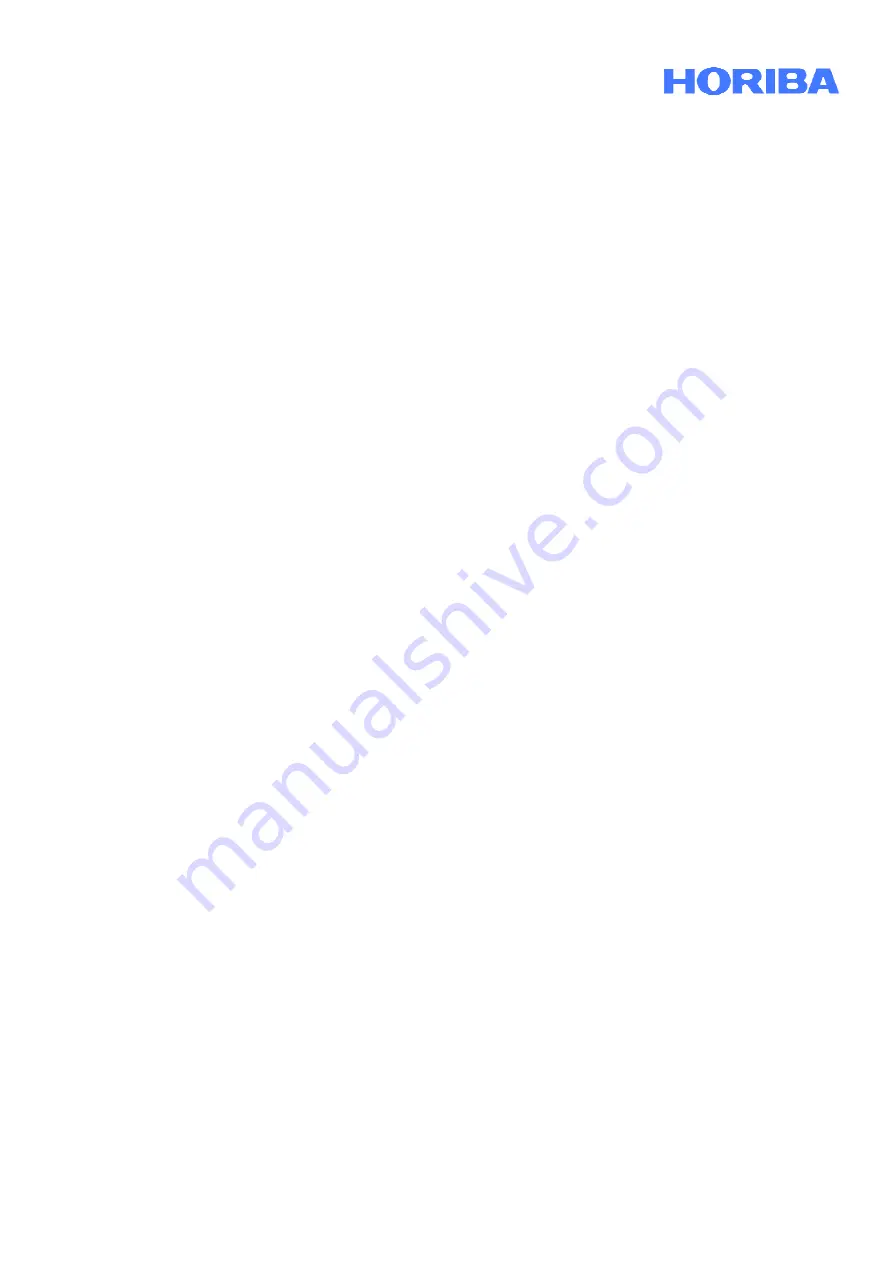
Operation Manual HORIBA APDA-371
Particulate Monitor
Date:
April, 2010
______________________________________________________________________________________________________________________
______________________________________________________________________________________________________________________
HORIBA Europe GmbH, Julius-Kronenberg-Str. 9, D-42799 Leichlingen, Telefon: +49(0)2175-8978-0, Fax: +49(0)2175-8978-50
Page 29
1.
Remove any PM
10
and PM
2.5
heads from the inlet tube. Install a BX-305 or BX-302 leak test valve (or equivalent
valve for auditing FRM samplers) onto the inlet tube. Turn the valve to the OFF position to prevent any air from
entering the inlet tube.
2.
In the TEST > TAPE menu, advance the tape to a fresh, unused spot.
3.
In the TEST > PUMP menu, turn on the pump. The flow rate should drop below 1.0 lpm. If the leak flow value is
1.0 lpm or greater, then the nozzle and vane need cleaning, or there may be another small leak in the system.
4.
Resolve the leak and perform the check again. A properly functioning APDA with a clean nozzle and vane will
usually have a leak value of about 0.5 lpm or less using this method, depending on the type of pump used.
5.
Turn the pump off, remove the leak test valve, and re-install the inlet heads.
NOTES: The reason for the 1.0 lpm leak flow allowance is due to the test conditions. With the inlet shut off the vacuum
in the system is very high, about 21 in Hg. This is many times greater than the APDA-371 will encounter during normal
sampling. If the leak reading during this test is less than 1.0 lpm, there should not be a significant leak during normal
operation.
Some agencies choose to adopt tighter tolerances for the leak test, such as requiring a leak value of 0.5 lpm or less
after the nozzle and vane are cleaned. Most agencies perform as-found leak checks (before cleaning the nozzle and
vane) for data validation purposes, since it is often necessary to invalidate data from a APDA which is found to have a
significant leak, all the way back to the last known good leak test. The typical recommended threshold for invalidating
data is an as-found leak value (before cleaning nozzle and vane) of 1.5 lpm or higher. Again, some agencies adopt
tighter standards, such as invalidating data if the as-found leak value is greater than 1.0 lpm.
5.4
Leak Isolation and Nozzle Seal Methods
Leaks can be further isolated using a soft rubber sheet with a ¼” hole in it, such as HORIBA part 7440. The filter tape
can be removed and the rubber seal inserted with the hole centered under the nozzle. The seal allows the leak check to
be performed as usual, but without any leakage through the filter tape. The leak value should drop to 0.2 lpm or less
with this method. A leak can be further isolated by using a part of the seal without a hole. This allows a leak test to be
performed only on the system below the filter tape junction. If the nozzle and vane are thoroughly clean, but a leak
persists, then see Section 7.5 for some troubleshooting steps for leaks in other parts of the flow system.
5.5
Nozzle and Vane Cleaning
The nozzle and vane (located under the nozzle) must be cleaned regularly to prevent leaks and measurement errors.
The cleaning must be done at least each time the filter tape is changed, though monthly cleaning is highly
recommended. Some sites will require more frequent cleaning as determined by the site administrator. The worst
environment for nozzle contamination seems to be hot, humid environments. This is because damp filter tape fibers
more easily stick to the nozzle and vane. The fibers can quickly build up and dry out, creating air leaks or even
punching small holes in the filter tape. This will cause measurement errors. Use the following steps to clean the parts.
Refer to the photos below.
1.
Raise the nozzle in the TEST > PUMP menu. Remove the filter tape (if installed) from the nozzle area. It is not
necessary to completely remove the tape from the unit.
2.
With the nozzle up, use a small flashlight to inspect the cross-hair vane.
3.
Clean the vane with a cotton-tipped applicator and isopropyl alcohol. Hardened deposits may have to be
carefully scraped off with the wooden end of the applicator or a dental pick or similar tool.
4.
Lower the nozzle in the TEST > PUMP menu. Lift the nozzle with your finger and insert another cotton swab
with alcohol between the nozzle and the vane. Let the nozzle press down onto the swab with its spring
pressure.
5.
Use your fingers to rotate the nozzle while keeping the swab in place. A few rotations should clean the nozzle
lip.
6.
Repeat the nozzle cleaning until the swabs come out clean.
7.
Inspect the nozzle lip and vane for any burrs which may cause leaks or tape damage.