane foil surface is dirty or damaged. It can be
cleaned with water rinse. Damaged membranes must be replaced.
•
The membrane assembly may not be fully extending or retracting properly, which
causes the metal part of the assembly to partially or completely block the beta
particles. Check the membrane motion.
Problem:
The clock settings are lost when the unit is powered down.
Cause/Solution:
•
The lithium battery on the 3230 circuit board may need to be replaced after about 10
years. It is normal for the clock to drift as much as 1 minute per month.
Problem:
The filter tape keeps breaking during normal operation.
Cause/Solution:
•
The photo sensors which watch the tape transport motion may be out of alignment.
Check the photo sensors as described by section 7.16.
•
This is sometimes caused by misalignment of the “SHUTTLE” photo sensor or the
interrupter flag on the end of shuttle beam inside the APDA.